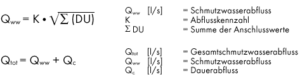
Waste water drainage
The wastewater discharge Qww according to DIN EN 12056-2, is determined from the sum of the connected loads (DU), taking into account the simultaneity, where K is the guide value for the discharge coefficient. It depends on the type of building and results from the frequency of use of the drainage objects.
Qww – wastewater discharge (calculated flow)
K – discharge coefficient
DU – connection value of unit
Qtot – total wastewater discharge
Qs – continous wastewater discharge (without simultaneity reduction)
From the sum DU, the wastewater discharge Qww can be calculated with the above formula, taking into account the corresponding discharge coefficient K. If the determined wastewater discharge Qww is smaller than the largest connected value of a single drainage object, the latter is decisive (limit value).
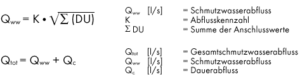