The following applies approximately:
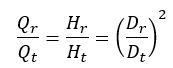
Q = flow rate
H = delivery head
D = impeller diameter
r = index for the reduced impeller diameter
t = index for the reference wheel diameter
The throttle curve H (Q) can be roughly determined from this relationship.
A more precise calculation, however, requires the consideration of performance charts in which an impeller diameter is assigned to each performance curve. The new performance curve is determined by interpolating the conversion from the neighboring curves. In order to fully utilize the efficiency of the method, it is recommended to record an duty chart with at least three performance curves. If there is a large difference between the smallest and largest impeller diameter, some (2..4) intermediate curves are required.
An alternative calculation method is described in ISO 9906. Knowledge of the mean impeller diameter at the leading edge D
1 is required here. According to the standard, this procedure is valid for
-
- Diameter reduction up to max. 5%
- Type number K ≤ 1.5
- Unchanged blade geometry (outlet angle, tapering, etc.) after cutting
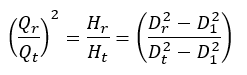
D
1 = Mean diameter at the impeller leading edge
For pumps with a type number K ≤ 1.0 and a maximum impeller diameter reduction of 3%, the efficiency can be considered as unaltered.
The point is composed of the volume flow Q and the flow rate H.
To calculate the design point, the required volume flow (flow rate of the pump) is first determined. Depending on the application, this can depend on various variables (e.g. heat requirement for heating systems, volume of wastewater produced, etc.). The calculated volume flow is then used to determine the frictional losses of the pipeline, which together with the static head then gives the total head of the pump.
If a minimum flow velocity is specified for the application and this is not reached for the calculated flow rate, the rated flow rate is adjusted so that the minimum flow velocity is reached. The pump then runs in off mode (intermittent).
The duty point of the system is the required operating point for the pump selection. The standard pumps usually have a deviation between the desired duty point and the actual operating point. The permissible deviation depends on the field of application and is partly regulated by applicable standards.
With speed-controlled pumps, the speed of the pump is modified so that the set operating point is approached exactly. Especially in systems that are operated in different load conditions (e.g. heating system), this enables efficient operation.
Depending on the design of the pump, there are further possibilities for adapting the pump performance curve to the duty point. In addition to changing the speed, the following methods are widely used:
- Impeller trimming
- Blade angle adjustment for axial flow pumps
- Throttling
- Bypass
This converts the mechanical power transmitted by the drive (motor) via the pump shaft into pumping power.