GEA Builds World’s First Carbon-Neutral Juice Production Facility for Innocent
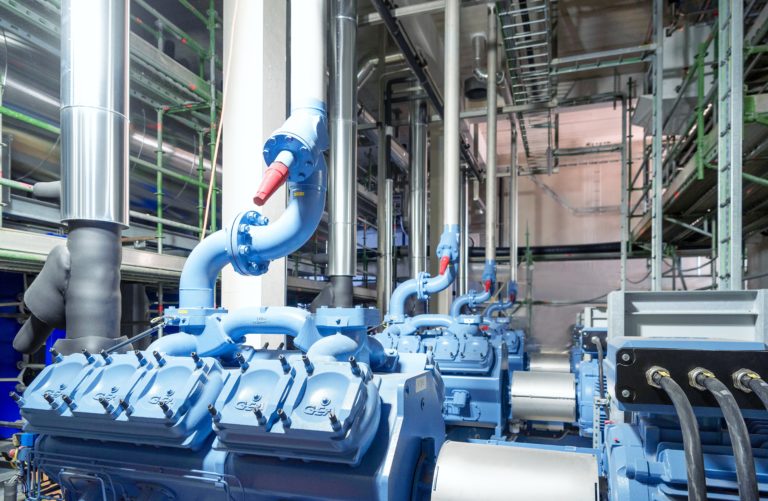
The intelligent heat pump design in combination with the process adaptations convinced the audience at the Heat Pump Awards 2021: GEA and innocent drinks jointly won gold in the People's Choice Award of the European Heat Pump Association (EHPA) for the new juice factory. Every year, the EHPA honors the most efficient and sustainable heat pump solutions with the Heat Pump Award. (Image source: GEA Group Aktiengesellschaft)
Located at the Rotterdam Food Hub, the production facility is scheduled to open officially in spring 2022.
In the new-build project, GEA is responsible for the process, refrigeration and heating technology. Early involvement in the design planning phase enabled the company to develop numerous innovative process changes that significantly help innocent on the path to reaching its climate goals. GEA and innocent recently won gold in the European Heat Pump Association (EHPA) People’s Choice Award for the smart heat pump design.
“The innocent project is an outstanding example of how we put our purpose of ‘engineering for a better world’ into practice,” said GEA CEO Stefan Klebert. “Not only have we integrated the most resource-efficient technologies, we have also entirely rethought the processes as well as the heating and refrigeration systems. Together with innocent, we have pushed the envelope beyond standard beverage production practice.”
Energy supply and demand cycle
Since much of the energy used in production is for heat, GEA worked intensively on in-process energy and resource efficiency in the manufacturing process. During the planning process, the project participants scrutinized every step: Could certain processes run at a lower temperature without impacting quality? Could the water needed for pasteurization be heated using waste heat from the refrigeration plant? What temperatures are new electric heat pumps capable of producing? Where is steam really necessary as a medium? For innocent, GEA broke down the entire juice-making process into its component parts and then rebuilt it from the ground up. The company also applied the sustainable energy solutions (SEnS) approach. This factors heating and cooling requirements into the systems right at the planning stage, instead of after the fact when corrections are virtually no longer possible.
Adapting the process on utilities demand
For example, a GEA heat pump will recover waste heat from the refrigeration systems and reuse it in other process steps. The pasteurization temperatures can be lowered from 95°C to 90°C – improving the energy balance by three percent. This makes it possible to fit a heat pump and thaw frozen juices with warm water instead of steam. GEA advised innocent to use two separate heating circuits – one set to 65°C for cleaning and the other to 90°C for pasteurization and sterilization. What’s more, innocent will only cool the juices as much as is absolutely necessary because every degree that the mercury doesn’t need to fall improves energy efficiency by no fewer than four percent.
Taking a 360-degree view of the process chain will allow innocent to substantially cut its carbon footprint while massively influencing other parameters such as water consumption and waste generation. An example highlights the use of lemon juice rather than water as a natural seal flushing liquid, because the low pH value prevents bacterial growth. On top of that, GEA has developed an automated clean-in-place system that minimizes the required cleaning surface area but also leverages Fluidor’s pioneering Fluivac technology to clean pipes with air instead of water. That allows innocent to recover 98 percent of the juice from the process piping. The customer will save on water and chemical usage as well as reduce manual tasks and downtime at the manufacturing facility.
Showcase for the entire beverage industry
“I take my hat off to GEA because they have been at our side every step of the way, helping us challenge conventional design approaches. All the little details add up to a great success,” said Andy Joynson, Chief Blender (Site Director) at the new innocent plant. The new solutions implemented go far beyond conventional beverage production processes. “Food and beverage manufacturers can choose to base their future plant designs on our model. We want to inspire and support a broad-based transformation. In line with that, we are consciously inviting the industry to share in our findings—and at the same time to learn from our missteps and our successes.”
Source: GEA Group Aktiengesellschaft