In particular, the following criteria must be taken into account:
(1) General suitability of the pump type
In principle, centrifugal pumps are only suitable up to a certain viscosity, which depends on the size. A positive displacement pump should be selected for very high viscosities.
(2) Pump characteristics
The pump characteristics are usually measured with water under standard conditions. If the density and viscosity are different, the characteristics must be converted accordingly. This is usually done automatically by the pump selection software if it is a Newtonian fluid.
(3) Material selection
The selection of suitable materials is extremely important, especially if the pumped medium contains abrasive or aggressive components. Many manufacturers offer media resistance information for this. For such use, however, direct contact with the manufacturer is definitely recommended.
(4) Seal selection
In addition to the media-material resistance, the characteristics of the pumped medium must be taken into account when selecting a suitable seal. In the case of dangerous substances (e.g. toxic or explosive media) or particularly valuable fluids, it is usually necessary to use a leak-free solution. Pumps without a shaft seal with a canned motor or magnetic coupling are ideal here.
(5) Solid or gas fractions
If the pumped medium contains solid and / or gas components, special pump designs that are intended for this must be selected. For example, suitable impellers prevent the pump from blocking when there are solid or fibrous components. Gas proportions affect the suction behavior of centrifugal pumps. A higher gas content leads to an increase in the required NPSH value and thus to the earlier occurrence of cavitation.
In practice this will however become not applicable for fluids of kinematic viscosities above 20mm²/s ( 20 cst ) due to the influence of a higher Reynolds Number with increasing viscosity. Empirical conversion methods have been developed for curve corrections for medium- and high-viscous fluids, which in practical application in older versions meant the time-consuming evaluation of diagrams, but in the current versions were prepared by corresponding formula sets.
The most widespread method worldwide is the method from the Hydraulic Institute (USA), which has been standardised as ANSI/HI 9.6.7 and ISO/TR 17766. In practice, the conversion is usually carried out by computer programmes such as the Spaix PumpSelector. The computer implementation of this method enables the conversion of performance curves, whereby the user only has to define the desired delivery data and the pumped medium. The best efficiency point of the pump is of vital importance with all the known curve correction methods.
The following conditions can be stated for the validity of this method:
- Centrifugal pumps with closed or semi-open impellers
- Kinematic viscosity in the range between 1 and 3000 mm²/s
- Flow rate at best efficiency point between 3 and 410 m³/h
- Head per stage between 6 and 130 m
- Fluid displacement by means of a centrifugal pump under normal operating conditions
- Handling of Newtonian Fluids
A centrifugal pump is a hydraulic flow machine in which the transport of the pumped medium is realized by utilizing the centrifugal forces (centrifugal forces) caused by the rotation of the impeller. Energy is transferred by deflecting the flow within the impeller blades.
Centrifugal pumps are typically applied for pulse free, continuous or intermittent operation, but they are not suitable for dosing or metering applications. The strengths of this process are in the continuous, pulsation-free operation. Another advantage is the relatively simple design and good adaptability, which avoids high maintenance costs.
The application is limited with regard to the viscosity of the pumped medium. With increasing fluid viscosity the efficiency is decreasing. Therefore the application is practically limited to fluids with a kinematic viscosity up to 100 .. 150 mm²/s. For higher viscosities positive displacement pumps are preferred.
Important parameters are head, flow rate, power requirement, efficiency and NPSH value. The parameters are generally shown as performance curves depending on the volume flow (flow rate).
Newtonian fluids, at laminar flow, create shear tension and pressure super-imposed normal tensions which are proportional to the deformation velocity, the proportionality factor being the absolute viscosity.
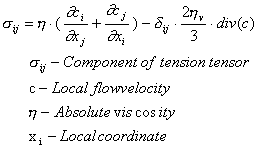
The kinematic viscosity is defined as:
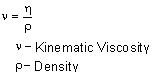
The viscosity depends on temperature and pressure, whereby pressure dependency of fluids is of negligibly small characteristics.
Viscosity of non-Newtonian fluids can moreover be time-related (thixotropic or rheopexic flow characteristics); its characteristics then becoming undefined.
The viscosity of a medium has an influence on both the system curve and the pump performance curve. For centrifugal pumps, the pump curves are converted in practice at a kinematic viscosity of more than 10 mm²/s.
This is thus indicated that there is no line coherence between deformation and shear tensors and that the viscosity rate is time-related.
Non-Newtonian flow characteristics can be observed with the following fluids:
- gaseous soot in oil varnish
- cereal corn suspensions in water
- waste water sludgesewage
- toothpaste
- mortar
- soap solutions
Examples:
Thixotropic characteristics can be observed on numerous kinds of varnishes and lacquers, that means the viscosity is time-related. On stirring with constant angular velocity a rather great resistance is being experienced at first, whilst after a time the viscosity becomes noticeable less, tending towards its lower limits.
Plastic and pseudoplastic characteristics can be observed on many industrial sludge’s e.g. suspensions of lime (mortar) and chalk (toothpaste). Below the shear rate (flow limit)they behave like solid bodies and above as fluids.
Colloidal fluids, such as caoutchouc or solution of soap in water, behave like thixotropic fluids but will not recover their original viscosity when agitation is stopped. The viscosity of such fluids decreases as agitation or shear rate is increased. The reverse (dilettante) characteristic scan be observed on some high-concentrated suspensions., their viscosity increases with increasing agitation or shear velocity rate.
Both the pump curves and the classical methods for calculation of the pipe friction loss assume a constant viscosity and are not valid for non-Newtonian fluids. Depending on the flow behaviour of the pumped medium, they can at best be used as an approximation. For many non-Newtonian media, there are therefore special calculation or approximation methods for sizing and selection.
It is, on one-dimensional flow:, physically defined as:
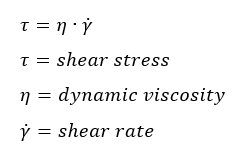
Of Newtonian fluid characteristics are e.g. the following:
- water
- oils
- gases
- mercury
- alcohol
- petrol
If it is not known whether a fluid is of Newtonian flow characteristics or not, it should be laboratory-tested.
The maximum and minimum temperatures of the pumped medium are of particular importance for the design of the pump. They are taken into account in the selection of materials and seals and, if necessary, in a media-material resistance test.
The fluid properties (density, viscosity) change with the temperature. The power requirement of the pump is directly proportional to the density. Therefore, the temperature must be taken into account from the operating range with the maximum density. Furthermore, for viscous media (ν > 10 mm²/s), the shape of the pump performance curve must be converted.
This point is called the best efficiency point (BEP) of the pump. The position of the point changes if the hydraulic parameters of the pump, such as the impeller diameter or the speed resp. the viscosity of the pumped liquid, change.
The aim of an optimal pump selection is for the pump to operate at the BEP so that it achieves its maximum efficiency.