Project-based mechanical and plant engineering: The path to saving 4,500 work hours a year
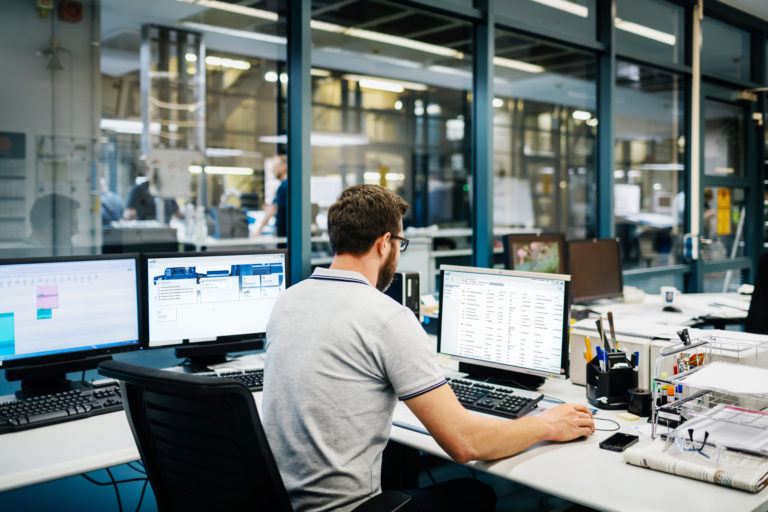
Digital supplier documentation. (Image source: Tom Werner via GettyImages)
The economic pressure faced by German machinery and plant manufacturers is notoriously high. In order to defend their leading global positioning, more and more domestic providers are turning to modern technologies in the realm of digital transformation. The spectrum spans a cross-section ranging from initiatives in areas such as Internet of Things (IoT) and its networked facilities and machines, Industry 4.0 and Smart Factory, as well as big data and artificial intelligence.
But that’s only one side of the coin. The production sector of the mechanical and plant engineering industry receives good marks in IMU’s study “Digitale Transformation im Maschinen- und Anlagenbau” (Digital transformation in mechanical and plant engineering), but when it comes to digitalization in administrative processes, a great many companies are lagging behind.
Processes that have either not been digitalized at all or only to an inadequate degree have a particularly marked impact on project management. Delays inevitably lead to customer dissatisfaction, and what’s more, if contractual obligations are not fulfilled, they result in needless additional expenses – such as costly contractual penalties. This situation is particularly acute for large-scale plants or special-purpose machinery, which involve a high number of suppliers.
The following case study illustrates how intelligent digitalization impacts internal processes in the mechanical and plant engineering industry.
In search of end-to-end digitalization
KSB Group is among the leading suppliers of high-quality pumps, valves, and related systems. Founded in Frankenthal in 1871, the company boasts a workforce of more than 15,000 people with an active presence on every continent.
Prior to implementing cloud-based supplier documentation, KSB’s project partners and suppliers exchanged information by e-mail and file attachments. There was no group-wide filing infrastructure in place that allowed for central management. Instead, critical project information was saved in various in-boxes or inside departmental systems. This came with its own set of disadvantages: It was often very laborious and time-consuming for project participants to locate certain information. It was also difficult to determine the current status of required documentation.
This escalated to a point where contractual penalties were a real risk since it was not immediately apparent that suppliers were failing to provide the necessary documentation. Gaining control of the situation meant introducing elaborate manual controls, which typically demanded a great deal of time. Thus, the time spent on deadline tracking alone in order to collect the required documentation amounted to a whopping 130 hours for every single project.
Faced with these challenges, KSB decided to implement a cloud-based platform that was designed to handle the following tasks:
- Centrally managed supplier documentation with processes that are lean and transparent to the highest possible degree
- Connection to the existing SAP system in order to link the sales order and purchase order number with the documentation
- Automatic deadline monitoring with a reminder feature
- A tool for analyzing supplier delivery performance and on-time delivery reliability with a view to mitigating risk and avoiding potential contractual penalties
- A state-of-the-art user interface and ease of use
The overall aim was to better integrate the suppliers into the process so that potential problems could be brought to their attention at an early stage. The new solution also had to support KSB’s efforts to achieve a more transparent customer-facing presence and deliver a more accurate picture of its own performance.
Realizing objectives such as those defined by KSB calls for a solution that incorporates all the desired functionality – preferably as part of the standard product. The most important pillars of any modern supplier documentation system incorporate the following aspects:
Digital supplier documentation should be cloud based to guarantee seamless collaboration across country, company, and departmental boundaries, integrating all project participants along the supply chain into a single system.
All information is stored in a central location in the cloud. With clear filing structures, status display, and integrated deadline management, all project participants always have a complete overview of the documentation status as well as all pending tasks and deadlines. In addition, every time a document is modified or released – whether internally or externally – the process can be recorded in a way that is revision-secure.
Modern supplier documentation systems are designed to enable plant and machine manufacturers to review their suppliers’ documentation efficiently and consolidate it into their total documentation so that it conforms to standards and guidelines. Rule-based completeness checks together with automated deadline management ensure that all tasks are completed on time. This makes cumbersome back-and-forth e-mail communication a thing of the past.
A digitalized end-to-end solution should have a graphical process editor that allows the user to create customized and cross-company processes – preferably without programming skills. This allows suppliers and customers to be integrated easily into the processes.
Once the processes have been defined, deadline reminders are sent out automatically to ensure that tasks are completed on time and that no deadlines and delivery dates are overlooked.
The product that is part of any modern supplier documentation solution should have numerous standardized interfaces for connecting to existing ERP (SAP), CRM, and PIM systems by default. This eliminates the need for manual data maintenance.
Document templates and centrally managed text modules can support and accelerate the creation of the overall documentation. Document templates also ensure a uniform appearance. Ready-to-use text modules, which can be used directly in a word processing program, help to ensure the consistency of formulations such as warnings.
Since many processes involve handling sensitive data, a cleverly devised role and rights model combined with two-factor authentication during login should ensure that only authorized persons have access to information and documents. This establishes clear rules as to who is permitted to view, edit, review, or approve which content. The system also logs every access to every document.
Last but not least, an intuitive, web-based user interface, which should be available in multiple languages, ensures a high level of usability.
How KSB benefits from a modern solution
By implementing a process-driven supplier documentation system based in the cloud, KSB succeeded in achieving the objectives it had defined. As one of the core requirements, the project documents are now stored centrally and accessible worldwide. Among other benefits, this means that all parties involved in an assignment – including suppliers – can retrieve the latest documentation version in accordance with their authorization rights. Another major advantage of the new system is its high level of usability. A web browser with an Internet connection is all it takes to use the system to its full potential.
Christian Strobl, Operational Procurement Pumps & Systems Pegnitz KSB SE & Co. KGaA, describes the advantages as follows: “Access to the digital supplier documentation can be handled flexibly. If we add a new supplier from Chile, for instance, they can log in just as easily as a supplier from France – without having to install software.”
Thanks to intelligent mass uploads, a great deal of time can also be saved when creating customer documentation. Uploading works in the following way: The customer’s documents are automatically renamed according to KSB’s specifications and assigned to the relevant order items of the order together with the comments. Previously these tasks had to be performed manually.
The many collaboration features available in the new platform are yet another example of how it boosts efficiency and quality in project management. For example, documents can be provided with annotations that can be viewed either by KSB employees only or by everyone involved.
In other words: With the new cloud-based and process-driven supplier documentation solution, KSB now has a single global platform for all communication, document management, and document processing with suppliers and customers.
Author: Andreas Dangl is the Business Unit Executive for cloud services at Fabasoft. In this capacity, he is responsible for the strategic positioning of Fabasoft Cloud. In addition, he consults and supports companies from a broad cross-section of industries with regard to implementing cloud solutions.