Sulzer eröffnet Produktionslinie sowie Logistikzentrum im finnischen Kotka
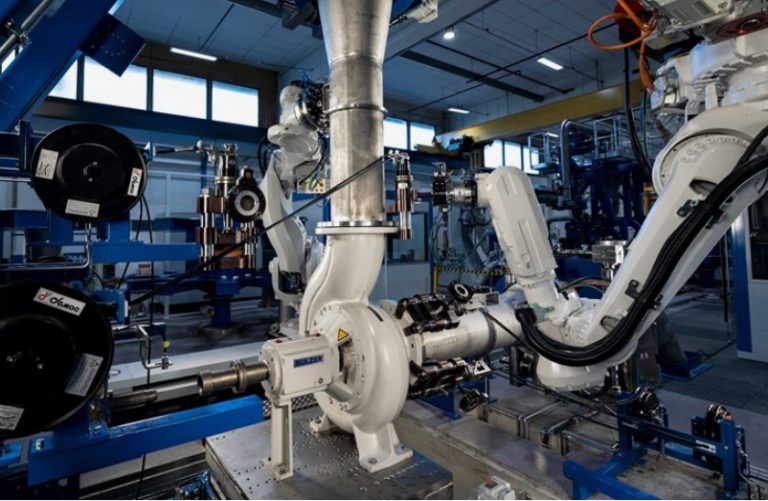
Sulzer eröffnet hoch automatisierte und digitalisierte Produktionslinie sowie Logistikzentrum im finnischen Kotka. (Bildquelle: Sulzer Ltd.)
Sulzer fertigt seit 130 Jahren Pumpen in Kotka. Mit der neuen Produktionslinie, die höchsten Industriestandards entspricht – auch in Bezug auf Ergonomie und Sicherheit – beginnt für das Unternehmen jetzt eine neue Ära. Die Durchlaufzeit in der modernen und energieeffizienten Anlage ist um 93 Prozent kürzer, was für die Kundschaft deutlich bessere Lieferzeiten bedeutet.
Stärkung der gesamten globalen Lieferkette von Sulzer
Die automatisierten Anlagen wurden mit Hilfe digitaler Technologie und nach Lean-Grundsätzen auf schnelle und effiziente Workflows ausgerichtet, um eine effektive Produktion sicherzustellen. Ein brandneues Logistikzentrum für das Material- und Komponentenhandling optimiert die Lieferkette für Materialien und trägt zur Verkürzung der Durchlaufzeiten bei. Die erhöhte Produktion im Werk Kotka wird die globale Lieferkette von Sulzer insgesamt stärken.
Die Sulzer-Fabrik in Kotka ist einer der wichtigsten Anbieter von konfigurierten Prozesspumpen, Rührwerken und schnelllaufenden Turbokompressoren für den Weltmarkt. Das Werk umfasst auch Prüfstände im Industriemassstab und Forschungseinrichtungen. Die Fabrik bedient Kundschaft aus der Prozessindustrie in Märkten wie Zellstoff, Papier und Karton, neue holzbasierte Prozesse, Biokraftstoffe, Zucker und Stärke, Metalle und Bergbau, Düngemittel, chemische Verarbeitung und Wasseraufbereitung.
Ein wichtiger Beitrag zur Gestaltung einer nachhaltigen Zukunft
„Die neue Produktionslinie ist das technologisch Modernste, was in diesem Bereich zu finden ist, und eröffnet unseren Kunden ganz neue Möglichkeiten in Bezug auf Qualität und Lieferzeiten. Ausserdem sind die Materialien, die wir für unsere hocheffizienten Pumpen verwenden, zu 99 Prozent wiederverwertbar. Die neue Anlage spiegelt damit nicht nur unser Streben nach Qualität wider, sie ist auch ein wichtiger Beitrag zur Gestaltung einer nachhaltigen Zukunft, den unsere Kunden zu schätzen wissen, und auf den unsere Mitarbeitenden stolz sein können,” sagte Veli-Pekka Tiittanen, Leiter der Business Unit Industry bei Sulzer.
Quelle: Sulzer Ltd.