Sulzer Collaborates with ANDRITZ to Support Production of 12’000 Tons of Biomethanol per Year at World Largest Plant
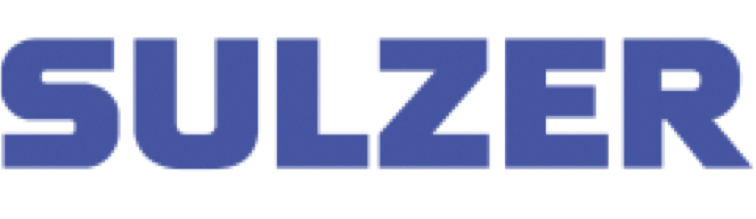
(Image source: Sulzer Ltd.)
Veolia will utilize the purification solution to convert raw pulp mill waste into commercial grade biomethanol suitable for a range of industries such as the transportation and chemical sectors.
Sulzer Chemtech’s separation technology supports removal of large volumes of impurities from biomethanol feedstock to enable Grade AA biomethanol production. High-quality biomethanol can be used by a broad range of industries, including the most demanding applications in the pulp and paper, transportation and chemical sectors.
Veolia is adopting ANDRITZ's cutting-edge technology, which was developed as part of the CircleToZero initiative. In this endeavor, ANDRITZ leverages Sulzer's ECR separation technology to transform pulp mill waste into high-quality, profitable biomethanol. Furthermore, Veolia utilizes a variety of process pumps from Sulzer to ensure the smooth and reliable operation of its plant.
Veolia’s new biomethanol purification plant – the world’s largest of its kind – will produce 12’000 tons of biomethanol per year for use in downstream chemical manufacturing or biofuel. The operation will be integrated into a local pulp mill to support circular production practices while generating additional value streams for Veolia.
Sulzer’s Chemtech Division President Uwe Boltersdorf comments: “Our market-leading technologies and products advance both sustainable energy and circular practices. Sulzer’s innovations are designed to enable efficient processes in support of bio-based and renewable manufacturing.”
ANDRITZ Sales Director Jaakko Wallenius comments: “We are delighted to see our concept contributing to the construction of the world’s largest facility for renewable methanol purification within a pulp mill. Our successful collaboration with Sulzer spans several years on a number of projects, and we anticipate continuing this partnership to deliver state-of-the-art circular infrastructures in the future.”
Source: Sulzer Ltd.