Crest Pumps: 5 Tips to Increase a Pumps Life
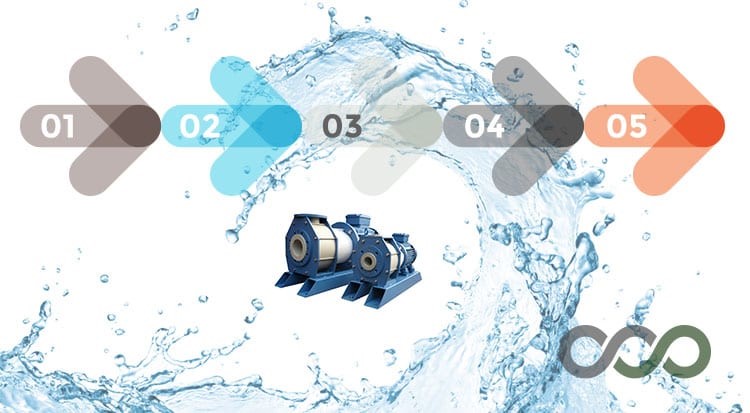
Top 5 tips to increase a pumps life. (Image source: Crest Pumps Ltd)
Material Compatibility
Using the correct pump materials are essential if the pump is to have a long life. This is especially so when handling corrosive liquids. Not only the main pump body material, but also the individual parts such as shaft/bearing/mech seal materials must be correctly specified if the pump is to last a long life.
Preventative Maintenance
Sometimes, scheduled pump maintenance is overlooked and instead left as reactive maintenance, whereby the pump is repaired if/when it fails. The risk of this strategy is that an entire process could be shut down whilst the pump is offline being repaired. The cost of carrying out a periodic maintenance procedure should be weighed up against the cost of a system shutdown should a pump fail. Also bear in mind a planned maintenance cost is likely to be much cheaper than a repair cost. Please refer to any pumps installation manual which will include recommended maintenance schedules.
Operating away from the BEP
Pumps are designed to run at the most efficient point by the manufacturer. If the pumps is run too far away from its efficiency point, this can quickly lead to excess recirculation, heat, radial loss, vibration, high seal temperature and vastly lower efficiency.. If a pump is to be used for varying duty points, we would recommend our high efficiency AVF pump range
Improper Piping
Poor piping layout can have a big effect of the pump's operation and its efficiency. Designs with in-verted "U"s on the suction side can trap air, while designs with a 90 degree bend immediately before the pump can cause turbulence inside the pump. Both could potentially result in suction and cavitation problems for the pump. Inlet pipework should be at least one size bigger than the pump inlet in order to prevent cavitation and allow best efficiency.
Do not run dry!
Under normal operating conditions, the pumped liquid acts as lubricant between the rotating and stationary parts, and the heat generated by the rotational action is gently taken away by the circulating liquid, But when a pump is starved of liquid, these moving parts generate heat from friction and as the heat builds up, damage will occur. For a mechanical seal pump, running dry could lead to pump cavitation and therefore seal damage. The mechanical seal could also experience thermal shock and under the right conditions could shatter within 30 seconds. With a mag-drive pump, the bearings and shaft can rise in temperature due to the absence of liquid lubrication and subsequently melt the plastic casing.
With the Crest Assoma mag drive range, a patented auxiliary circulations channel runs between the bearing and the magnet capsule. The pressure difference has a convection effect for cooling both the interior and exterior of the bearing thereby preventing the high temperature build up causes from dry running. The key point of this feature though, is that whilst the design allows for increased cooling, there is no reduction in pump efficiency.
Source: Crest Pumps Ltd