Automated Filling of Viscous and Chunky Snacks for Animals
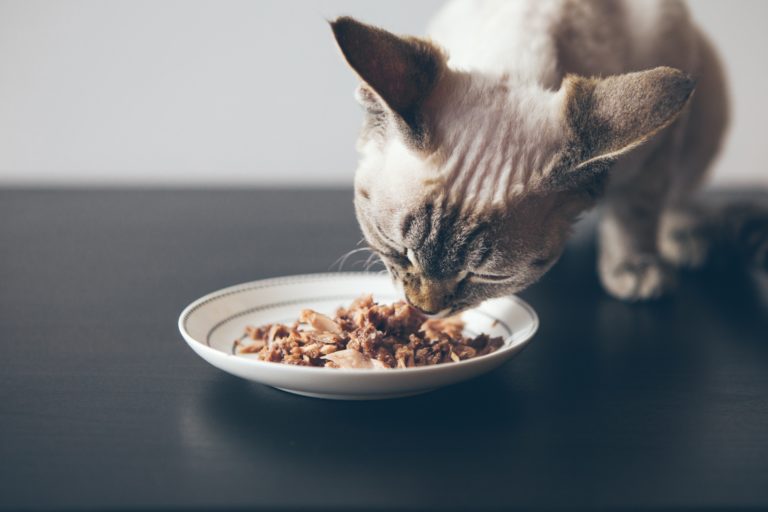
Pasteurization turns a liquid suspension loaded with solids into semi-solid feed or a snack. (Image source: Adobe Stock)
If pet food producers want to continue to meet the growing demand for pet food and the desire for variety and diversity in the coming years, they will need high-performance processing technologies that enable the conveying, filling, and dosing of ingredients.
Furthermore, the production facilities must be able to withstand what has been tested on a laboratory scale: It must be possible to increase the number of cycles or expand production capacity without major modifications to the process technology. This is also because it can be assumed that the number of dogs, cats and small mammals will increase - from an already incredible 34.9 million animals - to considerably more. And they will all need food.
Animal feed production: Flexible processes open up a variety of products
Classic dry pet food is usually produced by extrusion. Here, in automated processes, the various ingredients such as dry meat (meat powder) or other animal proteins and carbohydrates are mixed together with water to the desired recipe. After heating the mass, it is pressed through nozzles and the resulting strands are then dried and cut, to produce the pellets.
The situation is quite different for pastes and slurries, which play a major role today, especially in the dog snack market.
- Pastes are mixtures of solids and liquids, i.e., in a broader sense also slurries. However, they have a high solids content and are therefore no longer flowable, but spreadable. Pastes therefore belong to the semi-solid preparations.
- Slurries on the other hand, are coarsely dispersed systems of the "solid in liquid" type and are found in the animal feed industry in many types of feed or snacks. Industrial processing begins as a dispersed liquid in the form of jelly, sauces or creams, to which solids such as meat or vegetables are added. Pieces of 15x15x15 mm are no exception. In addition to meat or vegetables, nutritional supplements can of course be added, which also allows for the production of snacks for animals with specific health conditions. Depending on the product type, brand and the individual recipes of the manufacturers, gelatin is also often added to high-quality pet food. Collagen peptides and the natural by-products of their production, such as fats, proteins, and minerals, are also frequently added, as are abrasive ingredients such as parts of bones, tendons, and vertebrae. Gelatin has water-binding properties and gives the feed its user-friendly consistency after pasteurization.
Uniform dosing of chunky meat and vegetables in liquids
Up to this stage in the process, the suspension is in a more or less thin liquid form containing meat or vegetable components and tends to sediment. For the dosing and filling process into pouches, a process solution is required that reliably prevents this sedimentation. Similar to the pharmaceutical industry, pet food production is also subject to standards and regulations that must be complied with. For example, the Guide To Good Practice for the Manufacture of Safe Pet foods, published in 2018 by FEDIAF, explicitly addresses mixing processes and the framework conditions for homogeneity in chapter 2.5.
Once the pet food is in the primary package after dosing and filling, pasteurization takes place to kill germs and make the pet food storable for a certain period of time. Here, the liquid suspension, initially loaded with solids, becomes semi-solid feed or a snack. Pasteurization can be subdivided into specific processes depending on the temperature and the bio organisms to be killed, but these will not be discussed in detail here.
Flexible dosing and filling technology: Adjusting screw for batch quality
Liquids loaded with solids that tend to separate are not suitable for efficient industrial processing using peristaltic or piston pumps. Progressive cavity pumps represent an alternative. The technology developed by ViscoTec is one of the rotating positive displacement pumps. A stainless steel rotor moves eccentrically in an elastomer stator. This interaction of rotor and stator creates cavities that open alternately and whose size is always constant during rotation. This ensures that no blockage of the conveyed product occurs and that there are no blockages caused by solid feed components. The specific dosing geometry allows the conveying of an always constant volume proportional to the angle of rotation per revolution.
Bypass ensures a continuous process
An interesting feature for pet food production and flexibility in product mixtures and process is the option of equipping the progressive cavity pump with a bypass. It makes it possible to keep the liquid pet food moving during the dosing process, whilst the filling line is stopped. In this way, feed producers avoid separation in the pump feed. Integration of such dosing systems into existing production lines for animal feed is relatively easy, as additional filling and dosing valves are not required in an estimated 95% of all applications.
Dosing system and also bypass configurations are immediately available as standard products. The so-called suck-back function of ViscoTec technology also ensures a high-performance process, as the cleanliness of the primary packaging materials is guaranteed. They can be fed to labeling, quality assurance, and secondary packaging and logistics immediately after the high-cycle filling process without final cleaning.