Sulzer Molten Salt Pump Supports World First MOSS Renewable Energy Storage Project
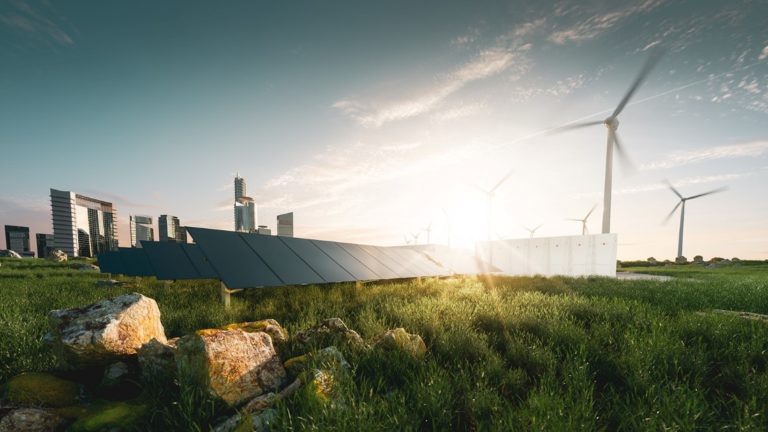
Power generation from renewable sources is transient, with varying sunlight and wind speeds resulting in fluctuating supply. (Image source: Sulzer Ltd.)
A world first, the pilot plant will validate the commercial viability of storing renewable energy in liquid hydroxide salts. Sulzer is a member of the project consortium investing DKK 24.7M in the technology, which has the potential to save 32’000 tonnes of CO2 emissions annually for each 1 GWh of capacity.
Power generation from renewable sources is transient, with varying sunlight and wind speeds resulting in fluctuating supply. Shortfalls in renewable power output to the grid must often be met with thermal powerplants, which is carbon intensive. MOSS aims to solve this by storing renewable energy for up to two weeks in molten hydroxide salts at temperatures of 700°C, which can be used to create steam and drive a turbine. This ensures that during periods of high renewable power generation, excess energy can be stored and deployed when output from windfarms and solar plants falls or electricity demand spikes.
Pumping up renewable power
Arrigo Beretta, Vice President of Global Technology at Sulzer, said: “Sulzer has a rich heritage providing molten salt pumps for concentrated solar power (CSP) plants, so we have proven solutions available to reliably withstand the extremely hot, highly corrosive alkaline salts utilized at MOSS. Working with our consortium partners, we are actively demonstrating how our pump technology can contribute to reducing carbon emissions.”
The pump provided by Sulzer will pump 700°C molten salt from a hot storage tank to a heat exchanger that generates steam. The pilot plant will offer a charge/discharge capacity of 200 kW, but is designed for scalability, with the end goal to build a commercial plant with storage for 1 GWh of power. A facility with this capacity is projected by the consortium to deliver a CO2 saving of 32’000 tonnes annually.
Products that can take the heat
Benoît Martin, Advance Engineering Manager & Pump Application Technical Advisor at Sulzer, added: “Due to the lower flow, only a few meters per hour, at the pilot plant, we specified our VNY vertical mixed-flow molten salt pump. While the hydraulic design is mostly standard, a custom design for the 700°C temperature, upgraded shaft seals and a special material are incorporated.
“At higher temperatures, salt becomes more corrosive, but building a pump to operate at 700°C isn’t a big jump for us. We’ve been providing molten salt pumps since the 1950s, and our work for Generation 3 CSP plants means we can accommodate salts at this temperature. We’re familiar with ensuring proper clearances, good temperature management, right materials and robust performance. Despite the extreme conditions, this is a relatively normal application for us.”
Scaling with the project
Sulzer has worked closely with consortium partner Hyme Energy. Hyme provided its own corrosion protection system and selected the materials required for the pump. Sulzer had previous experience working with these materials, which expedited the project.
As well as resisting aggressive media, the pump offers excellent scalability. If higher flow rates are required, Sulzer’s VEY pump offers the same hydraulics and potential specializations, so any verified specification on the VNY pump can be transferred directly to the larger model when the time comes to expand the project.
Proven technologies for the future energy market
The pilot plant is under construction in Esbjerg, with a ground-breaking ceremony taking place in September 2023. As well as support from organizations in the consortium including Aalborg University, Alfa Laval Aalborg, DIN Forsyning, Energy Cluster Denmark, Hyme Energy, KIRT X THOMSEN, Seaborg and Sulzer - the project is partly funded by the Danish Energy Agency’s Energy Technology Development and Demonstration Program (EUDP). Completion is expected by 2024, with a successful pilot hopefully leading to a fully-fledged commercial operation.
The proliferation of renewable energy in Denmark’s power grid, especially wind, makes it an ideal setting to test the technology. Sulzer is manufacturing the VNY pump with the expectation of delivering the complete unit sometime in September 2023. While the MOSS pilot plant will be a proof of concept for this method of renewable energy storage, it will rely on the proven technologies provided by experts in the field such as Sulzer.
Source: Sulzer Ltd.