New Technology for Legacy Pumps With Reverse Engineering Techniques
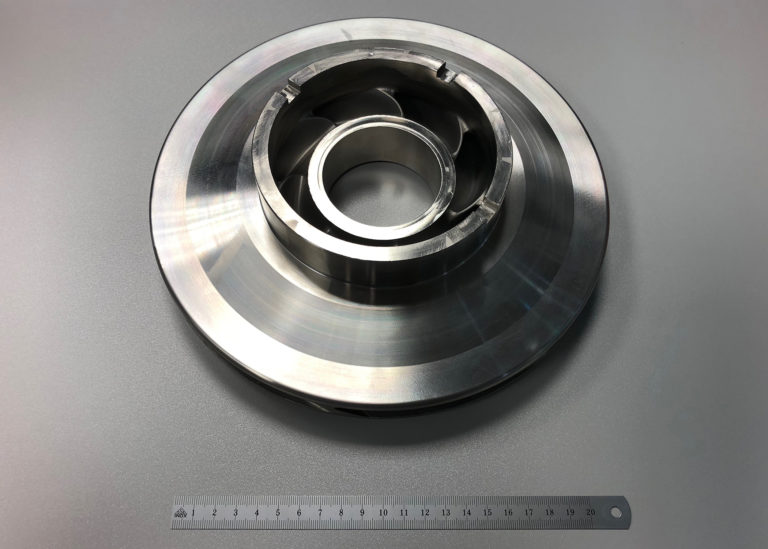
Hybrid manufactured closed impeller (Image source: Sulzer Ltd.)
Keeping these essential assets operational is an important task for any site maintenance team. This challenge is now becoming easier thanks to modern design and re-manufacturing techniques that can reduce lead times and improve performance.
Charles Soothill, Head of Technology for Rotating Equipment Services at Sulzer, looks at some of the latest technologies that are being developed and used to create new parts for pumps including reverse engineering and additive manufacturing (AM).
Pumps play an essential role behind the scenes of our everyday lives, keeping water for municipalities and crop irrigation moving; enabling power generation; supporting oil & gas and manufacturing processes. We will never know how much we depend on these vital assets and how many pumps have influenced our lives.
Something that we also don’t consider is that even the most reliable pumps will eventually succumb to wear, erosion, corrosion or fatigue. When that time comes, it is important to have a plan in place for repairs and replacement parts, to ensure that the pump is re-instated swiftly. The key to an effective solution is to source replacement parts quickly, even if the original equipment manufacturer (OEM) is no longer able to offer support.
Creating precision designs
The quality of these parts is determined by several aspects of the process. Capturing all the necessary data for a 3D CAD drawing can be achieved using laser scanners and digital coordinate measuring machines (CMMs) that can measure items quickly and very accurately.
In the past, creating the physical component would have involved making a mold and casting a blank part that could then be machined to the final dimensions. Today, modern AM techniques offer a much quicker solution and these can be sub-divided into direct, indirect and hybrid processes.
Direct and indirect manufacturing
Direct AM can be achieved in several alloys such as 316L stainless steel and Inconel 625, using laser powder bed melting to make more complex components. This area is expanding as the manufacturing processes for specialist alloys are developed further.
Indirect AM can print replicas of the part required in plastic or wax. These are then encased in a ceramic shell, which is known as investment casting. The shell is heated to melt the wax/plastic and then heated further to fire the ceramic.
This produces a hollow mold that can be filled with metal alloy, allowed to cool and then the ceramic shell is broken-away to leave the final part. The detail and surface finish achieved through this process improves quality and greatly reduces the time normally required for tooling to create new parts.
Another indirect technique is to print the sand mold of a conventional sand process using AM methods. This eliminates the need to store conventional casing patterns as well as the lead time and cost to make new ones.
Hybrid manufacturing
For urgent part requirements on high value assets, such as those seen in the oil and gas or petrochemical industries, a hybrid process using laser metal deposition and five-axis milling now allows rapid manufacture on a single, dedicated machine. For an impeller for example, a forged core is machined using five-axis methods to establish the basic shape of the eye of the impeller before a laser melts the powder and deposits a layer of metal onto the surface below. This allows large volumes or material to be built up quickly onto the core structure underneath. So far, the process has been developed for particular alloys but further advancement is ongoing.
One of the many advantages of this process is that parts can be created from a small stock of forged bars in a few common materials, enabling the manufacturer to make an immediate start. Furthermore, the core of the impeller will have all the positive attributes associated with forged materials. This is then built up further using the laser metal deposition process which can be accomplished on the same machine.
Complex geometries
Having created the basic internal structure, the milling function of the machine is used to finalize the surface finish of the internal passages that would otherwise be inaccessible to machine tools on the finished impeller. Then, the laser metal deposition process continues to add more material to the core, working towards the finished design.
After each application of new metal, the milling process is resumed to deliver the required surface finish, until the entire impeller has been constructed to the 3D CAD design. One benefit of this process is that an impeller with complex hydraulic geometry can be created on one machine, with no need to transfer it between different assets, saving time and improving accuracy.
The flexibility of this manufacturing method also offers the opportunity to create components using different materials, allowing specific alloys to be used in different areas of the design. This is an extension of technologies such as specialist coatings and hard-facings where optimized material properties can be incorporated into the design during the manufacturing process, rather than as an additional process.
Upgrading legacy parts
Some of the design standards used when legacy equipment was manufactured have been updated and refined and these are applied when creating new pump models. As a pump OEM, Sulzer continuously develops and updates its design standards as new technology allows. In this way, the customer of a replacement part can receive a modern component that can perform not just as well as, but better than the original.
For example, experience has shown Sulzer that the thickness of an area of an impeller component can affect erosion or high-cycle fatigue. Sulzer has incorporated this experience into its design and manufacturing standards used to produce replacement parts. This can improve the service life of replacement impellers, including those for much older machines. In this way, customers will benefit from Sulzer’s many years of experience.
A further advantage to applying this process to legacy equipment is in providing the opportunity to re-rate the pump. In many cases, pump applications or duty cycles change over the years and there can be significant benefits in efficiency and productivity achieved through a change in design. Applying computational fluid dynamics (CFD) to create revised hydraulics for the pump is an important step in a re-rate or retrofit project.
Quality counts
Additive manufacturing offers considerable savings in time when it comes to creating new components. The nature of the digital design process and the fact that this information can be sent around the world in seconds, means that the actual manufacturing process can be completed closer to the customer. This reduces logistics costs, minimizes the length of supply chain and of course saves time.
Ultimately, quality is of the utmost importance in pumping applications as it dictates pump efficiency and reliability, both of which have a direct impact on running costs and maintenance resources. AM in this context can be applied to deliver the desired level of quality more quickly, saving time and money, which all goes to help keep our lives moving.
Source: Sulzer Ltd.