Nuova tecnologia per pompe legacy con tecniche di ingegneria inversa
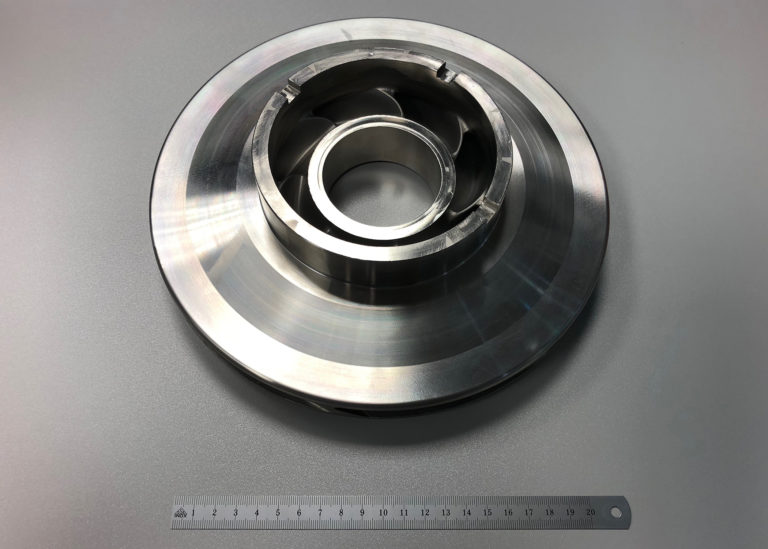
Girante chiusa prodotta ibrida (Fonte immagine: Sulzer Ltd.)
Mantenere operative queste risorse essenziali è un compito importante per qualsiasi team di manutenzione del sito. Questa sfida sta diventando più facile grazie alla moderna progettazione e alle tecniche di rifabbricazione che possono ridurre i tempi di consegna e migliorare le prestazioni.
Charles Soothill, Head of Technology for Rotating Equipment Services di Sulzer, esamina alcune delle ultime tecnologie che vengono sviluppate e utilizzate per creare nuove parti per pompe, tra cui il reverse engineering e la produzione additiva (AM).
Le pompe svolgono un ruolo essenziale dietro le quinte della nostra vita quotidiana, mantenendo in movimento l'acqua per i comuni e l'irrigazione delle colture; consentire la generazione di energia; sostenere il petrolio & amp; gas e processi produttivi. Non sapremo mai quanto dipendiamo da queste risorse vitali e quante pompe hanno influenzato le nostre vite.
Qualcosa che inoltre non consideriamo è che anche le pompe più affidabili finiranno per soccombere a usura, erosione, corrosione o affaticamento. Quando arriva quel momento, è importante avere un piano in atto per le riparazioni e le parti di ricambio, per garantire che la pompa venga reinstallata rapidamente. La chiave per una soluzione efficace è reperire rapidamente parti di ricambio, anche se il produttore di apparecchiature originali (OEM) non è più in grado di offrire supporto.
Creazione di design di precisione
La qualità di queste parti è determinata da diversi aspetti del processo. L'acquisizione di tutti i dati necessari per un disegno CAD 3D può essere ottenuta utilizzando scanner laser e macchine di misura a coordinate digitali (CMM) in grado di misurare gli articoli in modo rapido e molto preciso.
In passato, la creazione del componente fisico avrebbe comportato la realizzazione di uno stampo e la colata di un pezzo grezzo che poteva poi essere lavorato alle dimensioni finali. Oggi, le moderne tecniche di AM offrono una soluzione molto più rapida e queste possono essere suddivise in processi diretti, indiretti e ibridi.
Produzione diretta e indiretta
L'AM diretto può essere ottenuto in diverse leghe come l'acciaio inossidabile 316L e Inconel 625, utilizzando la fusione a letto di polvere laser per realizzare componenti più complessi. Quest'area si sta espandendo con l'ulteriore sviluppo dei processi di produzione per leghe speciali.
Indirect AM può stampare repliche della parte richiesta in plastica o cera. Questi sono poi racchiusi in un guscio di ceramica, noto come microfusione. Il guscio viene riscaldato per fondere la cera / plastica e quindi riscaldato ulteriormente per cuocere la ceramica.
Questo produce uno stampo cavo che può essere riempito con lega metallica, lasciato raffreddare e quindi il guscio ceramico viene spezzato per lasciare la parte finale. I dettagli e la finitura superficiale ottenuti attraverso questo processo migliorano la qualità e riducono notevolmente il tempo normalmente richiesto dagli utensili per creare nuove parti.
Un'altra tecnica indiretta è stampare lo stampo in sabbia di un processo di sabbia convenzionale utilizzando metodi AM. Ciò elimina la necessità di memorizzare modelli di carcassa convenzionali, nonché i tempi e i costi per crearne di nuovi.
Produzione ibrida
Per requisiti urgenti di parti su beni di alto valore, come quelli osservati nell'industria petrolifera e del gas o petrolchimica, un processo ibrido che utilizza la deposizione laser del metallo e la fresatura a cinque assi ora consente una produzione rapida su una singola macchina dedicata. Per una girante, ad esempio, un nucleo forgiato viene lavorato utilizzando metodi a cinque assi per stabilire la forma di base dell'occhio della girante prima che un laser fonda la polvere e depositi uno strato di metallo sulla superficie sottostante. Ciò consente di costruire rapidamente grandi volumi o materiale sulla struttura centrale sottostante. Finora, il processo è stato sviluppato per leghe particolari, ma sono in corso ulteriori progressi.
Uno dei molti vantaggi di questo processo è che le parti possono essere create da un piccolo stock di barre forgiate in pochi materiali comuni, consentendo al produttore di iniziare immediatamente. Inoltre, il nucleo della girante avrà tutti gli attributi positivi associati ai materiali forgiati. Questo viene poi ulteriormente sviluppato utilizzando il processo di deposizione laser del metallo che può essere realizzato sulla stessa macchina.
Geometrie complesse
Creata la struttura interna di base, la funzione di fresatura della macchina viene utilizzata per finalizzare la finitura superficiale dei passaggi interni che altrimenti sarebbero inaccessibili alle macchine utensili sulla girante finita. Quindi, il processo di deposizione del metallo laser continua ad aggiungere altro materiale al nucleo, lavorando verso il progetto finito.
Dopo ogni applicazione di nuovo metallo, il processo di fresatura viene ripreso per fornire la finitura superficiale richiesta, fino a quando l'intera girante è stata costruita secondo il progetto CAD 3D. Un vantaggio di questo processo è che una girante con geometria idraulica complessa può essere creata su una macchina, senza la necessità di trasferirla tra diversi asset, risparmiando tempo e migliorando la precisione.
La flessibilità di questo metodo di produzione offre anche l'opportunità di creare componenti utilizzando materiali diversi, consentendo di utilizzare leghe specifiche in diverse aree del design. Si tratta di un'estensione di tecnologie come rivestimenti speciali e rivestimenti rigidi in cui le proprietà ottimizzate del materiale possono essere incorporate nel design durante il processo di produzione, piuttosto che come processo aggiuntivo.
Aggiornamento delle parti precedenti
Alcuni degli standard di progettazione utilizzati durante la produzione di apparecchiature legacy sono stati aggiornati e perfezionati e vengono applicati durante la creazione di nuovi modelli di pompe. In qualità di OEM di pompe, Sulzer sviluppa e aggiorna continuamente i propri standard di progettazione come consentito dalla nuova tecnologia. In questo modo, il cliente di un pezzo di ricambio può ricevere un componente moderno che può funzionare non altrettanto bene, ma anche meglio dell'originale.
Ad esempio, l'esperienza ha dimostrato a Sulzer che lo spessore di un'area di un componente della girante può influire sull'erosione o sulla fatica da cicli elevati. Sulzer ha incorporato questa esperienza nei suoi standard di progettazione e produzione utilizzati per produrre parti di ricambio. Ciò può migliorare la durata delle giranti sostitutive, comprese quelle per macchine molto più vecchie. In questo modo, i clienti trarranno vantaggio dalla pluriennale esperienza di Sulzer.
Un ulteriore vantaggio dell'applicazione di questo processo ad apparecchiature legacy consiste nel fornire l'opportunità di rivalutare la pompa. In molti casi, le applicazioni della pompa oi cicli di lavoro cambiano nel corso degli anni e possono esserci vantaggi significativi in termini di efficienza e produttività raggiunti attraverso un cambiamento nel design. L'applicazione della fluidodinamica computazionale (CFD) per creare un'idraulica rivista per la pompa è un passo importante in un progetto di riqualificazione o retrofit.
La qualità conta
La produzione additiva offre notevoli risparmi di tempo quando si tratta di creare nuovi componenti. La natura del processo di progettazione digitale e il fatto che queste informazioni possono essere inviate in tutto il mondo in pochi secondi, significa che il processo di produzione effettivo può essere completato più vicino al cliente. Ciò riduce i costi logistici, riduce al minimo la lunghezza della catena di approvvigionamento e, naturalmente, fa risparmiare tempo.
In definitiva, la qualità è della massima importanza nelle applicazioni di pompaggio in quanto determina l'efficienza e l'affidabilità della pompa, che hanno entrambe un impatto diretto sui costi di esercizio e sulle risorse di manutenzione. AM in questo contesto può essere applicato per fornire il livello di qualità desiderato più rapidamente, risparmiando tempo e denaro, il che aiuta a mantenere le nostre vite in movimento.
Fonte: Sulzer Ltd.