Nouvelle technologie pour les pompes héritées avec des techniques d’ingénierie inverse
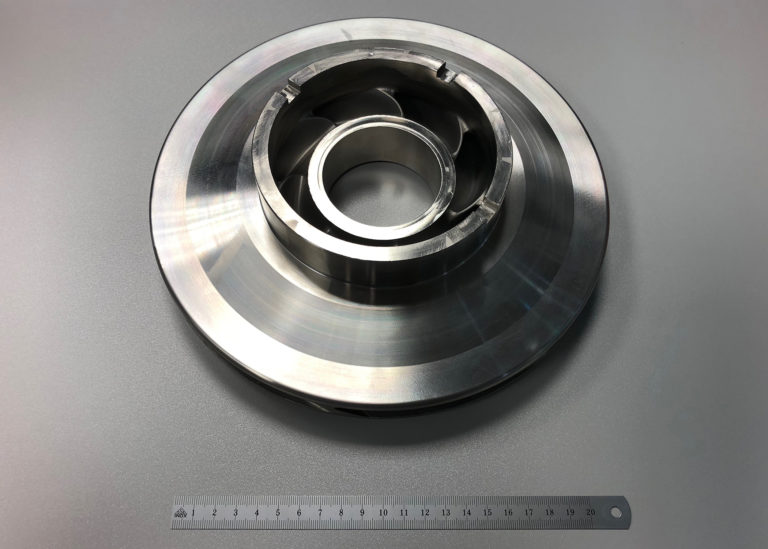
Turbine fermée de fabrication hybride (Source de l'image: Sulzer Ltd.)
Garder ces actifs essentiels opérationnels est une tâche importante pour toute équipe de maintenance de site. Ce défi devient désormais plus facile grâce à des techniques de conception et de re-fabrication modernes qui peuvent réduire les délais et améliorer les performances.
Charles Soothill, responsable de la technologie pour les services d'équipement rotatif chez Sulzer, examine certaines des dernières technologies qui sont développées et utilisées pour créer de nouvelles pièces pour les pompes, y compris l'ingénierie inverse et la fabrication additive (FA).
Les pompes jouent un rôle essentiel dans les coulisses de notre vie quotidienne, en maintenant l'eau des municipalités et l'irrigation des cultures en mouvement; permettre la production d'électricité; huile de soutien & amp; gaz et procédés de fabrication. Nous ne saurons jamais à quel point nous dépendons de ces actifs vitaux et combien de pompes ont influencé nos vies.
Ce que nous ne considérons pas non plus, c'est que même les pompes les plus fiables finiront par succomber à l'usure, à l'érosion, à la corrosion ou à la fatigue. Lorsque ce moment vient, il est important d'avoir un plan en place pour les réparations et les pièces de rechange, afin de s'assurer que la pompe est remise en place rapidement. La clé d'une solution efficace est de trouver rapidement des pièces de rechange, même si le fabricant d'équipement d'origine (OEM) n'est plus en mesure de proposer une assistance.
Création de conceptions de précision
La qualité de ces pièces est déterminée par plusieurs aspects du processus. La capture de toutes les données nécessaires pour un dessin CAO 3D peut être obtenue à l'aide de scanners laser et de machines à mesurer tridimensionnelles numériques (MMT) capables de mesurer des éléments rapidement et très précisément.
Dans le passé, la création du composant physique aurait impliqué de fabriquer un moule et de couler une pièce brute qui pouvait ensuite être usinée aux dimensions finales. Aujourd'hui, les techniques de FA modernes offrent une solution beaucoup plus rapide et celles-ci peuvent être subdivisées en processus directs, indirects et hybrides.
Fabrication directe et indirecte
La FA directe peut être réalisée dans plusieurs alliages tels que l'acier inoxydable 316L et l'Inconel 625, en utilisant la fusion par lit de poudre laser pour fabriquer des composants plus complexes. Ce domaine se développe au fur et à mesure que les procédés de fabrication des alliages spécialisés se développent.
Indirect AM peut imprimer des répliques de la pièce requise en plastique ou en cire. Ceux-ci sont ensuite enfermés dans une coque en céramique, connue sous le nom de moulage de précision. La coque est chauffée pour faire fondre la cire / plastique, puis chauffée davantage pour cuire la céramique.
Cela produit un moule creux qui peut être rempli d'alliage métallique, laissé refroidir, puis la coque en céramique est cassée pour quitter la pièce finale. Les détails et la finition de surface obtenus grâce à ce processus améliorent la qualité et réduisent considérablement le temps normalement nécessaire à l'outillage pour créer de nouvelles pièces.
Une autre technique indirecte consiste à imprimer le moule de sable d'un processus de sable conventionnel en utilisant des méthodes AM. Cela élimine le besoin de stocker des modèles de boîtier conventionnels ainsi que le délai et le coût pour en fabriquer de nouveaux.
Fabrication hybride
Pour les besoins urgents en pièces sur des actifs de grande valeur, tels que ceux observés dans les industries pétrolière et gazière ou pétrochimique, un procédé hybride utilisant le dépôt de métal au laser et le fraisage cinq axes permet désormais une fabrication rapide sur une seule machine dédiée. Pour une roue par exemple, un noyau forgé est usiné en utilisant des méthodes à cinq axes pour établir la forme de base de l'oeil de la roue avant qu'un laser ne fasse fondre la poudre et dépose une couche de métal sur la surface en dessous. Cela permet d'accumuler rapidement de grands volumes ou matériaux sur la structure centrale en dessous. Jusqu'à présent, le processus a été développé pour des alliages particuliers, mais des progrès supplémentaires sont en cours.
L'un des nombreux avantages de ce processus est que les pièces peuvent être créées à partir d'un petit stock de barres forgées dans quelques matériaux courants, ce qui permet au fabricant de démarrer immédiatement. De plus, le noyau de la roue aura tous les attributs positifs associés aux matériaux forgés. Ceci est ensuite développé en utilisant le processus de dépôt de métal au laser qui peut être réalisé sur la même machine.
Géométries complexes
Après avoir créé la structure interne de base, la fonction de fraisage de la machine est utilisée pour finaliser la finition de surface des passages internes qui seraient autrement inaccessibles aux machines-outils sur la roue finie. Ensuite, le processus de dépôt de métal au laser continue d'ajouter plus de matériau au noyau, en travaillant vers la conception finie.
Après chaque application de nouveau métal, le processus de fraisage est repris pour fournir la finition de surface requise, jusqu'à ce que la roue entière ait été construite selon la conception CAO 3D. L'un des avantages de ce processus est qu'une roue à géométrie hydraulique complexe peut être créée sur une seule machine, sans avoir besoin de la transférer entre différents équipements, ce qui permet de gagner du temps et d'améliorer la précision.
La flexibilité de cette méthode de fabrication offre également la possibilité de créer des composants en utilisant différents matériaux, permettant d'utiliser des alliages spécifiques dans différents domaines de la conception. Il s'agit d'une extension de technologies telles que les revêtements spécialisés et les revêtements durs où les propriétés optimisées des matériaux peuvent être incorporées dans la conception pendant le processus de fabrication, plutôt que comme un processus supplémentaire.
Mise à niveau des pièces héritées
Certaines des normes de conception utilisées lors de la fabrication de l'équipement ancien ont été mises à jour et affinées et elles sont appliquées lors de la création de nouveaux modèles de pompes. En tant que fabricant OEM de pompes, Sulzer développe et met à jour en permanence ses normes de conception à mesure que la nouvelle technologie le permet. De cette manière, le client d'une pièce de rechange peut recevoir un composant moderne qui peut fonctionner non seulement aussi bien, mais mieux que l'original.
Par exemple, l'expérience a montré à Sulzer que l'épaisseur d'une zone d'un composant de roue peut affecter l'érosion ou la fatigue à cycle élevé. Sulzer a intégré cette expérience dans ses normes de conception et de fabrication utilisées pour produire des pièces de rechange. Cela peut améliorer la durée de vie des roues de remplacement, y compris celles des machines beaucoup plus anciennes. De cette manière, les clients bénéficieront des nombreuses années d’expérience de Sulzer.
Un autre avantage de l'application de ce procédé à des équipements existants est de fournir la possibilité de réévaluer la pompe. Dans de nombreux cas, les applications de pompe ou les cycles de service changent au fil des ans et il peut y avoir des avantages significatifs en termes d'efficacité et de productivité grâce à un changement de conception. L'application de la dynamique des fluides computationnelle (CFD) pour créer un système hydraulique révisé pour la pompe est une étape importante dans un projet de redimensionnement ou de modernisation.
La qualité compte
La fabrication additive permet un gain de temps considérable lors de la création de nouveaux composants. La nature du processus de conception numérique et le fait que ces informations peuvent être envoyées dans le monde entier en quelques secondes, signifie que le processus de fabrication proprement dit peut être achevé plus près du client. Cela réduit les coûts logistiques, minimise la longueur de la chaîne d'approvisionnement et, bien sûr, fait gagner du temps.
En fin de compte, la qualité est de la plus haute importance dans les applications de pompage car elle dicte l'efficacité et la fiabilité des pompes, qui ont toutes deux un impact direct sur les coûts de fonctionnement et les ressources de maintenance. Dans ce contexte, la FA peut être appliquée pour fournir le niveau de qualité souhaité plus rapidement, en économisant du temps et de l'argent, ce qui contribue à faire bouger nos vies.
Source: Sulzer Ltd.