Nueva tecnología para bombas heredadas con técnicas de ingeniería inversa
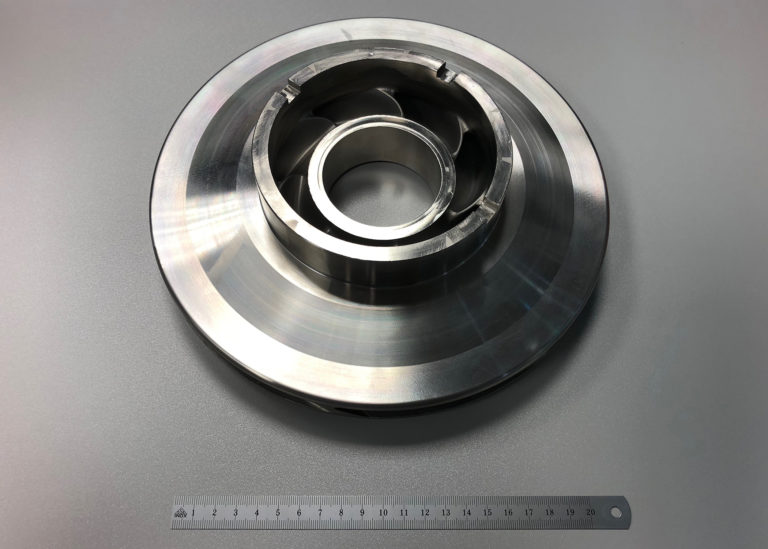
Impulsor cerrado de fabricación híbrida (Fuente de la imagen: Sulzer Ltd.)
Mantener estos activos esenciales operativos es una tarea importante para cualquier equipo de mantenimiento del sitio. Este desafío se está volviendo ahora más fácil gracias al diseño moderno y las técnicas de re-fabricación que pueden reducir los tiempos de entrega y mejorar el rendimiento.
Charles Soothill, jefe de tecnología para servicios de equipos rotativos en Sulzer, analiza algunas de las últimas tecnologías que se están desarrollando y utilizando para crear nuevas piezas para bombas, incluida la ingeniería inversa y la fabricación aditiva (AM).
Las bombas juegan un papel esencial detrás de la escena de nuestra vida diaria, manteniendo el agua para los municipios y el riego de cultivos en movimiento; permitir la generación de energía; aceite de apoyo & amp; procesos de fabricación y gas. Nunca sabremos cuánto dependemos de estos activos vitales y cuántas bombas han influido en nuestras vidas.
Algo que tampoco consideramos es que incluso las bombas más confiables eventualmente sucumbirán al desgaste, erosión, corrosión o fatiga. Cuando llegue ese momento, es importante tener un plan para las reparaciones y las piezas de repuesto, a fin de garantizar que la bomba se reinstale rápidamente. La clave para una solución eficaz es obtener piezas de repuesto rápidamente, incluso si el fabricante de equipos originales (OEM) ya no puede ofrecer asistencia.
Creación de diseños de precisión
La calidad de estas piezas está determinada por varios aspectos del proceso. La captura de todos los datos necesarios para un dibujo CAD en 3D se puede lograr utilizando escáneres láser y máquinas de medición de coordenadas digitales (CMM) que pueden medir elementos de forma rápida y muy precisa.
En el pasado, la creación del componente físico implicaba hacer un molde y fundir una pieza en blanco que luego se podía mecanizar hasta las dimensiones finales. Hoy en día, las técnicas modernas de AM ofrecen una solución mucho más rápida y se pueden subdividir en procesos directos, indirectos e híbridos.
Fabricación directa e indirecta
La AM directa se puede lograr en varias aleaciones, como acero inoxidable 316L e Inconel 625, utilizando la fusión por lecho de polvo con láser para fabricar componentes más complejos. Esta área se está expandiendo a medida que se desarrollan aún más los procesos de fabricación de aleaciones especializadas.
Indirect AM puede imprimir réplicas de la pieza requerida en plástico o cera. A continuación, se envuelven en una carcasa de cerámica, que se conoce como fundición a la cera perdida. La cáscara se calienta para derretir la cera / plástico y luego se calienta más para cocer la cerámica.
Esto produce un molde hueco que se puede llenar con una aleación de metal, se deja enfriar y luego se rompe la cáscara de cerámica para dejar la pieza final. El acabado de detalle y superficie logrado a través de este proceso mejora la calidad y reduce en gran medida el tiempo que normalmente se requiere para las herramientas para crear nuevas piezas.
Otra técnica indirecta es imprimir el molde de arena de un proceso de arena convencional utilizando métodos AM. Esto elimina la necesidad de almacenar patrones de carcasa convencionales, así como el tiempo de espera y el costo de fabricar patrones nuevos.
Fabricación híbrida
Para los requisitos urgentes de piezas en activos de alto valor, como los que se observan en las industrias del petróleo y el gas o petroquímica, un proceso híbrido que utiliza la deposición de metal por láser y el fresado de cinco ejes ahora permite una fabricación rápida en una sola máquina dedicada. En el caso de un impulsor, por ejemplo, se mecaniza un núcleo forjado utilizando métodos de cinco ejes para establecer la forma básica del ojo del impulsor antes de que un láser derrita el polvo y deposite una capa de metal sobre la superficie inferior. Esto permite que se acumulen grandes volúmenes o material rápidamente en la estructura central debajo. Hasta ahora, el proceso se ha desarrollado para aleaciones particulares, pero se están realizando más avances.
Una de las muchas ventajas de este proceso es que se pueden crear piezas a partir de un pequeño stock de barras forjadas en unos pocos materiales comunes, lo que permite al fabricante comenzar de inmediato. Además, el núcleo del impulsor tendrá todos los atributos positivos asociados con los materiales forjados. Esto luego se construye aún más utilizando el proceso de deposición de metal por láser que se puede lograr en la misma máquina.
Geometrías complejas
Una vez creada la estructura interna básica, la función de fresado de la máquina se utiliza para finalizar el acabado de la superficie de los pasajes internos que de otra manera serían inaccesibles para las máquinas herramienta en el impulsor terminado. Luego, el proceso de deposición de metal por láser continúa agregando más material al núcleo, trabajando hacia el diseño terminado.
Después de cada aplicación de metal nuevo, se reanuda el proceso de fresado para obtener el acabado de superficie requerido, hasta que todo el impulsor se ha construido con el diseño CAD 3D. Una ventaja de este proceso es que se puede crear un impulsor con geometría hidráulica compleja en una máquina, sin necesidad de transferirlo entre diferentes activos, lo que ahorra tiempo y mejora la precisión.
La flexibilidad de este método de fabricación también ofrece la oportunidad de crear componentes utilizando diferentes materiales, lo que permite que se utilicen aleaciones específicas en diferentes áreas del diseño. Se trata de una extensión de tecnologías como recubrimientos especiales y revestimientos duros donde las propiedades optimizadas del material se pueden incorporar al diseño durante el proceso de fabricación, en lugar de como un proceso adicional.
Actualización de piezas heredadas
Algunos de los estándares de diseño utilizados cuando se fabricaron equipos heredados se han actualizado y perfeccionado y se aplican al crear nuevos modelos de bombas. Como OEM de bombas, Sulzer desarrolla y actualiza continuamente sus estándares de diseño a medida que lo permite la nueva tecnología. De esta manera, el cliente de una pieza de repuesto puede recibir un componente moderno que puede funcionar no tan bien como el original, sino también mejor.
Por ejemplo, la experiencia ha demostrado a Sulzer que el grosor de un área de un componente del impulsor puede afectar la erosión o la fatiga de ciclo alto. Sulzer ha incorporado esta experiencia en sus estándares de diseño y fabricación utilizados para producir piezas de repuesto. Esto puede mejorar la vida útil de los impulsores de repuesto, incluidos los de máquinas mucho más antiguas. De esta forma, los clientes se beneficiarán de los muchos años de experiencia de Sulzer.
Una ventaja adicional de aplicar este proceso a los equipos heredados es que brinda la oportunidad de recalificar la bomba. En muchos casos, las aplicaciones de la bomba o los ciclos de trabajo cambian a lo largo de los años y puede haber beneficios significativos en la eficiencia y la productividad logradas mediante un cambio en el diseño. La aplicación de dinámica de fluidos computacional (CFD) para crear un sistema hidráulico revisado para la bomba es un paso importante en un proyecto de recalificación o modernización.
La calidad cuenta
La fabricación aditiva ofrece un ahorro de tiempo considerable a la hora de crear nuevos componentes. La naturaleza del proceso de diseño digital y el hecho de que esta información se pueda enviar a todo el mundo en segundos significa que el proceso de fabricación real se puede completar más cerca del cliente. Esto reduce los costos de logística, minimiza la longitud de la cadena de suministro y, por supuesto, ahorra tiempo.
En última instancia, la calidad es de suma importancia en las aplicaciones de bombeo, ya que dicta la eficiencia y confiabilidad de la bomba, las cuales tienen un impacto directo en los costos de funcionamiento y los recursos de mantenimiento. La AM en este contexto se puede aplicar para ofrecer el nivel de calidad deseado más rápidamente, ahorrando tiempo y dinero, todo lo cual ayuda a mantener nuestras vidas en movimiento.
Fuente: Sulzer Ltd.