Alternative Application for APV’s Positive Displacement Pumps
For many years APV has been renowned as a supplier of pumps for the food industry, but the company also has expertise in other industries. For example, APV’s range of positive displacement pumps is used for the production of cosmetics and dyestuffs.
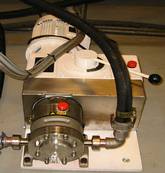
(Quelle: APV)
Bad Experience with Gear Pumps
Previously, Dyrup used gear pumps in their production process. However, as many of these pumps only had a life-cycle of approximately three months, Dyrup initially changed these for APV Cleanline positive pumps and subsequently switched to the latest technology APV pump range known as the DW pump. The APV pumps have a far longer life-cycle than the original gear pumps used by Dyrup, because they are capable of handling the remains of granulate which are contained within the paste.
Good Exerience with Cleanline/DW Pumps
The first Cleanline pumps were installed at Dyrup more than six years ago. Today, there are four Cleanline pumps and one DW1 pump in operation at the factory in Kolding. The DW1 pump was installed at the beginning of 2002.
Dyrup requires a combination of reliability and high efficiency from the pumps. The DW pump yields approximately 6 litres per minute at a comparatively low velocity (400 r/min) and is fitted with Silicon Carbide(SiC/SiC) single mechanical shaft seals. Overall, it is designed for optimum operational efficiency and minimum wear of parts.
With more than 20 years’ experience as Service Manager for Dyrup, Bent Sørensen is very satisfied with APV’s positive displacement pumps. "There have been no serious problems during nearly seven years of operation," he said "and we are especially satisfied with the newly designed DW pump, which we expect to last for more than 10 years. We do not anticipate investing in alternative solutions for some time to come, other than to replace our Cleanline pumps with the new DW pump."
DW Redesign
The newly designed DW pump incorporates significant improvements to the parts that do not come into contact with the product. Flexibility is in-built, with the option to quickly change the inlet/outlet orientation on the premises. Ease of maintenance and cleanability as well as improved efficiency are some of the other advantages.
Source: SPX FLOW, Inc.