Diaphragm Metering Pump Makes “Electrolysis Made in Baden-Württemberg” Fit for Industrial Application
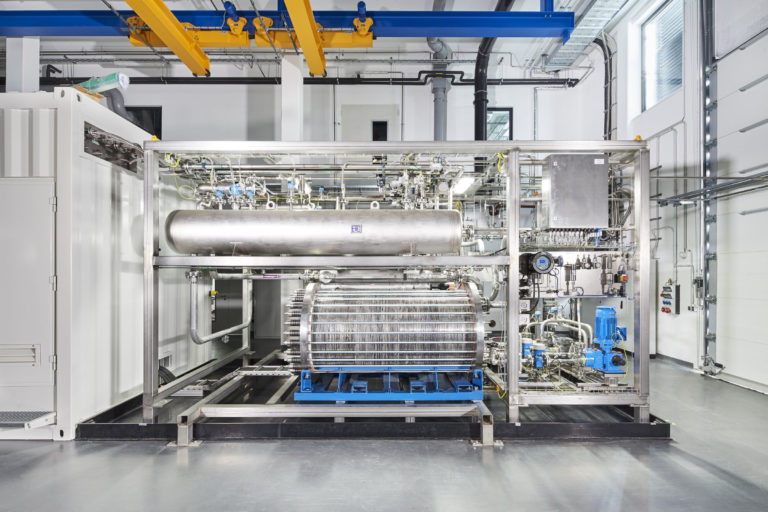
The requirements for an electrolyzer and the individual components are complex. (Image source: Center for Solar Energy and Hydrogen Research Baden-Württemberg (ZSW))
Hydrogen is also suitable as a storage medium to compensate for fluctuations in renewable energy production, since it can be produced via electrolysis using any power source. As part of the "Electrolysis Made in Baden-Württemberg" project, which was completed in 2023, the Baden-Württemberg Center for Solar Energy and Hydrogen Research (ZSW) has now strengthened the region as a hydrogen location for the long term. With the participation of 40 companies, a scalable system demonstrator for alkaline pressure electrolysis with an output of 1 MWel was engineered. The pump specialist LEWA from Leonberg, Germany, also contributed to the success of the project: an ecoflow diaphragm metering pump with Ex motor feeds the water required for hydrogen production into the process. As of 2026, the system will continue to operate in the H2 GeNeSiS model region and feed hydrogen into the new pipeline along the Neckar River.
On the way to the targeted climate neutrality, the German government did decide on the update of the National Hydrogen Strategy until July 2023. The assumption is that the demand for hydrogen in Germany will more than double by 2030 compared to today. Given this forecast, the update defines four fields of action: expand the availability, infrastructure and use of hydrogen and create good framework conditions for planning and approval processes. The "Electrolysis Made in Baden-Württemberg" of the ZSW project, which was successfully completed at around the same time last summer, is also aimed at the first two points in particular.
The aim of the project, which was funded by the Baden-Württemberg Ministry of Economic Affairs, was to develop a CE-certified, production-ready alkaline water electrolysis system with an output of 1 MWel, which can be scaled for various industrial applications thanks to its modular design. "Electrolysis systems in this performance class are particularly suitable as so-called H2 hubs for decentralized hydrogen production," explained Frank Baumgart, Laboratory Manager in the Regenerative Energy Sources and Processes (REG) department at ZSW and the main person responsible for the design and construction of the electrolysis demonstrator. "These are used by filling stations or industrial processes that require hydrogen, for example."
LEWA ecoflow diaphragm metering pump at the heart of the electrolysis system demonstrator
A total of 40 companies were involved in the realization of the "Made in Baden-Württemberg" system demonstrator. They contributed the individual process and electrical engineering components to the pilot project, as well as valuable know-how. The project partners had the opportunity to gain experience in this special application area and to test their components in the actual application environment. "The requirements for an electrolyzer are complex," noted Baumgart. "On the one hand, high pressures and temperatures of up to 90 °C are required to achieve the best possible overall efficiency. Secondly, the material resistance of all system parts must be ensured, since individual components come into contact with demineralized water, alkaline electrolyte or hydrogen or oxygen."
With the pump that feeds the water required for hydrogen production into the process, the process engineering specialists from LEWA contributed a central component at the heart of the system. The ecoflow diaphragm metering pump feeds in exactly the amount of process water that is consumed during electrolysis. This requires the flow rate to be precisely adjusted to the actual consumption conditions in real time. Otherwise, the metering process would have a negative effect on the system's closed control loops. "Metering is therefore carried out using two-point control," explained Björn Pfizenmayer, Area Sales Manager at LEWA. "The unrivaled suction capacity of LEWA pumps ensures a continuous process."
Difficult suction conditions and many years of continuous operation
For this complex task, LEWA chose the ecoflow LDC1 M910S, which has a hydraulic output of 0.2 kW and was equipped with an Ex motor due to the hydrogen produced during the process. In accordance with the requirements of the application, it conveys water at up to 30 °C at a flow rate of 130 l/h against 40 bar in the electrolysis system demonstrator. "This type of pump enables the precise adjustment of a defined water volume within a wide control range," said Baumgart. "This is particularly important for the system demonstrator, because electrolysis stacks with different lengths and outputs are to be tested and operated here."
As these types of systems are designed to operate for up to 20 years, all system components must have a long service life and be easy to maintain and repair. Due to possible points of contact with the potassium hydroxide solution in the electrolysis stack, all components of the ecoflow unit also had to be highly resistant to chemicals. This is why the components in contact with the product are made of stainless steel 316/316L (1.4401/1.4404), which is also resistant to potassium hydroxide solutions, and the pump head of the M900 series has a robust PTFE sandwich diaphragm. "The diaphragm is permanently monitored with patented LEWA DPS technology," added Pfizenmayer. "This prevents interruptions caused by leaks, even when the electrolyzer is in continuous use."
Successful project completion in 2023
The electrolysis system demonstrator "Made in Baden-Württemberg" with a CE marking has been in operation at ZSW since 2023. The 1 MWel system is also a basic model and, thanks to its modular design, larger output classes up to the double-digit megawatt range can be scaled from it in the future. The demonstrator itself will eventually feed hydrogen into the new pipeline along the Neckar River as of 2026, as part of the H2 GeNeSiS model region at the port of Stuttgart. "From the individual components to the electrolysis stack and the system technology, the demonstrator serves as a showcase for the technology and regional value creation potential of Germany as a hydrogen location," said Baumgart in summary.
Source: LEWA GmbH