Air Supply Through Injectors Slows the Rate at Which Odour and Decay Develop in Waste Water
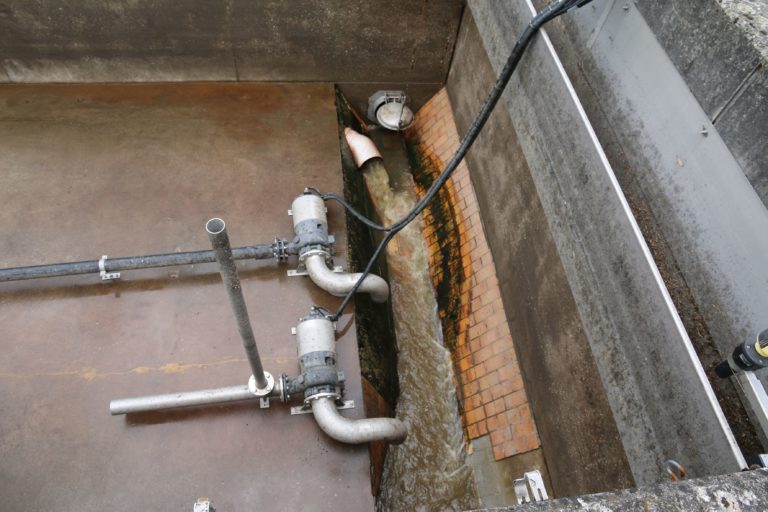
The two MXS series submersible waste water pumps with single-channel impeller should be positioned as close as possible to the drain channel to ensure continuous pumping out. (Image source: HOMA Pumpenfabrik GmbH)
Up to that point, operators had not only had to cope with inadequate energy efficiency. Solids such as sand, twigs or fibres swept along with the water also blocked the nozzles and pumps of the water jets used. At the same time, due to insufficiently optimised adjustment to the tank geometry, the installed equipment was unable to adequately mix the water, resulting in malodorous deposits on the floor and walls. HOMA Pumpenfabrik GmbH, a specialist company with many years of experience in the area of waste water management systems, was therefore assigned to supply and install new cleaning equipment. Thanks to accurately matched injector jets and submersible pumps with single-channel impeller, solids are no longer deposited in the collection tank and maintenance costs have been significantly reduced. These positive results led to further cleaning systems from HOMA being installed in the stormwater overflow tank in 2019.
“Emergency interventions were common practice here for a long time,” reported Sascha Velte, Senior Waste Water Technician at the Nastätten rainwater collection facility. “In addition to the usual domestic waste water, in the case of extreme precipitation, rainwater from surrounding streets and public spaces is diverted to us to avoid overloading the sewerage system and sewage treatment plant. We therefore often had to carry out emergency interventions and repairs because this mixed water had swept up rubbish, branches or sanitary products, which in turn blocked the pumps and water jets.” In 2018, the Nastätten municipal works, which operated the system, decided that the ageing, fault-prone water jets and pumps should be modernised. To minimise future malfunctions due to solids, whilst also counteracting any deposits, the municipal services called in the experts from HOMA Pumpenfabrik GmbH. Since our company, based in Neunkirchen-Seelscheid in Germany, has extensive experience with sewage treatment plants and water management systems, we were able to offer a bespoke solution.
“The main problem with the water jets that were installed up to 2018 was that they were not sufficiently tailored to the elongated design of the collection tank,” explained Mr Velte. “With a rectangular tank, it is particularly difficult to reach every nook and cranny to ensure that the solids circulating in the water remain suspended and do not settle on the tank floor or block the pumps.” Organic particles in the water can lead to the formation of sludgy deposits, quickly resulting in a putrid odour when the tank is emptied, which becomes noticeable in the local area. The partially mineral deposits therefore had to be regularly removed through manual cleaning, which took a considerable amount of time. This mass disposal of solids also meant a high load for the downstream sewage treatment plant and overburdened the pumps and bar screens there.
Precise matching to the tank geometry prevents deposits
At HOMA, as we already had experience in similar projects with tanks more than three times as long as they are wide, our pump experts had no problem offering a suitable concept. “The plan was to position two BR 100 injector jet pipe systems so that, in the very long but narrow tank, the flow jets guarantee a high mixing rate but backflow is not impaired,” explained Alfred Kleu, Head of Application Management at HOMA Pumpenfabrik GmbH. “In addition, the two MXS series submersible waste water pumps with single-channel impeller were fitted with suction pipes on the pump suction flange so that the pumps can draw the medium out of the drain channel for as long as possible to ensure continuous pumping out.”
HOMA engineers positioned one of the two injectors with an accurately gauged pipe extension piece roughly in the centre of the tank and the other at the end, thereby ensuring that the jets could churn and aerate the entire contents of the tank, in accordance with its design. The medium is pushed and accelerated through an injector nozzle flange mounted to the pump discharge, which creates a suction effect (vacuum) via a vertical pipe and draws air in. The air/water mixture is pushed out through the jet pipe at high speed parallel to the tank floor. This prevents the formation of any deposits that would generate an unpleasant odour or necessitate time-consuming cleaning. The PermaCool function (cooling jacket) of the MXS pumps used also ensures reliable continuous operation (S1) without thermal overload in the case of a surface motor
Clog-resistant impellers for uninterrupted operation
“Aside from the special tank geometry, we also tackled the problem of possible clogging of the impellers in the pumps,” reported Florian Steiner from Waste Water Systems Consulting and Sales/Distribution at HOMA. “As the mixed water can contain not only added content such as leaves, sticks, sand, etc. but also fibrous solids such as flushed sanitary products, the pumps used needed to be as resistant as possible to clogging caused by the strands that frequently form.” The benefit of the MXS pumps installed in Nastätten is that their closed single-channel impellers have large ball passages, through which the solids can pass easily. This also means that pump failure does not occur due to the collection of fibrous content (clogging) and there is no longer any need for urgent maintenance in the holding tanks.
“In addition to reduced maintenance, we have also observed lower running costs since the new injectors were installed,” explained Mr Velte. “As the pumps have an efficiency of 80 % and performance is not reduced by pump failures, power consumption has gone down significantly.” Consequently, the required optimisation of the cleaning systems was achieved, in terms of energy efficiency and ecological footprint. In conjunction with virtually maintenance-free operation, this has also led to considerable cost savings.
“When working together with HOMA, what impressed us most was their focus on finding solutions,” concluded Mr Velte. “Whereas our old equipment was not particularly suited to the tank and the water consistency, HOMA delivered a specific design with durable pumps that are protected against all kinds of solids. This is why we opted to fit the adjacent stormwater overflow tank with the same injector jet system in 2019 too.”
Source: HOMA Pumpenfabrik GmbH