Optimierung der Leistung und Zuverlässigkeit von Offshore-Pumpen
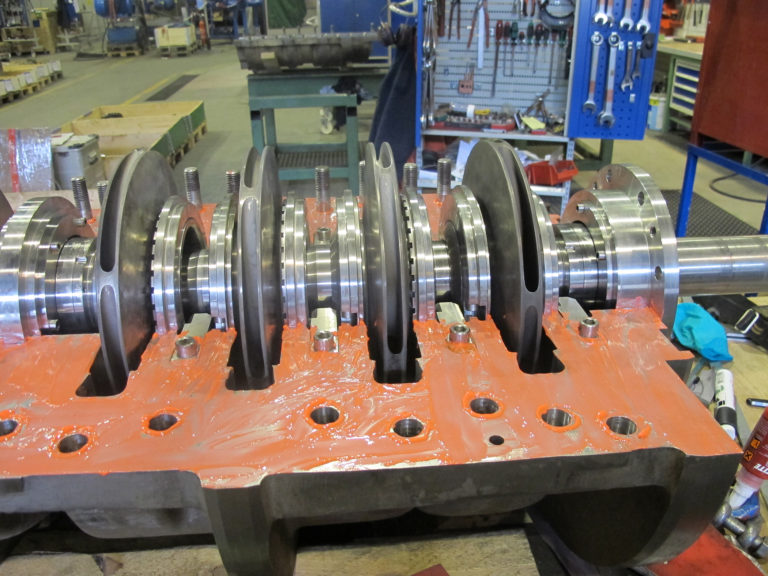
Nachbearbeitete interne Komponenten optimieren die Pumpenleistung (Bildquelle: Sulzer Ltd.)
Luca Lonoce, Pump Retrofit Specialist bei Sulzer, untersucht die Vorteile eines Pump Retrofit-Projekts anhand eines Beispiels, mit dem der Betreiber 150 Mio. USD eingespart hat.
Änderungen der Pumpenleistung können aus mehreren Gründen erforderlich sein. Beispielsweise werden Raffinerien, die die Produktion steigern möchten, die betroffenen Vermögenswerte untersuchen und Engpässe identifizieren. In einigen Fällen müssen die Durchflussraten über die vorhandenen Funktionen der Geräte hinaus erhöht werden. Ein Bohrloch muss möglicherweise die Wasserinjektionsrate erhöhen, oder die Zuverlässigkeit bestimmter Anlagen muss möglicherweise verbessert werden, um die neuen Ziele zu erreichen.
Neu für Alt
Die erste und einfachste Lösung besteht darin, die vorhandenen Pumpen durch neue Geräte zu ersetzen, die für die neuen Produktionsraten spezifiziert wurden. Dies hat viele Vorteile in Bezug auf Zuverlässigkeit, Leistung und Effizienz. Die Verwendung der neuesten Materialien und Designtechnologien gewährleistet eine dauerhafte und effektive Lösung.
Es gibt jedoch einige Nachteile - die Zeit bis zur Fertigstellung des Projekts, den Produktionsausfall während der Arbeit und die Gesamtinvestitionen. Zusammen schließen diese diese Option fast immer aus.
Anpassen und überleben
Eine günstigere Option besteht darin, die vorhandenen Assets so zu ändern, dass sie die neuen Ziele erreichen können. Es gibt viele Herausforderungen, die bis zu einem gewissen Grad durch die Implementierung eines Nachrüstungsprojekts gelöst werden können. Zuverlässigkeitsprobleme können durch einen Materialwechsel verbessert werden, um Erosion oder Korrosion zu beheben. Die Leistung kann durch Ändern des hydraulischen Designs der Pumpe verbessert werden.
Nachrüstungsprojekte sind eine sehr kostengünstige Alternative zum Austausch großer Anlagen, wenn ein Produktionsstandort eine Leistungsänderung oder eine Verbesserung der Zuverlässigkeit erfordert. Durch die Minimierung der Anzahl der zu ändernden Komponenten werden sowohl die Zeit als auch die Kosten des Projekts auf ein Minimum reduziert.
In Norwegen bietet die Regierung beispielsweise der Öl- und Gasindustrie Unterstützung bei der Reduzierung ihres CO2-Fußabdrucks an. Einer der größten Gewinne kann durch die Reduzierung des Energieverbrauchs von Pumpanlagen erzielt werden. Durch ein Nachrüstungsprojekt zur Optimierung der Pumpenleistung für jede Anwendung konnten die Betreiber erhebliche Einsparungen bei den Betriebskosten erzielen, die zur Erreichung der nationalen Kohlenstoffziele beitragen.
Optimierte Leistung
Einer der Hauptbereiche des Pumpenbetriebs sind Wassereinspritzsysteme, mit denen die Produktivität der Ölquellen maximiert wird. Wenn das Ölfeld reift, müssen die Wassereinspritzraten erhöht werden, um die Ölproduktion zu maximieren. Dies erfordert eine Erhöhung der Kapazität der Einspritzpumpen, ohne die Anordnung der Anlage oder die vorhandenen Rohrleitungen zu beeinträchtigen.
In diesem Fall muss die Durchflussmenge erhöht werden, während die Förderhöhe beibehalten wird. Dies bedeutet, dass der Leistungsbedarf steigt und das Pumpendesign geändert werden muss. Durch die enge Zusammenarbeit mit den Plattformingenieuren und die Festlegung der Grenzen des Motors oder der Turbine können Pumpenkonstrukteure einen modifizierten Hydraulikvorschlag erstellen, der sowohl die Leistung als auch den Wirkungsgrad verbessert.
In einem alternativen Szenario muss der Systemdruck möglicherweise reduziert werden, während die ursprüngliche Durchflussrate beibehalten wird. Das Reduzieren des von einer Pumpe erzeugten Drucks kann erreicht werden, indem mehrere Stufen vom Pumpenrotor entfernt werden, wodurch der Energiebedarf der Pumpe erheblich verringert wird. In einigen Fällen kann die Wiederholungslösung einen Frequenzumrichter enthalten, der mehr Flexibilität bei der Leistung der Pumpe bieten kann.
Durch erneutes Einstellen der hydraulischen Bedingungen einer Pumpe auf den neuen Betriebspunkt, eine Kombination aus Durchfluss und Förderhöhe, kann das System effizienter arbeiten. Basierend auf den nachgeschalteten Anforderungen können die Pumpenkennlinien so umgestaltet werden, dass sie den erforderlichen Durchfluss und Druck liefern, während sie an oder nahe ihrem besten Wirkungsgradpunkt (BEP) arbeiten.
Ein typisches Beispiel
Eines der größten Offshore-Ölfelder im Nahen Osten verwendet fünf BB5-Einspritzpumpen, vier 9-MW-Wehrpumpen und eine 14-MW-Sulzer-HPcp-Pumpe, die alle von Gasturbinen angetrieben werden. Der Vorschlag bestand darin, die Produktion auf dem Ölfeld zu steigern, wodurch die Gasturbinen aufgerüstet werden müssten, um ihre maximal erreichbare Leistung zu erzielen. Nachdem dies erreicht wurde, würden alle fünf Pumpen erneut betrieben, um die maximal möglichen Einspritzdurchflussraten unter Verwendung der erhöhten Leistungskapazität zu liefern.
Sulzer wurde sowohl als Originalhersteller für Pumpen (OEM) als auch als unabhängiger Wartungsanbieter mit dem Auftrag zur Aufrüstung aller fünf Pumpen beauftragt. Ziel war es, mit möglichst vielen vorhandenen Komponenten und bei minimaler Unterbrechung des Produktionsplans die bestmöglichen Durchflussraten zu erzielen.
Sulzer hatte Zugriff auf eine komplette Ersatzpatrone für die Weir-Pumpen, aus der alle erforderlichen Konstruktionsinformationen gesammelt und als Grundlage für die Änderung des Patronendesigns verwendet werden konnten. Der Vorschlag bestand darin, das ursprüngliche 4-Stufen-Design gegen eine 3-Stufen-Alternative mit einem Laufrad mit ähnlichem Durchmesser auszutauschen. Dadurch konnten die vorhandenen Rohrleitungen, Schmiersysteme, Gleitringdichtungen, Lagergehäuse und Standortschnittstellen beibehalten werden.
Steigerung der Produktivität
Mit der Ersatzpatrone implementierte Sulzer das neue Laufdesign und lieferte es an die Plattform zurück, auf der es eine der Betriebspumpen ersetzte. Der gesamte Vorgang zum Entfernen und Installieren des neuen Laufs dauerte nur 2-3 Tage, einschließlich der Inbetriebnahme. Die entfernte Originalpatrone wurde in das Entwicklungszentrum von Sulzer zurückgebracht, wo sie denselben Konstruktionswiederholungsprozess durchlief.
Durch die Befolgung dieses Implementierungsplans wurde sichergestellt, dass der Betrieb auf der Plattform vom Wiederholungsprojekt nicht betroffen war, wodurch Produktionsausfälle vermieden und der Arbeitsaufwand auf der Plattform minimiert wurden. Die verbesserten Patronen führten zu einer 25% igen Steigerung des Durchflusses gegenüber dem ursprünglichen Design der vier Pumpen, wobei die gesamte Einspritzkapazität um 30% stieg.
Dieses Projekt war auch äußerst kostengünstig. Im Vergleich zu einem Projekt zur Beschaffung neuer Pumpanlagen für dieselbe Aufgabe sparte das Wiederholungsprogramm dem Plattformbetreiber insgesamt 150 Mio. USD und vermeidete alle Störungen, die durch eine neue Installation entstehen würden.
Laufende Unterstützung
Öl- und Gasförderanlagen werden von Leistung und Anlagenzuverlässigkeit angetrieben, die durch technisches Know-how und Konstruktionserfahrung verbessert werden können. Durch die Zusammenarbeit mit einem Engineering-Partner wie Sulzer, der über ein weltweites Netzwerk von Service-Centern sowie jahrzehntelange Erfahrung in der Pumpenkonstruktion verfügt, insbesondere im Offshore- sowie im Öl- und Gassektor, können Plattformbetreiber ihr Geschäft optimieren.
Wiederholte Projekte bieten die Möglichkeit, die Verfügbarkeit, Zuverlässigkeit und damit die Produktivität zu steigern. In einigen Anwendungen ist es möglich, die Effizienz zu verbessern, wodurch die Energiekosten sowie der CO2-Fußabdruck des Unternehmens gesenkt werden. Was auch immer das Ziel ist, wenn es um die Pumpenleistung geht, sollte das Nachrüstungsprojekt immer als eine der Hauptoptionen betrachtet werden.
Quelle: Sulzer Ltd.