Sulzer’s Technology Converting Bamboo into Bioethanol in Indian Bio-Refinery
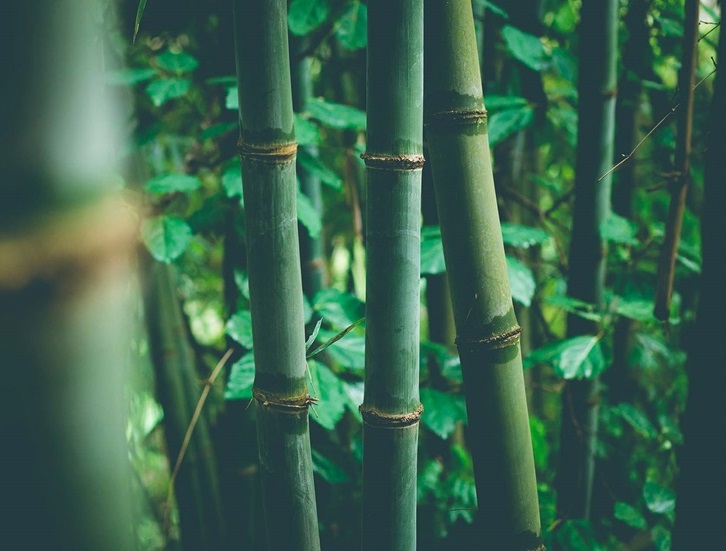
Sulzer’s technology converting bamboo into bioethanol in pioneering Indian bio-refinery. (Image source: Sulzer Ltd.)
The country’s first bio-refinery, Assam Bio Refinery Pvt Ltd., built by Chempolis technology, is a ground-breaking joint venture that will be the only refinery in the world to create bioethanol from bamboo – available in abundance in north-eastern India. To help realize this pioneering endeavor, Sulzer is delivering a range of engineered application pumps as well as core technology such as column internals for the refining process.
India, like most countries, is keen to improve the sustainability of its industrial sectors and is taking positive steps by using renewable feedstocks such as bamboo to create biofuels and other chemicals. To ensure a successful and reliable process, a joint venture has been formed between the state-run oil refining company, Numaligarh Refinery Ltd. and two Finnish companies, Fortum and Chempolis.
The facility will use Sulzer’s unrivalled experience in pump design and manufacturing as well as separation technology to ensure long-term reliability and efficiency in the refining processes. The company’s expertise in the chemical industry is well-established and it has been supplying process pumps to similar applications all over the world for decades.
Once complete, the bio-refinery will use 300’000 tons of bamboo each year. In addition to the environmental benefits of the fuels and chemicals being produced, the refinery will procure bamboo and other raw materials from local suppliers, strengthening the community’s local economy.
Using Chempolis proprietary technology, the joint venture is demonstrating how India can utilize its own natural, sustainable resources to reduce the reliance on fossil fuels and work towards self-sufficiency in energy production. The bio-refinery is dimensioned to produce 60 million liters of bioethanol, which can be used to help power vehicles, as well as 19’000 tons of furfural and 11’000 tons of acetic acid per year.
Frédéric Lalanne, President of Sulzer’s Flow Equipment Division and CEO of the Sulzer Group from February 18, 2022, commented: “The increased use of renewable energy sources is all the more important as global demand for power continues to rise. Sulzer is committed to using its engineering expertise and process knowledge to support customers that are using innovative processes to reduce our reliance on fossil fuels and improve sustainability.”
Source: Sulzer Ltd.