Seepex Unveils Automatically Adjustable Progressive Cavity Pump
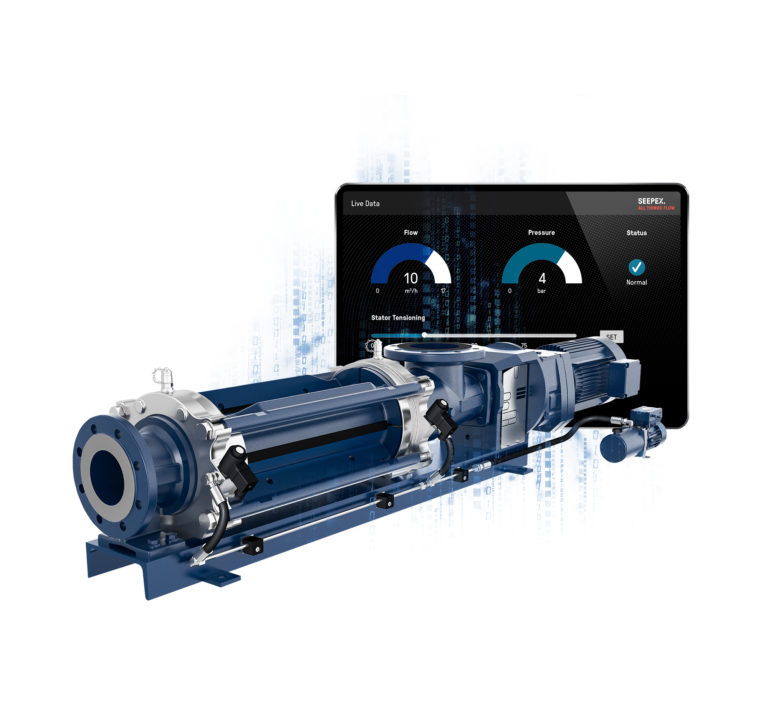
It's all a matter of adjustment: the stator clamping is adjusted digitally to the optimum operating point with a click. (Image source: Seepex GmbH)
With SCT AutoAdjust the progressive cavity pump is automatically adjusted to the optimal operating point – simply with one click from the control room or locally on site through the Seepex Pump Monitor via the app. The clamping between the most important conveying elements – the rotor and stator – can be easily adapted to the conditions in the process or the degree of wear. With "SCT AutoAdjust", Seepex has further developed and digitized its internationally patented Smart Conveying Technology (SCT).
Top-quality pumping capabilities through the use of Industry 4.0 properties
"SCT AutoAdjust is the bridge between the world of analog pumps and digital solutions and has a unique technical design," says Dr. Christian Hansen, Chief Technology Officer (CTO) at Seepex. The pump manufacturer from Bottrop is presenting an automated pump with integrated Industry 4.0 technology. Wrenches and the like are a thing of the past – one remote click or a touch on the on-site Pump Monitor is enough to adjust the stator clamping system in such a way that the pump always provides top-quality pumping performance. Seepex has been setting standards in the area of easy maintenance since 2008 with its predecessor, the mechanically adjustable SCT, and as a leading manufacturer now offers the widely recognized possibility of readjusting the stator clamping. This technology is now being improved once more with the introduction of SCT AutoAdjust. Manual adjustment, for example in the event of wear or short-term process changes, is completely unnecessary here because the service technician responsible can easily carry out all the changes from the control room. In this new pump generation the signals are transmitted via analog signal cables or digitally via various bus systems. Travel to and from the locations where work needs to be carried out is eliminated, thereby saving both time and labor costs. Even in complex plants, where pumps are often difficult to access, the service technician benefits from the remote adjustment option.
Easy integration into existing systems
The control system, sensors and readjustment device are already included in the package. The Seepex Pump Monitor can be integrated on request. The Pump Monitor measures all relevant operational parameters such as temperature, flow rate, pressure, vibration, etc. – 365 days a year, 24 hours a day. This means that the data can be analyzed only locally or, even more extensively, also in the cloud, in the Seepex Connected Services. This makes it possible to measure and optimize pump performance. The degree of wear becomes apparent and any upcoming maintenance can be planned in advance. This reduces downtimes and avoids unplanned outages. Integration into existing process infrastructures could not be easier. Start-up, connection to the Pump Monitor and connection to the cloud are carried out by a Seepex specialist.
The shortest, fastest and easiest maintenance work ever
As long ago as 2008 Seepex launched its Smart Conveying Technology (SCT) on the market and revolutionized the maintenance of progressive cavity pumps. The tried and tested design principle: the Smart Stator consists of two halves and can be easily installed and uninstalled on site without having to remove suction or pressure pipes. Maintenance can therefore be carried out very easily by just one individual. With an integrated retensioning device, the clamping between the rotor and the stator can be adjusted for optimum conveyance if the flow rate changes, e.g. due to wear and tear. This significantly extends the service life of the rotor and stator, reduces the need for spare parts and lowers the life-cycle costs of Seepex pumps.
With the SCT AutoAdjust this retensioning of the stator is now performed automatically at the push of a button via a hydraulic unit, completely without the use of special tools. The newly developed premium model range makes work on the pump considerably easier and therefore helps to save even more time and costs. Assembly and dismantling is still just as easy as with the familiar SCT system. In addition to the usual adjustment of the pump speed, retensioning is a further, much more efficient way of keeping the pump flow rate constant within the optimum range. Seepex enables maximum energy savings and "the shortest, fastest and easiest maintenance work ever. Moreover, life-cycle costs are significantly reduced," says Dr. Tobias Mänz, Project Manager at Seepex. SCT AutoAdjust will be available for pressures of up to 8 bar. The compact dimensions of the tried-and-tested two-stage SCT are retained, so that easy replacement is possible.
News and advantages at a glance
- There is no need for complicated procedures on the plant or journeys to remote pump locations to carry out manual adjustments.
- Pump installations that are difficult to access can be easily reached remotely.
- Reduced maintenance requirements, less wear and tear, lower spare part costs and a significantly longer pump service life due to the simple automated operation and more frequent adjustment at an early stage of the stator clamping.
- Precise adjustment of the optimum operating status in order to react quickly and easily to changing process conditions and ensure an optimal process result.
- Unplanned downtimes are now a thing of the past. The status of the pump is clearly visible at all times. The result of the readjustment is immediately visible in the performance of the pump and the wear reserve can be read off in the higher-level systems.
- All maintenance work can be carried out in a minimum of space, as there is no need for piping to be dismantled. Furthermore, there is no additional space requirement for disassembling the stator.
- Keeping an eye on the plant at all times and everywhere. Unnoticed changes or problems are a thing of the past thanks to the monitoring of the operating and pump status in the control system, on the Pump Monitor or optionally in the Seepex Connected Services.
Source: Seepex GmbH