New Technology for Old Parts: Advanced Manufacturing Techniques Enhance Performance of Pumping Systems
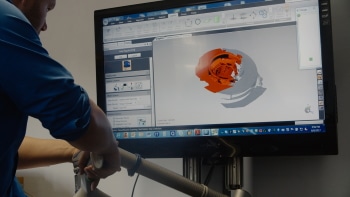
Handheld laser scanners can create precision 3D engineering drawings. (Image source: Sulzer)
Achieving the same goal for legacy equipment would appear almost impossible when spare parts are no longer stocked. However, cutting-edge design and manufacturing technology can minimize delays and offer improved performance.
Reliability and efficiency are essential for effective pump performance, but every asset will succumb to wear, erosion, corrosion or fatigue eventually. At this point, operators are reliant on the availability of parts, and in some cases additional engineering support, to complete a satisfactory repair and return the asset to normal operation.
Many critical processes use redundant equipment to maintain productivity while an asset is being repaired, but even in these cases, the total repair time needs to be kept to a minimum. For those without the ability to engage standby equipment, downtime can represent significant financial costs.
Grasping the challenge
Pumps are precision engineered for each task that they perform, and the impeller consists of complex, and sometimes unique, geometry to achieve the required performance and efficiency levels. It is also under constant attack from the pumped media, and gradually efficiency will be reduced as clearances increase and profiles are eroded.
When the time comes to source a new part, the first stop is the original equipment manufacturer (OEM), which will always offer replacement parts where possible. Some OEMs, such as Sulzer, have considerable expertise in parts manufacturing and reverse engineering of components for any make and model of pump. This can be especially important after sometimes decades of service, when some parts may no longer be available from stock, and lead times become an important factor.
Under these circumstances a specialist parts manufacturer is required, one that can use the original part to reverse engineer the new component. Fortunately, recent advances in engineering technology have enabled lead times to be significantly reduced as well as offering other advantages.
3D designs
Creating a set of 3D engineering drawings is now much less time-consuming, thanks to hand-held laser scanners and digital coordinate measuring machines (CMMs) that can measure items quickly and very accurately. Equipment, such as the HandySCAN 700 is a very compact device that is accurate to 30 µm.
When creating replacement parts for crucial pieces of equipment, speed is of the essence. Using the latest generation of laser scanners enables engineers to gather up to 480’000 points of data every second. Intersecting laser lines ensure that even the most complex geometry is captured accurately, which is essential in the recreation of an impeller.
For larger pieces of equipment that cannot be easily moved, on-site engineers can visit customers’ premises to offer specialist advice and take essential measurements to create new engineering drawings. Using multiple portable CMMs and laser scanners for on-site data acquisition allow dimensions to be repeatable within 0.025 mm (0.001 in.).
Once the basic dimensional data has been acquired, design engineers can then fine-tune the design of the new component. For example, the geometry of an impeller can be adjusted to make sure clearances are optimized. The designers can also make alterations to the original design to account for changes in the application or performance needs.
Creating the mold
The traditional process of casting a new component, such as an impeller, required a wooden pattern of the original part to be created and used with a sand-casting box. This is a very time-consuming process and it can take weeks to finalize the design of the pattern, which can be subject to considerable inaccuracies, especially if it has been stored for any length of time.
Today, 3D computer-aided design (CAD) files can be created in minutes using laser scanners, transferred to a wide variety of machine tools and robots, and used to create perfect reconstructions of the original part. One method is to utilize a 3D sand printer that uses the data to rapidly build a mold of the new component. Using layers of sand and adhesive, the 3D printer can create a mold that can withstand the high temperatures of molten metal that will form the new component.
As part of this process, design engineers use computational fluid dynamics to predict the flow of gases within the mold as the molten metal is poured. It is essential that the gases have effective escape routes, or vents, since trapped gases would lead to weaknesses in the new component. The vents can be incorporated into the 3D CAD drawing and included easily in the sand printing process.
Rapid manufacturing
State-of-the-art additive manufacturing technology provides complete precision molds and cores. The process takes about 48 hours to complete, but depending on the size of the components, multiple molds can be printed at the same time, making it more efficient.
Another method of creating a mold, which is often used for making casings, involves two halves, known as the cope and the drag, which are brought together to create the finished shape. Today, the process starts with a solid block of sand that is machined using a multi-axis CNC robot milling tool to create a precision mold as laid out in the 3D CAD drawings.
To produce a wooden pattern for the sand-casting box using traditional methods takes 2–6 weeks, depending on the complexity of the pattern form. Using a 3D sand printer removes the need for a pattern – the mold is printed directly and finished in less than 24 hours. Machining a precision mold from a sand block takes 2–4 hours.
Material improvements
Today, parts manufacturers have a vast array of alloys available to them and designers can determine the exact composition of a metal alloy by the type of component and its application; advanced metallurgy knowledge enables new components to be created with improved durability compared to the originals.
Once the basic shape has been established, the final precision profiles are delivered by CNC vertical turning lathes for impellers and bowls, horizontal shaft lathes, milling equipment and grinders. Working to the 3D CAD drawings, these machines sculpt and polish the parts to ensure perfect operation.
Defining quality
Throughout the design and manufacturing process, extensive quality control procedures and equipment are used to ensure that every part is manufactured to the highest standards. Just as the laser scanners determined the initial dimensions, so CMMs can be used to deliver confidence in the finished component.
As well as physical measurements, heat treatment, certified material reports, chemical analysis, and a range of material tests and non-destructive testing (NDT) can be carried out. These ensure the reliability of the parts as well as compliance with customer specifications and any changes from the original design.
As a leading independent maintenance provider and pump OEM, Sulzer offers a comprehensive range of services that include cutting-edge manufacturing techniques for fast delivery of components. With over 100 service centers around the world Sulzer provides customers with local engineering facilities that are supported by a global network of expertise and knowledge.
Engineering technology has advanced spectacularly over the past 10 years and the latest developments are enabling operators of legacy equipment to save time and maximize their investment by improving reliability and efficiency. By taking advantage of new materials and manufacturing techniques, it is possible to minimize downtime whilst also improving performance.
Source: Sulzer Ltd.