Ensure good workmanship around your ship’s pump systems
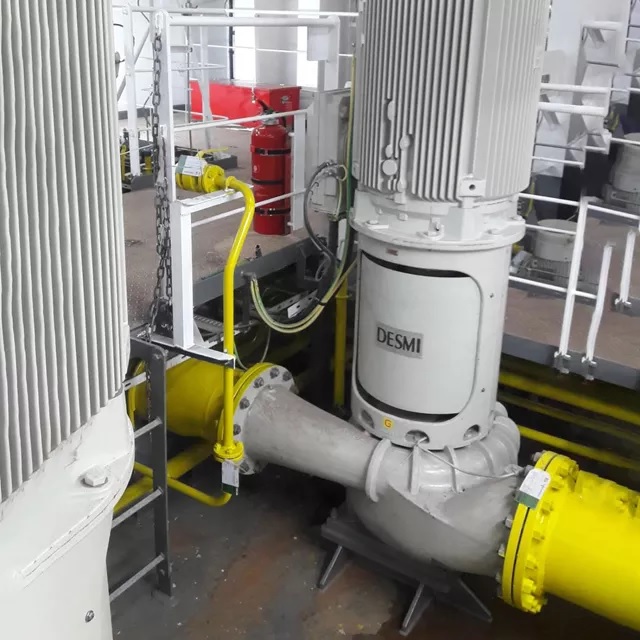
The motor is two-thirds of a pump’s weight. Make sure you have a solid foundation under the pump. (Image source: DESMI)
DESMI’s Sales and Application Manager in China, John Nielsen has a message for ship owners all over the world: “Be aware of how your pump systems are installed. Ensure good workmanship!”, he says. “That’s the bottom line. There are too many outfitting crews lacking practical experience.”
“Ship owners must thus make sure their site teams follow key guidelines for proper pump installation. Because most of the time, a pump breakdown is not due to a faulty pump”, John says.
With several years at DESMI and more than 20 years as a shipbuilder, John Nielsen knows what he is talking about. He offers a list of “do’s and don’ts” in pump installation for ship owners, superintendents, site teams and shipyards. “You need to be aware of these things”, he says. “A pump is just a component that will do exactly what it is designed to do. But if it’s not installed properly, then you can destroy it. It’s a bit like Murphy’s Law: If something can go wrong, it will. And in the end, the ship owners will have to bear the costs.”
A solid foundation
Solid pump foundations are at the top of John’s list. “It is extremely important that these are done correctly. The foundation has to be supported so there’s no chance of wobbling.” In other words, do not install the pump on a soft plate – a steel plate with no or missing support below. “There’s an old shipyard saying: You need the same amount of steel below the plate as you have on top of it.”
If the outfitting team wants to use weighted or spring-loaded supports, they must first check the design with DESMI or the steel engineer. “It is not up to the individual outfitting team to decide”, John says. “Most pumps today are vertical. And two-thirds of a pump’s weight is actually the electrical motor. Some pumps are four and a half tons meaning the electrical motor is three tons. This all calls for very good foundations to avoid vibration, etc.”
Pipes and valves
There are standard ISO rules for pipe routing, but these can be tricky to follow onboard a ship due to limited space. “So that means you have to think a bit alternatively,” John says. On a ship, make sure that the pipe design allows the liquid flowing to the pump on the suction side at a maximum velocity of 1 meter per second (m/s). This is a rule of thumb so that you avoid creating water vortex or cavitation that will eventually destroy the pump.
And then there are valve choices. On ships, a big number of valves are butterfly valves, mainly because this is an inexpensive valve type. But a butterfly valve only works in the pumping direction. This is why there are always a non-return valve in series with the butterfly on pumps pressure side. Otherwise, if pumps are working in parallel and one pump is dormant without installed non-return valve, the active pump will pump liquid to the other pump instead – no matter butterfly valve open or closed.
Furthermore, it is important that the valves are full bore (full port). This means that when the valve is open, it has the same diameter as the pipe. Don't use valves that are slightly smaller in diameter than the pipe. This will create small vortexes inside the pipe and will eventually destroy the pipe and the valve.
Materials and corrosion
It is also important to plan carefully for the pump material used, depending on the liquid it is pumping and conditions around it. Material choices for pumps include bronze, nickel aluminum bronze (NiAIBz), gun metal, cast iron, cast steel, stainless steel 304, stainless steel 316, and duplex. “All of these materials have each their own advantages and disadvantages. It’s important to consider these”, John says.
DESMI typically uses stainless steel 316 or duplex for alkaline or acidic liquids, for example. “But you have to handle this material very carefully. You need to know what you’re doing. Otherwise they can corrode.”
DESMI designs its seawater pumps typically of NiALBz for a designed sea water temperature of 32°C. Sea Water temperature above that becomes much more corrosive. Likewise, cast iron is not a good choice for seawater pumps in warm areas. “If you’re operating in Greenland, then a cast iron pump can last a long time, but not if you’re working in the tropics.”
For low temperature freshwater pumps, the DESMI design is using cast iron housing and NiAlBz impellers, designed for a water temperature of 36°C. “The problem with fresh water on a ship is that you need additives to remove oxygen as to avoid corrosion/rust. But there are many different kinds of additives and some of these make the water very viscous, and as result water can be leaking everywhere. Another problem with additives is that these chemicals change waters pH values. This is also something that needs to be considered when selecting materials.”
Be aware of the potential for galvanic corrosion (also called bimetallic corrosion) when considering materials. This is a phenomenon that occurs when two different materials are put together – like copper and iron in salt water. Salt water will act as an electrolyte. “It's a slow killer”, John says. “It takes a long time before you find out it is a problem.”
”It is the same principle as used for protection steel with zinc anodes.”
In the case with copper and iron – the iron will slowly move to the copper.
“I think many people have experienced that calcium is building up inside pipes, etc. – this is also due to galvanic element effect.”
John’s main advice about material choice is to look carefully at what is supposed to be used in different conditions and listen to the experts.
“We see many cases where customers specify bronze. And yes, we can use bronze, but we prefer to use nickel aluminum bronze, because it is more rigid. And it’s also better for avoiding galvanic element corrosion. So, this is the DESMI choice.”
“One last word in this materials section, and that is related to how to increase the pump efficiency. Most pumps have an efficiency of 75-80%”, John says. “Some ship owners require 80-83%. And this demands more than just an update of the mechanics. While there are many ways to do this, coating a pump internally with a glass-like coating is the most common method. It is also possible to use an electrical control system to increase the efficiency. More and more shipowners are asking for the higher efficiency.”
Source: DESMI A/S