ViscoTec – 24/7 production of laundry detergent pods and dishwasher tabs
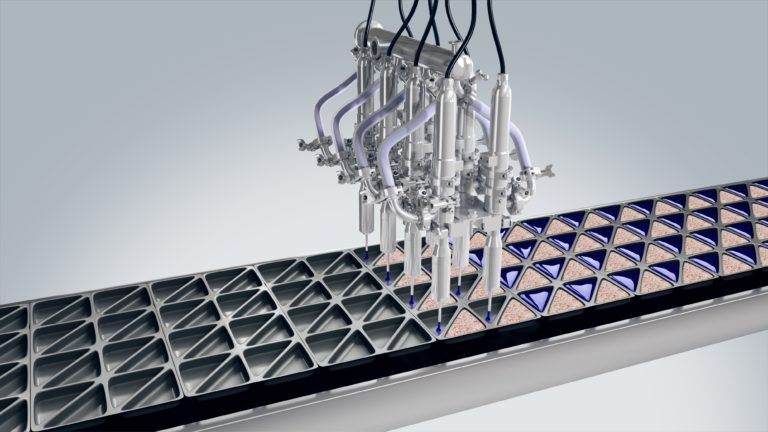
Rendering ViscoTec hygienic dispenser for filling dishwasher tabs. (Image source: ViscoTec Pumpen- u. Dosiertechnik GmbH)
How exactly should laundry detergent be dosed so that the laundry is completely clean, without the environment suffering? Does the dishwasher detergent compartment have to be filled completely in order to achieve streak-free cleanliness? But then it might not be possible to close the drawer properly? These are just a few of the questions that are frequently discussed on the Internet for example. These considerations are being eliminated, as laundry and dishwashing detergent is available in pre-dosed packages, so-called pods or tabs. Their application ensures that only the right quantity of detergent recommended by the manufacturer is used per wash cycle. Environmentally harmful overdoses are avoided. And the laundry is not over exposed.
ViscoTec hygienic pumps are used for filling viscous cleaning agents into these pods or tabs. For example, in cooperation with the machine builder Harro Höfliger, highly industrial production and packaging equipment is developed that enables 24/7 production and operates fully automatically. There are a number of points that need to be considered during the manufacture of the tabs and pods: In order to obtain the useful pads, the detergent is dosed onto a water-soluble film, which then dissolves in the washing machine or dishwasher. "Companies come to us with a design where the shape, number of chambers and filling material is already specified," explains Jürgen Luka, Engineering & Innovation Services (EIS) department at Harro Höfliger. "For example, they would like a pouch with three chambers containing 15 grams of powder, five grams of gel and five grams of liquid. Both the gel and the liquid can be applied with the ViscoTec pumps.”
Detergent pods
The material to be dosed for the detergent pods has a gel-like, viscous texture and poses no real challenges for ViscoTec’s dosing pumps. However, there are two special advantages of using progressive cavity pumps for dosing: On the one hand, they are easy to clean automatically, and, on the other hand, they have a particularly short cycle time, which is achieved by only employing high-quality materials. ViscoTec hygienic pumps and dispensers can be thoroughly cleaned within the dosing process without the need to dismantle them (CIP). Automatic rinsing is particularly advantageous when changing the color of the dosing material, for example. It saves time and downtimes are greatly reduced.
Dishwasher tabs
Particularly abrasive suspensions are dosed into dishwasher tabs. One challenge here is to counteract sedimentation of any solids during the entire dosing process. ViscoTec has met this challenge by circulating the dosing material within the complete system. It remains in constant motion. Filling takes place within the flow movement. This concept is made possible by integrating a bypass into the dosing pump. In this bypass, the material can be kept in constant motion during the dosing process and also when the system is at a standstill. This also prevents sedimentation in the pump feed. The dosing pumps comply with the requirements of the GMP and FDA guidelines. The complete filling system consists of a storage container with agitator, an RD hygienic feed pump and several hygienic dispensers. A further challenge is the abrasiveness of the materials to be dosed: The abrasive dosing materials usually cause above-average wear in filling systems. Thanks to the stainless steel/elastomer pairing in the rotor and stator of the ViscoTec dosing pumps, particularly long service lives are achieved in contrast to steel/steel combinations in piston pumps. By adopting the endless piston principle used in the ViscoTec products, the materials are dosed or filled purely volumetrically and almost wear-free. A decisive benefit of this technology lies in the resulting conveying chamber, whose volume remains absolutely constant during movement.