Thermal Management in Printed Circuit Boards: Successful Dispensing Test of Thermal Paste
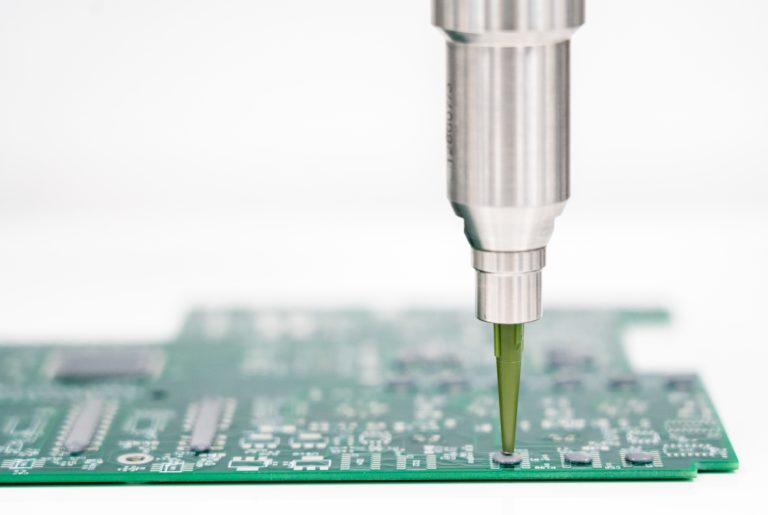
Dispensing tests of the highly abrasive, highly viscous 1-component thermal paste. (Image source: ViscoTec Pumpen- u. Dosiertechnik GmbH)
The extremely abrasive and, at the same time, highly viscous material had to be dispensed onto a printed circuit board while meeting the highest accuracy requirements.
The finished circuit boards are installed in various electronic components in the subsequent manufacturing process. The thermal paste helps to support the thermal heat management there and ensures optimum heat transfer to the outside.
For the dispensing tests, a 1-component 3RD8 dispenser with ceramic rotor was used and powered by a ViscoPro-C servo drive. The material was conveyed via a ViscoMT-C cartridge emptying system.
Challenges in dispensing abrasive thermal paste
Abrasive pastes cause increased wear. If properties such as high viscosity of the materials are then added, many common dispensing systems and technologies, such as piston pumps, reach their limits. They cannot meet the high demands of service life and precision. ViscoTec is the specialist for these materials in particular. With the endless piston principle, ViscoTec succeeds in reducing wear to a minimum and meeting the highest precision requirements. And by using the ceramic rotor in addition to ViscoTec's standard equipment, the service life of the dispensing equipment can be increased many times over, even when dispensing highly abrasive materials.
The dispensing tests show that despite the high viscosity and abrasion of the thermal paste, the individual lines and dots were dispensed very precisely. The speeds of the dispenser and robot were perfectly combined. There was no dripping of the material.
As well as perfect dispensing results, this also means less downtime due to less maintenance work and reduced cost on wear parts for the customer. In addition, material waste is minimized and contamination of components, as well as unintentional dripping, are prevented. This in turn ensures fewer rejects.