Gestión térmica en placas de circuito impreso: prueba de dispensación exitosa de pasta térmica
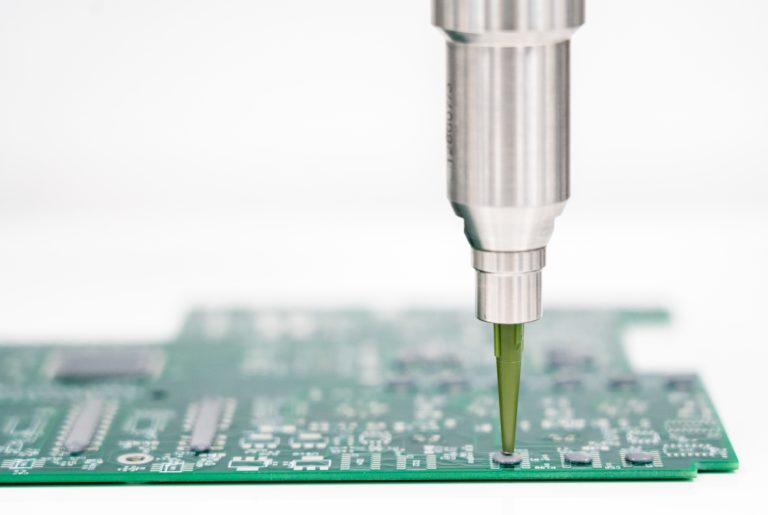
Ensayos de dosificación de la pasta térmica monocomponente altamente abrasiva y viscosa. (Fuente de la imagen: ViscoTec Pumpen- u. Dosiertechnik GmbH)
El material extremadamente abrasivo y, al mismo tiempo, altamente viscoso tuvo que ser dispensado en una placa de circuito impreso cumpliendo con los más altos requisitos de precisión.
Las placas de circuito terminadas se instalan en varios componentes electrónicos en el proceso de fabricación posterior. La pasta térmica ayuda a respaldar la gestión del calor térmico allí y garantiza una transferencia de calor óptima al exterior.
Para las pruebas de dispensación, se utilizó un dispensador 3RD8 de 1 componente con rotor cerámico y alimentado por un servoaccionamiento ViscoPro-C. El material se transportó a través de un sistema de vaciado de cartuchos ViscoMT-C.
Desafíos en la dosificación de pasta térmica abrasiva
Las pastas abrasivas provocan un mayor desgaste. Si luego se agregan propiedades como la alta viscosidad de los materiales, muchos sistemas y tecnologías de dispensación comunes, como las bombas de pistón, alcanzan sus límites. No pueden satisfacer las altas exigencias de precisión y vida útil. ViscoTec es el especialista en estos materiales en particular. Con el principio de pistón sin fin, ViscoTec logra reducir el desgaste al mínimo y cumplir con los más altos requisitos de precisión. Y al utilizar el rotor de cerámica además del equipo estándar de ViscoTec, la vida útil del equipo de dispensación se puede aumentar muchas veces, incluso cuando se dispensan materiales altamente abrasivos.
Las pruebas de dispensación muestran que a pesar de la alta viscosidad y abrasión de la pasta térmica, las líneas y puntos individuales se dispensaron con mucha precisión. Las velocidades del dispensador y el robot se combinaron perfectamente. No hubo goteo del material.
Además de unos resultados de dispensación perfectos, esto también significa menos tiempo de inactividad debido a un menor trabajo de mantenimiento y un menor costo de las piezas de desgaste para el cliente. Además, se minimiza el desperdicio de material y se evita la contaminación de los componentes, así como el goteo involuntario. Esto, a su vez, asegura menos rechazos.