Technical article: Production process efficiency through digital supplier documentation
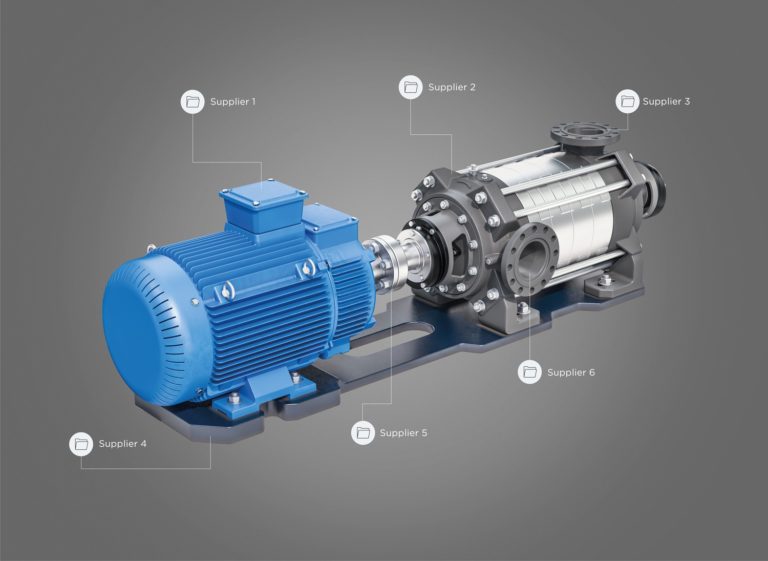
Production process efficiency through digital supplier documentation. (Image source: Fabasoft International Services GmbH)
In light of the boom that the German plant and mechanical engineering sector is currently enjoying, companies will have to be particularly inventive if they hope to outperform the competition and future-proof their operations.
Alongside large order volumes, substantial documentation requirements arising from contractual and legal parameters also need to be satisfied: Concluding the project acceptance process on time requires complete supplier documentation.
This means that for every single pump component—in addition to the project and product-specific documents—safety documents, guarantees, certification, approval and licensing documents or maintenance manuals also have to be provided. As a result, supplier documentation in the specialized fields of mechanical engineering can comprise upwards of several thousand documents. Documents are often transmitted using upload servers or as e-mail attachments. The diverse communication channels make it more and more complicated for project managers to keep track of the current documentation status so that they can determine which suppliers have already provided the required documentation services and where there is a need for action. If documents are incomplete or missing from the supplier documentation, delays in the progress of the project can result, or worse, companies might even face contractual penalties. On top of that, exchanging documents by e-mail and various download platforms also curtails project efficiency and complicates efforts to keep track of whether all parts of the documentation are complete.
Central digital documentation—an information hub
Flawless and centralized documentation is crucial if the technical editing in specialized mechanical engineering and plant construction is to be handled efficiently across production sites and corporate boundaries. This is where a cloud-based system is well suited to meet the requirements of all parties involved—be it the component manufacturer, the product manufacturer, the plant manufacturer, the authorities, or the customer—effectively and in compliance with the required safety standards.
Permanent availability
The business environment prevailing in plant and mechanical engineering is decidedly international and underscores the advantages of permanent availability offered by cloud-based solutions. Supplier documentation can be created around the clock from any location, and document approvals can be conveniently handled in an app. Workflow enables efficient coordination across national borders and time zones. The only prerequisite is a (mobile) device with an HTML5-compatible web browser and an Internet connection. Even if the Internet connection is temporarily down, cloud-based products offer an offline mode. Documents that are “in progress” are automatically synchronized back into the supplier documentation as soon as the Internet connection is re-established.
Supplier documentation in practice
A leading global provider of pumps, valves, and systems in building services engineering, industry, water management, the energy sector, and mining is utilizing cloud-based supplier documentation and digitalizing its procurement processes, including the documentation.
The company’s procurement process looks like this: The pump manufacturer receives a product order. The order is entered into SAP and broken down into order items and their corresponding trade parts before being transferred to the digital supplier documentation system. The maximum document list is already stored in the software solution, which means that the design engineers only need to select the document types that are specifically needed for the pump (operating manuals, data sheets, wiring diagram, certifications, and the like) from the parts list. After that, the pump manufacturer determines and commissions its sub-suppliers for the various trade parts. Component orders to the sub-suppliers are entered into the relevant ERP (enterprise resource planning) system. At the same time, every sub-supplier is given access to its own “repository” in the cloud-based supplier documentation system and can incorporate all the different types of documentation required or even create them directly using the document templates. All information relating to the documentation is transmitted, processed, and approved in an organized and traceable format by means of document status and automated workflows so that the component production can start without delay. The pump manufacturer can check the documentation status of each individual sub-supplier quickly and efficiently and take corrective action if necessary, and can also supplement the overall documentation with its own documents from any of the sites at which the pump is physically manufactured. Once the documentation is complete and covers all line items and trade parts, it can be forwarded to the customer—once again via the supplier documentation in the cloud. To do this, the customer either receives access to the supplier documentation or the documentation is transmitted to a customer system by means of an interface.
The bottom line
The unique advantages of a cloud-based version of digital supplier documentation lie in the speed of implementation in the company and the flexibility in integrating the stakeholders along the supply chain. The solution reduces both the costs and the internal workload involved in operating and maintaining the IT infrastructure and makes them more predictable. The entire supplier documentation creation process is made transparent and traceable for all parties involved. Delays resulting from misunderstandings in communication are eliminated. Nevertheless, when choosing cloud-based products, data protection and data security issues merit careful consideration; selection criteria include data storage in the EU by the provider and appropriate certification.
Author: Andreas Dangl is the Business Unit Executive for Cloud Services at Fabasoft.