Sulzer Creates Hybrid Additive Manufacturing Process to Minimize Lead Time on Components
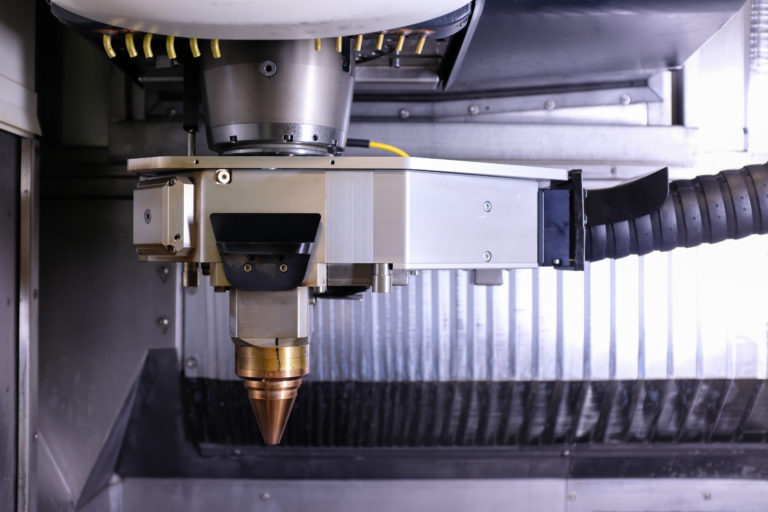
The cutting-edge laser metal deposition head (Image source: Sulzer Ltd.)
Pumping systems are central to moving raw materials as well as the finished product, and many processes in between. So standby pumps are retained as well as spare parts, such as impellers. Now, there is an opportunity to reduce this stock-holding. Manufacturing technology has taken a significant step forward following the completion of validation and trial part manufacture. The technology incorporates laser metal deposition and precision machining. Additive Manufacturing (AM) using this technology can create finished parts in one machine, significantly reducing lead times.
Developing technology
Chevron and Sulzer were interested in developing their partnership so as to reduce parts inventory and improve flexibility.
Back in the 1990s, Sulzer played an important role in creating laser metal deposition technology. Building on this background the company has constantly been working to develop and implement new additive manufacturing techniques for key applications.
Today, the company has developed and implemented additive manufacturing technology to produce new pump impellers of the highest quality, without the need for tooling. The project offers Chevron the potential to reduce lead times for new parts without compromising on quality.
Gathering expertise
For the past two years, Sulzer and Chevron have established a joint project. The collaboration also involves other partners such as suppliers of equipment for the manufacturing cell, powder suppliers, audit and certification bodies.
Charles Soothill, Head of Technology for Rotating Equipment Services for Sulzer explains: “Together, the teams have worked to combine the capabilities of 5-axis CNC milling and laser metal deposition equipment to create this hybrid additive manufacturing process. This combination of additive and subtractive elements enables the new process to be quicker because setups are avoided.”
Simplifying complex geometries
Starting with a piece of stock material of the required grade and quality loaded into the hybrid machine tool, it is possible to machine the most complex geometries of the eye of the impeller. Material is then added and finish-machined while remaining in the same cell. This process enables Sulzer to create finished machined quality on far more complex components than would normally be possible with a conventional machine tool.
In addition to all the standard cutting tools that are stored in the tool changer, there is also the laser metal deposition head, which can be used to build up material on the workpiece, or core. The machine can quickly change between the milling tools and the laser head, a process that would normally require the component to be repositioned in a separate machine.
The additive technology has also required the development of new processes, using a fine powder, 50 to 100µm, and a laser. The powder is melted by the laser and deposited on the surface of the stock material held in the hybrid machine tool.
Hybrid impeller manufacturing
Pump impellers are complex components to manufacture, the internal geometry is too complicated to be created by a conventional milling machine. Starting with a forging, the core of the impeller can be machined using a 5-axis milling machine. Then further material is added to the outside of the impeller using laser metal deposition.
The use of milling tools means that the internal hydraulic surfaces have a very high-quality finish, much better than those achieved with a casting process. The process of adding material and machining is repeated until the complete impeller emerges. The whole process, which can be completed in a matter of days, is much quicker than casting a new component, which can typically take 15 – 20 weeks.
The greatly reduced build time for a new impeller means that, in the event of a pump needing a new component, the standby pump can be brought online while the new part is manufactured and delivered. Although this time could be reduced further if necessary, the consensus is that a few days is sufficient for the majority of applications.
Proving the theory
The development work has now been put into practice and applied to a real-world application. Chevron has a CPT pump from Sulzer operating with a corrosive fluid, an application that requires specific material properties to ensure the durability of the pump. The impeller was identified for replacement and an ideal subject for the new manufacturing process.
Using the original design drawings, a 3-dimensional model was fine-tuned and a final set of coded instructions for the hybrid manufacturing machine was generated. Within a few hours the new impeller had been created and was ready to be installed.
The new impeller was installed in the pump and tested at Sulzer first. It has now been operating successfully since its installation on site in 2019. Both Sulzer and Chevron are confident in the performance and durability of the new component.
Robert Rettew, Program Manager, Materials Technology Development at Chevron, comments: “We have worked closely with Sulzer to develop the technology and systems required to achieve hybrid manufacturing and now Chevron is the first customer to benefit from this cutting-edge solution. There is considerable opportunity to increase the applications and widen the scope of materials used in the process.”
Chevron has a strategic plan to take advantage of new and innovative technologies that can offer improvements for its operations and improve efficiency. One of these is additive manufacturing. This process is also very important for components that are now obsolete, enabling parts for heritage assets to be sourced with a short lead time.
Charles Soothill concludes: “For Sulzer, the goal is to offer customers the best possible service and, when time is of the essence, deliver the solution with the shortest lead time, while maintaining the highest quality standards. In addition to receiving a new part quickly, customers also benefit from the latest design standards that have benefitted from decades of experience in designing and manufacturing pumps.”
Source: Sulzer Ltd.