Sulzer crea un proceso híbrido de fabricación aditiva para minimizar el tiempo de entrega de los componentes
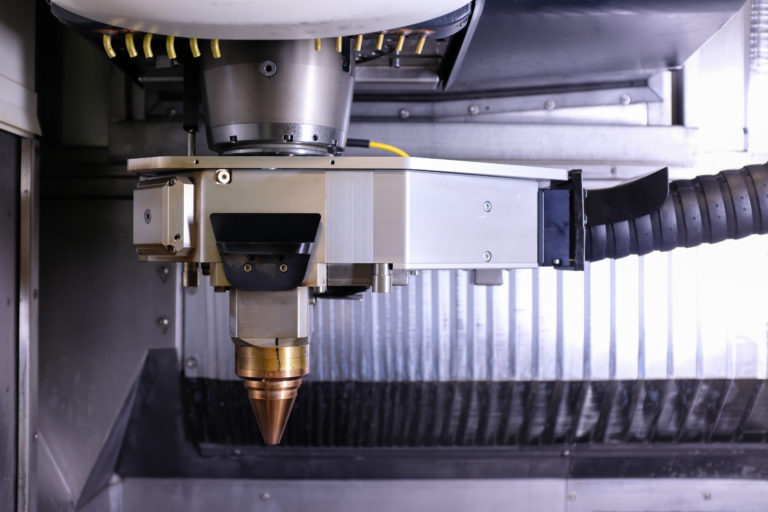
El cabezal de deposición de metal láser de última generación (Fuente de la imagen: Sulzer Ltd.)
Los sistemas de bombeo son fundamentales para mover las materias primas, así como el producto terminado, y muchos procesos intermedios. Por tanto, se conservan las bombas de reserva y las piezas de repuesto, como los impulsores. Ahora, existe la oportunidad de reducir esta tenencia de existencias. La tecnología de fabricación ha dado un importante paso adelante tras la finalización de la validación y la fabricación de piezas de prueba. La tecnología incorpora deposición de metal láser y mecanizado de precisión. La fabricación aditiva (AM) que utiliza esta tecnología puede crear piezas terminadas en una máquina, lo que reduce significativamente los plazos de entrega.
Desarrollando tecnología
Chevron y Sulzer estaban interesados en desarrollar su asociación para reducir el inventario de piezas y mejorar la flexibilidad.
En la década de 1990, Sulzer jugó un papel importante en la creación de tecnología de deposición de metales por láser. Basándose en estos antecedentes, la empresa ha estado trabajando constantemente para desarrollar e implementar nuevas técnicas de fabricación aditiva para aplicaciones clave.
Hoy, la empresa ha desarrollado e implementado tecnología de fabricación aditiva para producir nuevos impulsores de bombas de la más alta calidad, sin necesidad de herramientas. El proyecto ofrece a Chevron el potencial de reducir los tiempos de entrega de piezas nuevas sin comprometer la calidad.
Reuniendo experiencia
Durante los últimos dos años, Sulzer y Chevron han establecido un proyecto conjunto. La colaboración también involucra a otros socios como proveedores de equipos para la célula de fabricación, proveedores de polvo, organismos de auditoría y certificación.
Charles Soothill, director de tecnología de servicios de equipos rotativos de Sulzer, explica: “Juntos, los equipos han trabajado para combinar las capacidades del fresado CNC de 5 ejes y el equipo de deposición de metales por láser para crear este proceso híbrido de fabricación aditiva. Esta combinación de elementos aditivos y sustractivos permite que el nuevo proceso sea más rápido porque se evitan las configuraciones ".
Simplificar geometrías complejas
Comenzando con una pieza de material de stock del grado y calidad requeridos cargada en la máquina herramienta híbrida, es posible mecanizar las geometrías más complejas del ojo del impulsor. Luego, el material se agrega y se maquina de acabado mientras permanece en la misma celda. Este proceso permite a Sulzer crear calidad de mecanizado acabado en componentes mucho más complejos de lo que normalmente sería posible con una máquina herramienta convencional.
Además de todas las herramientas de corte estándar que se almacenan en el cambiador de herramientas, también existe el cabezal de deposición de metal láser, que se puede utilizar para acumular material en la pieza de trabajo o núcleo. La máquina puede cambiar rápidamente entre las herramientas de fresado y el cabezal láser, un proceso que normalmente requeriría reposicionar el componente en una máquina separada.
La tecnología aditiva también ha requerido el desarrollo de nuevos procesos, utilizando un polvo fino de 50 a 100 µm y un láser. El polvo es derretido por el láser y depositado sobre la superficie del material almacenado en la máquina herramienta híbrida.
Fabricación de impulsores híbridos
Los impulsores de bombas son componentes complejos de fabricar, la geometría interna es demasiado complicada para ser creada por una fresadora convencional. Comenzando con una forja, el núcleo del impulsor se puede mecanizar utilizando una fresadora de 5 ejes. Luego, se agrega más material al exterior del impulsor usando deposición de metal por láser.
El uso de herramientas de fresado significa que las superficies hidráulicas internas tienen un acabado de muy alta calidad, mucho mejor que los que se logran con un proceso de fundición. El proceso de adición de material y mecanizado se repite hasta que emerge el impulsor completo. Todo el proceso, que se puede completar en cuestión de días, es mucho más rápido que la fundición de un nuevo componente, que normalmente puede tardar entre 15 y 20 semanas.
El tiempo de construcción muy reducido para un nuevo impulsor significa que, en caso de que una bomba necesite un nuevo componente, la bomba de reserva se puede poner en línea mientras se fabrica y entrega la nueva pieza. Aunque este tiempo podría reducirse aún más si fuera necesario, el consenso es que unos días son suficientes para la mayoría de aplicaciones.
Prueba de la teoría
El trabajo de desarrollo ahora se ha puesto en práctica y se ha aplicado a una aplicación del mundo real. Chevron tiene una bomba CPT de Sulzer que funciona con un fluido corrosivo, una aplicación que requiere propiedades específicas del material para garantizar la durabilidad de la bomba. El impulsor fue identificado para reemplazo y un sujeto ideal para el nuevo proceso de fabricación.
Utilizando los dibujos de diseño originales, se ajustó un modelo tridimensional y se generó un conjunto final de instrucciones codificadas para la máquina de fabricación híbrida. En unas pocas horas se había creado el nuevo impulsor y estaba listo para ser instalado.
El nuevo impulsor se instaló en la bomba y se probó en Sulzer primero. Ahora ha estado funcionando con éxito desde su instalación en el sitio en 2019. Tanto Sulzer como Chevron confían en el rendimiento y la durabilidad del nuevo componente.
Robert Rettew, Gerente de Programa, Desarrollo de Tecnología de Materiales en Chevron, comenta: “Hemos trabajado en estrecha colaboración con Sulzer para desarrollar la tecnología y los sistemas necesarios para lograr la fabricación híbrida y ahora Chevron es el primer cliente en beneficiarse de esta solución de vanguardia. Existe una oportunidad considerable para aumentar las aplicaciones y ampliar el alcance de los materiales utilizados en el proceso ".
Chevron tiene un plan estratégico para aprovechar tecnologías nuevas e innovadoras que pueden ofrecer mejoras para sus operaciones y mejorar la eficiencia. Uno de ellos es la fabricación aditiva. Este proceso también es muy importante para los componentes que ahora están obsoletos, lo que permite que las piezas de los activos patrimoniales se obtengan con un plazo de entrega corto.
Charles Soothill concluye: “Para Sulzer, el objetivo es ofrecer a los clientes el mejor servicio posible y, cuando el tiempo es esencial, entregar la solución con el menor tiempo de entrega, manteniendo los más altos estándares de calidad. Además de recibir rápidamente una pieza nueva, los clientes también se benefician de los últimos estándares de diseño que se han beneficiado de décadas de experiencia en el diseño y fabricación de bombas ”.
Fuente: Sulzer Ltd.