Smart Monitoring IoT Solution for Industrial Pumps from LEWA and generic.de Receive Allianz Industrie 4.0 Award
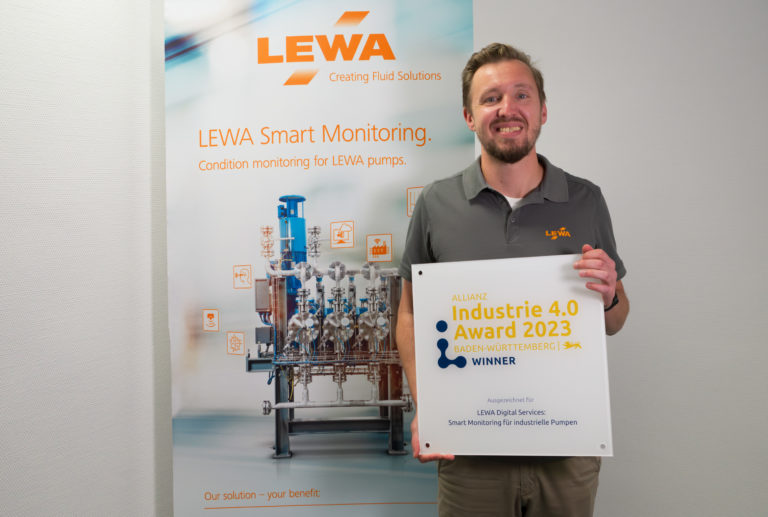
Pump manufacturer LEWA and its partner for digital product development generic.de were honored with this year's Allianz Industrie 4.0 Award (Image source: Lewa GmbH)
With the help of the intelligent monitoring system, industrial pumps can be reliably and seamlessly checked, monitored and evaluated during operation, even in very remote locations. The prize was awarded at the Startup the Future Event on November 22, 2023, in Stuttgart.
The continuous operation of pump systems in critical applications goes hand-in-hand with high expenditures for monitoring and maintenance. Recording parameters such as flow rate, temperature and pressure often require expensive and high-maintenance instrumentation as well. "Our pumps meter and convey expensive and sensitive fluids. For this reasons, our customers have very high expectations in terms of process reliability. Over the past few years, we have acquired a great deal of monitoring expertise for our pumps," explained Moritz Pastow, Program Manager Digital Services & IoT at LEWA GmbH. The Smart Monitoring IoT system designed and realized together with generic.de enables LEWA to share its expertise in diagnostics with end customers automatically and based on key figures. The system outputs error states with precise error localization and in plain text for increased user-friendliness. At the same time, the technology is the basis for a whole range of other possible applications, such as predictive maintenance, intelligent energy management, remote service and performance analyses.
Precise monitoring even at the edge of civilization
A lot is demanded from the sensors used: They must also guarantee high-frequency data acquisition at 1,000 Hz for high-pressure applications up to 1,000 bar with highly toxic, extremely hot or cold, explosive and abrasive fluids. The industrial pumps are integrated into processes that must function 24/7. "Technologically, the project was extremely demanding. We are not just dealing with standard sensor values here. Up to 2,000 signals per second must be tapped and processed cleanly. In addition, online and offline connectivity was a major challenge," reported Michael Puder, CEO of generic.de software technologies AG. To make matters worse, many of the pumps provided by LEWA are used in the most remote places in the world: for example, on offshore oil platforms. The system must therefore be able to enable continuous monitoring, even without a permanent Internet connection.
Users have a practical customer portal for remote access: "All parameters and statuses can be called up at any time and from any location," explained Pastow. As a single touchpoint for customer self-service, the portal allows LEWA customers to continuously monitor all pumps in the form of digital twins via special dashboards. In addition, important documents and spare parts lists can be made available via the digital asset management system. Connection to the end customer's ERP system is also planned.
Product development with agile transformation included
New technologies and the growth of networking in the value chain have forced companies to pursue cross-company approaches to the digital transformation. "We very quickly realized that the classic development processes from mechanical engineering didn't really work for a digital product like 'Smart Monitoring'," Pastow confirmed. The project had more than just an impact on LEWA's technology portfolio. Agile methods have also found their way into the mechanical engineering company's product development processes.
Source: LEWA GmbH