Simple steps to keep onsite treatment within consent
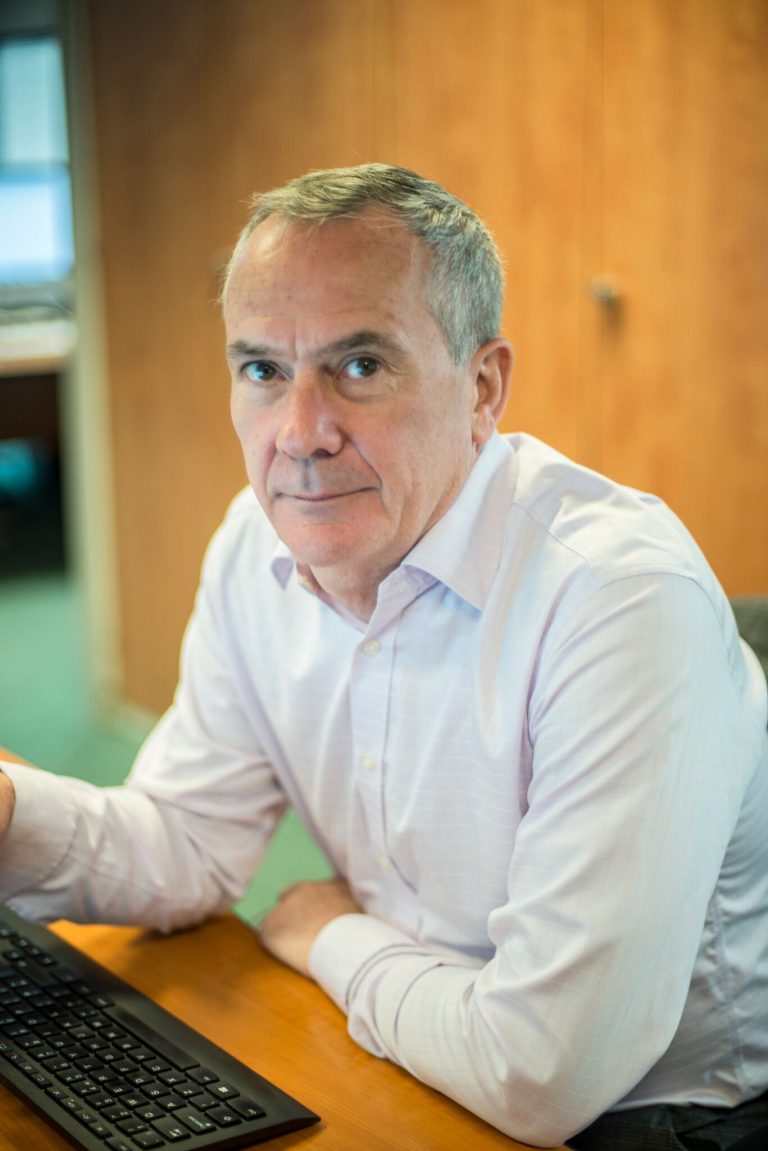
Andrew Baird, technical director, WPL. (Image source: WPL Ltd.)
The regulator’s toughening approach to discharge permit breaches, a number of high profile prosecutions and record fines for polluters, along with increased public awareness, means customers are also demanding more from their water utilities. While much of the Environment Agency’s scrutiny has been directed at the water sector – in 2019, it told the industry to clean up its act and protect the environment from pollution – it is clear that all companies with onsite treatment are coming under increasing pressure to have reliable processes in place.
A breach of trade effluent consent, which is granted by water companies to companies that discharge into the public sewer, is a criminal offence and penalties can range from an early warning notice to a fine or prosecution or, in the most serious cases, imprisonment. Financial and reputational implications are also significant. The cost of reactive mitigation for the most serious breaches, such as clean-ups or tankering, can potentially run into millions and risks thrusting the company brand into the spotlight for the wrong reasons.
WPL specialises in packaged wastewater treatment plants and sees different companies making the same avoidable mistakes that result in permit breaches - but the solutions are often simple.
Maintain onsite equipment
Equipment failure lies behind the majority of permit breaches, and often occurs due to a lack of maintenance.
When it comes to commercial or industrial companies, onsite effluent treatment is not necessarily seen as a core part of the operation and interest can be lacking. This can result in this vital equipment, that may underpin the efficiency of the whole site, being some of the least loved.
When installing new kit, we advise management to give the responsibility of maintaining it to specific employees who understand not only the mechanics but also the importance of the plant. Having enthusiastic champions of the equipment means it is more likely to receive the attention it deserves. Of course, with the Covid-19 pandemic leading to urgent reviews of business continuity plans, it seems good practice to assign this responsibility to a team rather than an individual, so the knowledge is not lost if one person becomes unavailable
Testing and trials
Performance and commercial shocks caused by discrepancies between designs and the delivery of a project can be avoided by conducting detailed reviews and pilot trials ahead of installing permanent plant. WPL can undertake in-depth advance testing in two ways - laboratory testing and onsite pilot trials.
Industrial laboratory service
Bespoke lab-scale reviews are conducted at WPL’s in-house facility to ascertain the profile of the effluent and ensure that the correct dosing regime is implemented, based on the requirements of environmental discharge permits. WPL’s process scientists carry out a separation test on effluent samples from the specific site and replicate appropriate treatment processes from WPL’s range which includes dissolved air floatation (DAF), biological treatment and settlement options.
Depending on the specific consent requirements, scientists can monitor chemical oxygen demand (COD) and biochemical oxygen demand (BOD) and levels of pollutants such as greases, phosphates, nutrients and nitrates to see if they are achieving the separation required.
Based on the analysis, a report is produced that determines the best technology and cost of the final scheme. This kind of testing has a quick turnaround with results returned in about a week. It causes little disruption to the customer and allows designers to rule out different technologies, saving time in researching options that might not work.
Onsite pilots
Following a lab review, an onsite pilot project is usually recommended to identify the precise equipment required. Pilots allow engineers to really look closely at factors including chemical and power consumption and sludge production to give a very accurate indication of how the plant will operate and the costs, giving the customer confidence that there will be no surprises. They can seem expensive but they may save money in the long run.
WPL recently built a permanent dissolved air flotation (DAF) unit on the site of a food manufacturer, which only wanted a lab review and not a pilot. It transpired the effluent being discharged was different from the sample given for lab testing – the sugar content differed vastly and could not be effectively removed.
Samples are variable in industrial treatment and the pilot would have picked this up very quickly, saving the customer time and money. An additional biological treatment plant has since had to be installed on the site.
Repurpose existing equipment
The solution to failing consent may not always require a large investment or the rebuilding of infrastructure. In many cases, just a single piece of equipment is needed, or, where an existing piece of kit fails, it can often be repurposed.
WPL’s Hybrid-SAF is a highly efficient biological treatment technology with custom-built cells can be retrofitted into any onsite vessels regardless of shape or size. This can improve the process to give it a 20-year life expectancy to meet consent and is significantly cheaper than rebuild projects.
Staff training
Of course, the solution to consent failure may not even be engineering-based. It can be a case of better staff training and revamped internal policy. For example, in the food industry, breaches can occur because employees are not scraping utensils before they wash them, meaning food debris and grease washes into the public sewer – resulting in a breach.
Education and ongoing training can really help prevent equipment and processes breaking down, ensuring the treatment plant remains fully compliant and continues to protect the environment. WPL can offer advice on all of these issues and support companies who are concerned about onsite treatment facilities failing consent.
Source: WPL Limited