Scaba Heavy-Duty Agitators Save Energy in Sulphur Melters
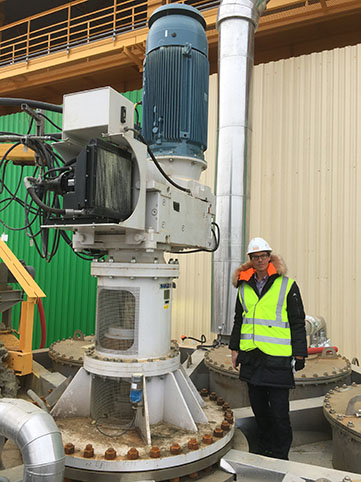
Scaba 240FVPT-Sff agitator operates smoothly at the PhosAgro Cherepovets site in Russia. (Image source: Sulzer Ltd.)
The challenge
Both melters were designed with six steam heating coils, and heat transfer was essential to achieve the required melting capacity. The design temperature for the melted sulphur was 130°C. A proposed agitator had a 200 kW motor with three impellers, whereo the lower one was a pitch blade turbine. The main challenges were:
- High heat transfer requirement
- Heavy-duty application
- Corrosive environment in the gas phase
- Large ambient temperature range between -47°C and +40°C
The solution
Sulzer calculated that a motor capacity of 132 kW would be enough, instead of 200 kW. This could be achieved with a Scaba agitator and high-efficiency SHP propellers on two levels. The result was verified in a computational fluid dynamics (CFD) analysis that proved that the propellers were correctly positioned and that no pitch blade turbine was needed.
Because the agitators operate with a variable frequency drive (VFD), it was, however, decided to install a 200 kW motor, but to operate it at 132 kW. The additional power is only a reserve for extremely cold conditions, and the normal operating speed is a maximum of 132 kW. This gives extra safety, but still substantial energy savings.
The agitators are running at 132 kW, or even lower, which proves that the hydraulics are excellent. The Scaba agitators operate smoothly and with a very low vibration level.
Customer benefit
- Engineered agitator of heavy-duty design
- Great energy savings thanks to high-efficiency hydraulics and accurate design system
- Smooth operation with very low vibrations
- Designed to withstand the local weather conditions with extremely low and high temperatures
- Quick and easy installation, safe operation, easy maintenance and service
"Sulzer’s prediction of the agitation level proved to be correct, and the two Scaba agitators save a significant amount of energy. The agitators are of heavy-duty design, and it is impressive to see these large units operate so smoothly with very low vibration levels."
Patrik Kolmodin, Product Line Manager Agitators, Sulzer
Product data
The Scaba agitators are engineered for heavy-duty operation at a high operating temperature. Their design comprises a rigid mechanical construction, strong bearing frame and an industrial Nord gearbox. The shaft is a solid 240 mm shaft made of carbon steel, with stainless steel lining. To withstand the great ambient temperature range, a gearbox with double heaters for extremely cold days and a cooler for hot conditions was selected.
The gas phase can be aggressive, and all in-tank parts above the surface were therefore made of 904L with additional rubber lining.
Scaba 240FVPT-Sff Table
Impellers | 2 x 3-bladed SHP1 propellers, diam. 2’500 mm |
Rotational speed | 20-46 rpm, max 53 rpm |
Gearbox | NORD SK11307AFK at 16 rpm |
Motor | ABB, used power 132 kW, installed 200 kW |
Seal | Stuffing box, grease lubricated |
Material of construction | Wetted parts in 316L, gas phase 904L + rubber lining |
Tank diameter | 7.3 m |
Tank height | 7.6 m |
Fluid | Melted sulphur at 130°C, 1.8 g/cm³ |
Purpose | Heat transfer |
Source: Sulzer Ltd.