Paint Manufacturer Cuts Maintenance and Cleaning Costs with Bredel Hose Pumps
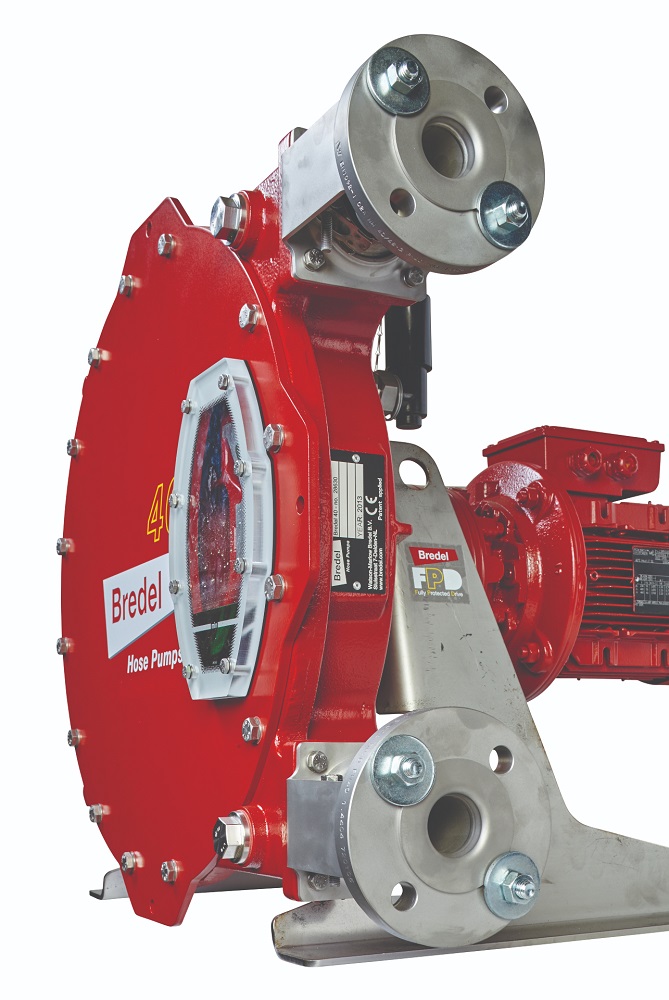
Paint manufacturer cuts maintenance and cleaning costs with Bredel hose pumps (Image source: Watson-Marlow Fluid Technology Group)
The company previously used progressive cavity pumps in the production of the paints, but the costs associated with cleaning, maintenance and repair were unacceptably high. Such was the success of the initial switch to Bredel hose pumps that the paint manufacturer now has eight Bredel 40 models.
During the Covid-19 pandemic, DIY home improvement projects increased hugely as people spent more time at home, driving a surge in demand for paint. To keep pace with production requirements, paint manufacturers had to rely extensively on their pumps, as any issues with reliability or efficiency could prove extremely costly.
Costly issues
The paint manufacturer in Germany previously used progressive cavity pumps, but maintenance and cleaning were ongoing issues. Even tiny traces of colour could spoil the next batch of paint. Additionally, the TiO2 (titanium dioxide) and pigment dyes are extremely abrasive and caused excessive wear to the PC pumps.
Unlike progressive cavity pumps, Bredel hose pumps have no moving parts that come into contact with the product. Instead, the pumped fluid is completely contained in a long-life hose, which is the only wear part and can be changed quickly and easily.
Cleaning costs are also far less. Not only are modern acrylic or latex-based paints easier to clean using just water, but Bredel pumps have no valves or seals to clog, while cleaning the hose is simple using sponge/foam balls (pigs).
Proven pump performance
At the German paint manufacturer, Bredel hose pumps transfer mixed paint to a filling station. Here, 10-20 litre containers await paint, which has a viscosity of about 5,000 mPas. Pump duty is intermittent, running for approximately 20 minutes to complete each batch depending on paint stock/order demand. The Bredel pumps operate at a flow rate of around 3,000 l/h and ensure there is no paint colour contamination.
Today, the plant has eight Bredel 40 pumps: four on duty and four on standby to ensure production continuity. This set-up using these highly repeatable pumps has been operating successfully for several years. The plant reports a significant reduction in maintenance and repair costs, with each Bredel pump demonstrating hose life in excess of one year. Furthermore, Bredel pumps feature no mechanical seals, again serving to reduce the maintenance budget.
Lower-flow solution
Recently, the paint manufacturer sought another pump for lower flow rates. Thanks to the success of the Bredel hose pumps on site, the plant’s engineering team once again approached WMFTG, this time selecting a 630UN/RE process/cased pump. The 630 pump is now in-situ transferring special and lower demand paints into smaller cans, typically 250-1000ml capacity.