New Triplex Process Diaphragm Pump for Various Applications
The G3M, a heavy-duty, medium-sized triplex drive unit, was originally developed to bring re-liquefied boil-off gases from LNG tankers to a high pressure level, rendering these gases usable for the ships propulsion system.
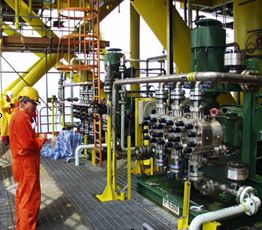
Like its sister model, the Lewa Triplex G3M is also suitable for use in the oil and gas industry, for example for injecting methanol or condensate (Picture: Lewa GmbH)
As a rugged workhorse, it is also ideal for various other applications, including use in the chemical industry or for offshore applications on oil platforms. The Lewa Triplex G3M process diaphragm pump will be one of the main exhibits of Lewa GmbH at Achema 2015. A technical animation demonstrating the synchronization of three Lewa Triplex process diaphragm pumps in various operating states will also be shown at the trade show.
The G3M is an intermediate size product in the Lewa portfolio that attains a maximum output of 200 kW thanks to its stroke length of 120 mm and a rod force of 125 kN. It is intended for use primarily in the oil and gas industry, as well as the chemical process industry. The chief application in the former sector is injecting monoethylene glycol and methanol. In the process industry, a wide variety of pumping tasks in pressure ranges between 40 and 750 bar can be managed. Other possible applications include handling highly flammable materials such as vinyl acetate, slurry in the wet oxidation or high-pressure metering of liquid ammonia.
Problem-free operation for more than 40,000 h
Just like the other models from the Triplex series, the G3M is equipped with an integrated—and thus particularly heavy-duty—worm gear. The monoblock drive element housing, on which the electric motor is flange-mounted via a coupling with flexible intermediate element, makes it possible to reduce the number of bearings and seals required to a minimum. This also makes the design highly compact. The optimal phase offset of the three pistons is ensured by a one-piece, solid and triple-throw crank shaft that requires only two roller bearings. To attain better damping of the swelling load, on the other hand, the bearings of the connecting rods are designed as slide bushings. The flow rate can be controlled using a frequency converter that regulates the change of the motor RPM, the number of strokes per minute and thus the flow rate. Because all components are designed for continuous duty, problem-free operation for more than 40,000 h is possible with the drive unit.
New pump head family for all common applications
To fit the G3M, which can manage a maximum pressure of 750 bar or a maximum flow rate of approximately 50 m³/h, Lewa is developing pump heads for every conceivable application. This development process relies on existing, proven technologies so that the pump can be adapted perfectly for use in the respective application situation. For example, even high-pressure applications will be possible with the M800 pump heads, because these heads on the G3M with PTFE diaphragm are designed for up to 750 bar.
Synchronization reduces pulsation and enables a flexible stand-by concept
Just like the other Triplex models before it, a synchronization of up to four of these pumps can be implemented for the G3M. A technical animation that illustrates the possibilities of this type of system will be shown at Achema. The basic goal of the harmonization is to reduce the pulsation of the pumped fluid and prevent vibrations in the pipelines that have the potential to damage the system. It is also useful to carry out a synchronization to prevent wear as much as possible on a system that is to be run for a very long period of time. Equal control without a master pump enables flexible implementation of the stand-by concept.
To implement an individual solution suitable for the respective application, the manufacturer not only needs to be familiar with the requirements for machine operation, but must also observe the machines peripheral equipment closely. In keeping with the complexity of the system and in an effort to eliminate resonance points from the outset, the pipelines must also be taken into account for the pulsation calculation, which is carried out on new systems in advance. This is used as the basis for developing a solution for the respective application. Requests for these types of redundant systems often come from the chemical industry, which strives to achieve quick, precise control in the handling of sensitive fluids.
Animation shows change in the different operating modes
The various operating states will be shown in the form of a diagram on a large monitor. In startup mode, each subsequent machine starts up once a specific rotational speed is reached so that the pumps start up one after the other in accordance with the requirements. In repair mode, a pump can be switched off while the other two pumps take over the preset flow rate. Another important application eliminates resonance points. In operating mode, the machine is run in a controlled manner in accordance with customer requirements.
Source: LEWA GmbH