New Progressing Cavity Pump Design Improves Sludge Transfer
The increase in urbanisation and environmental legislation in the UK suggests that the demands placed on municipal wastewater treatment companies are likely to increase. Pumps are an integral part of water and waste treatment systems, ...
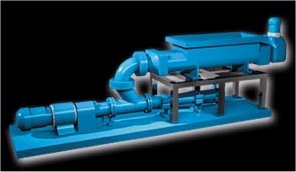
(Robbins & Myers).
... so the on-going development and improvement of progressing cavity pumps, the type of pump best suited to a wide range of water and waste treatment applications, is of prime importance.
Robbins & Myers, manufacturers of the Moyno progressing cavity pump range, outline their contribution in meeting the increasing demands placed upon wastewater treatment operators. For example, how pump engineers have spent years developing and enhancing the performance of progressing cavity pumps to better withstand the abrasive conditions found in wastewater treatment and sludge transfer applications.
Continuous improvements in research, design and manufacturing have resulted in new progressing cavity pumps products with extended capabilities. For example, Robbins & Myers recently introduced its 2000 HS System as an alternative to the more expensive piston pump and the higher maintenance open conveyor systems, typically used for dewatered sludge transfer in municipal wastewater treatment. The 2000 HS can handle a higher percentage of solids and pump it further than any other PC pumps based system. This new pump package incorporates a dual auger feed and advanced control system which boosts efficiency in handling semi-dry, high density solids, such as dewatered municipal sludge containing over 50% solids.
The 2000 HS System is designed to provide optimum performance for handling high solids filter cake applications thanks to some unique features. These include an ultra-feed® rotor configuration which is designed to improve the flow efficiency of high solids and content materials and ultra-shield® rotor coatings that help the pump to maintain peak performance and longevity, even under highly abrasive and corrosive service conditions.
The system features a non-pulsating flow, resulting in the elimination of pressure spikes caused by HDRPP systems while a twin screw feeder (TSF), located inside the suction hopper, supplies a constant, pressurised feed rate to the pump resulting in a 100% pump cavity fill rate. This feature also provides the flexibility of varying TSF length to match the wide feed areas from centrifuges, such as 1 metre, up to 3 metre length belt filter presses. The concentric rotation in a close tolerance pressure tube allows the TSF to generate positive stuffing pressure to the pump inlet, normally between 10 and 30 psi.
Additional features include a combination of dual augers that counter rotate to create a pull-down effect on the product and intermeshing augers that provide a self-cleaning action. This prevents the pumped product from sticking to the augers and ‘filling-in’ the flights. The completely vertical sidewalls also prevent the product from bridging. The system enables the TSF to operate at a separate rotational speed from the pump, allowing better control over the amount of stuffing pressure. Other developments also contribute to the overall improved pumping performance. For example, the optional slip injection system enhances the flow of sludge through the pipeline by allowing semi-dry, high solids material to be efficiently transferred within a closed piping system.
This enables an additive, such as polymer or water, to be injected into the flow path through injector rings positioned at pre-determined intervals immediately down-stream of the pump. When dispensed by a high-efficiency metering pump, the slip decreases the friction between the interior pipe wall and the pumped material resulting in a number of benefits. For example, additional reduction in discharge pressure, improved material transfer over distances up to 500ft, reduced energy consumption and the use of smaller pipe diameters and therefore, lower installation costs.
Of course, innovations in pump design only bring operational benefits if selected and applied effectively. The best pumping solution for any wastewater treatment application results from the combination of process knowledge, proven application experience and pump performance. When applied correctly, this combination ensures reliability, improved process efficiency and lower total cost of ownership.
The development of the Moyno 2000 HS System, coupled with extensive, field-proven application experience can provide improved performance and longevity, reduce maintenance downtime and lower total cost of ownership.
Source: NOV, Inc.