Lewa Begins Sales of Nikkiso Centrifugal Canned Motor Pump Models
Since July 2016, Lewa have been successively taking over the global sales of centrifugal canned pumps from its Japanese parent company, Nikkiso Co. Ltd. To even better meet the requirements of the European market, the reliable Nikkiso “Non-Seal” brand centrifugal canned motor pumps will be available from January 2019, also in accordance with DIN EN ISO 2858.
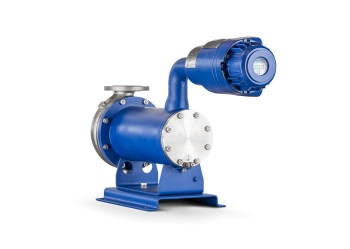
The encapsulated and entirely leak-proof design, which has the motor located inside the pressure-resistant stator casing, allows for the sealless pump design of the new models in accordance with DIN EN ISO 2858. (Image: Lewa)
As the first step, four sizes, the 25-160, 32-125, 40-200 and 50-200, will be introduced. Another four models will follow in February of 2019, while a total of 12 pump sizes will be available by the end of the 3rd quarter of 2019. The compact and low-vibration Nikkiso centrifugal canned motor pumps are used mainly for the transfer and circulation tasks of easily flammable, explosive or toxic fluids in the chemical and petrochemical industry. They therefore satisfy all the requirements of the ATEX Directive 2014/34/EU and are able to be customized. Furthermore, models in accordance with the API 685 standard are available.
“Thanks to over 60 years of experience in the manufacturing and further development of Non-Seal centrifugal canned motor pumps, Nikkiso Co., Ltd. is in the position to offer operators of chemical and petrochemical systems a reliable alternative to standard centrifugal pumps in order to safely convey easily flammable and toxic fluids,” reports Kazim Konus, Product Manager at Lewa. This is enabled by the encapsulated and completely leak-free construction of the pump, in which the motor is located inside the pressure-resistant stator housing, consisting of a stator lining and stator band. As a result, all models are designed without damage-prone mechanical seals, which minimizes both immediate as well as long-term hazard risks for employees as well as the environment.
Thanks to the special design of the pump, a part of the pumped medium is conveyed into the motor compartment and is used there for lubrication of bearings. Furthermore, it is simultaneously used for cooling the motor. “By manufacturing the installed slide bushings from a variety of materials, it becomes possible to adapt the pumps perfectly to the individual properties of the various media processed,” relates Konus. “The bearing material line-up ranges from carbon graphite to PTFE and silicon carbide to a mixed structure of carbon and silicon carbide that ensures exceptional protection against wear.”
Certifications for extreme operating conditions
To durably withstand the high stresses that exist in refineries of the chemical and petrochemical industries and to fulfill the requirements of the operator, all NIKKISO Non-Seal centrifugal canned motor pump models are certified in accordance with ATEX 2014/34/EU and can also be designed in accordance with API 685. “With the additional implementation of the requirements of DIN EN ISO 2858, we fulfill the demands of plant operators for standardized and easily interchangeable pumps. The new series enable the replacement of existing standard centrifugal pumps that have mechanical seals, in order to increase plant safety and the reliability of the unit without modifying the isometry of existing piping,” says Konus. The four models, which will be available on the European market beginning in January, feature a maximum drive output of 27.5 kW at a maximum flow rate of 80 m³/h and a maximum head of 90 m. In addition, the standard nominal outputs are also adhered to, with a specific head assigned to each of a variety of flow rates – taking into account the nominal diameter of the suction and discharge nozzles.
Monitoring of the pump bearings by E-monitor
All Non-Seal centrifugal canned motor pumps are equipped with the E-monitor, developed by NIKKISO, for the continuous improvement of operational safety and reliability. This is the most advanced monitoring system of its kind for pumps in high pressure and high temperature applications. “The bearing conditions of the NIKKISO Non-Seal pumps are checked by the E-monitor on an ongoing basis in order to detect deviations from normal conditions,” Konus says. “This takes place during operation through monitoring the radial and axial position of the rotor assembly by means of sensors integrated into the stator. In the event of increasing wear to the bearings, the appropriate sensors register these deviations and display the condition of the bearings via a display with traffic light colors.” Thus, wear can be detected early on and the necessary maintenance better planned. To further optimize monitoring, the E-monitor can be equipped with a remote function or an analog output signal that includes a remote display of the state of the bearings, including alerting and emergency shutdown. All models of centrifugal canned motor pumps are easy to install and service thanks to their modular design – neither spacer discs or clearance settings are necessary.
“With the introduction of the new models in accordance with DIN EN ISO 2858, we offer customers and operators a reliable and cost-efficient pump solution with a real added value in terms of the total cost of ownership for the system,” reflects Konus contentedly.
Source: LEWA GmbH