Freudenberg Sealing Technologies determines carbon footprint of seals
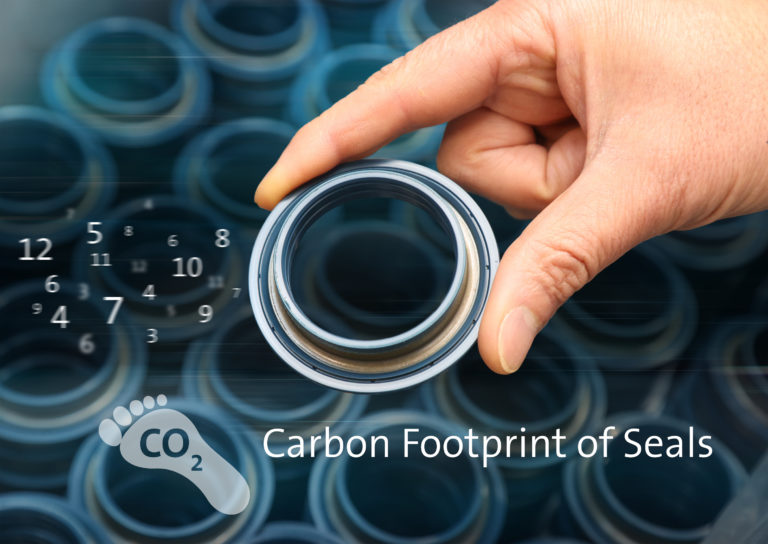
(Image source: Freudenberg Sealing Technologies GmbH & Co KG)
How many grams of CO2 are in a sealing ring? And by what means is it possible to minimize the greenhouse gas footprint from the production of components already during the design phase? Dr. Meike Rinnbauer and Volker Schroiff at Freudenberg Sealing Technologies want to provide knowledgeable answers to these questions. The project they have worked on in a team for the last two years aims to accurately determine the carbon footprint of Freudenberg products. The start of the project already yielded a fundamental insight: “Two factors have a significant impact on the emissions balance of a component,” Rinnbauer explains. The first factor is the selection of the material from which the seal is made and the second is the seal’s manufacturing process. Transport, on the other hand, was shown to have a substantially lower impact during analyses at the start of the project and is therefore negligible in the current assessment.
Freudenberg Sealing Technologies has developed its own “Green Index” to ascertain the greenhouse gas balance of materials. The background: Climate-relevant emissions are not the only environmental properties of chemical substances that should be considered in internal comparisons and evaluations of materials and processes. “For example, we try to avoid toxic precursors as much as possible to ensure our employees’ occupational safety and also take other environmental impacts into consideration,” Rinnbauer says. Since modern seals often consist of material compounds, all individual components are examined to avoid setting misguided incentives for the selection of certain materials.
To determine the global warming potential (GWP) of individual material components, Freudenberg Sealing Technologies uses an expert database that complies with the ISO 14044 standard for life cycle assessments. This process utilizes average, site independent GWP values for each individual substance, independently of its specific origin. In the future, however, it is expected that manufacturer- and site-specific parameters will be available along the entire supply chain. “This would also enable us to select future material suppliers not only on the basis of cost, quality and availability but also according to sustainability criteria,” says Rinnbauer. Then the sum of the GWPs weighted according to material proportions yields the entire GWP of a sealing material. At the same time, the harmfulness of individual material components is checked based on Freudenberg’s own occupational safety guidelines and the European REACH chemicals regulation. Depending on the harmfulness class, a penalty factor is assigned, which currently ranges from 1 (harmless) to 2 (persistent). The highest single value determines the factor that is multiplied by the total GWP. This ultimately results in a dimensionless value that can be used to assign the seal material to a specific sustainability class in the Green Index. Once they have been determined, all index values are stored in a materials database used throughout the company and are then available to the development engineers.
The effect resulting from the weighting process can be illustrated based on two fluoroelastomer materials (FKM), both of which are used for seals in the industrial sector. The first compound does not contain any harmful material components at all and has a greenhouse gas potential of 9.4 kilograms of CO2 per kilogram of material. The second compound has a lower greenhouse gas potential of only 8.0 kilograms of CO2 per kilogram of material, but it contains a hazardous material, which results in a classification as “not sustainable” in the Green Index. Since the lower sustainability is assigned a malus of 1.66, the first compound performs better in the overall assessment. However, an example of a polyolefin-based seal for fuel cells also shows that a material can be very sustainable even if it contains a persistent catalyst at a small proportion of 0.08 percent. Freudenberg Sealing Technologies has not yet made a final decision on how and to what extent sustainability factors should be considered beyond the GWP. “The important thing,” Rinnbauer says, “is that our optimization isn’t one-dimensional. When selecting materials, we also consider the service life and wear resistance that influence our customers’ eco-balance.”
Measured instead of estimated
Another thing is clear: The energy used to manufacture seals results in CO2 emissions, unless the energy supply to the production plants has already been fully converted to sources that are neutral regarding greenhouse gas. “The great challenge is to correctly allocate the CO2 emissions generated by energy that is supplied or created at a production site to individual material batches or products,” Schroiff explains. One prerequisite for this is knowledge backed up by measurements of how much energy is used in the individual process steps, specifically in relation to the weight, volume, or surface area. Based on the company’s core processes, a team at the Weinheim headquarters examined the specific energy consumption and other environmentally relevant parameters, such as the amount of technical or “engineered” waste consisting of partially or fully processed material. This kind of waste arises, for example, because products do not receive their final shape until they are finely machined in the production process. The four examined core processes include the mixing of the material, molding including vulcanization, coating, and reheating. In terms of material weight, the mixing proved to be similarly energy intensive as the molding and vulcanization. “But what surprised us in particular was that reheating consumes almost as much energy as the molding and vulcanization,” says Schroiff.
Sample products
In conclusion, the Freudenberg team transferred the results to two sample products, a Simmerring made of fluoroelastomers (FKM) as used in the automotive industry and general mechanical engineering, and a housing part made of polyamide 6.6 with a functional coating for electromagnetic shielding. This revealed significant differences: For the Simmerring, the molding and vulcanization account for about half of the total production-related energy consumption. It is possible to reduce the CO2 emissions by a third overall using an optimized molding process that does not require post-processing. For the housing part, the production of the plastic material accounts for a significantly higher proportion of around 40 percent of the energy input, while the coating accounts for about one-tenth. In the production of polyamide components, too, the material and possibly the technical waste account for a significant proportion of the total emissions.
Even if many materials and processes still need to be studied in more detail before transferring the methodology, a clear tendency is evident: “The greatest leverage for manufacturing components in a more climate-friendly way lies in avoiding waste during the production, at least as long as we are still using fossil energy,” Schroiff explains. Therefore, Freudenberg Sealing Technologies is resolutely focusing on waste-preventing production technology. By using cold runner injection molding with valve gate technology alone, the company already eliminates around 70 tons of waste per year and emits 600 tons less CO2.
Source: Freudenberg FST GmbH