Patented Sealing Solution to Improve Drinking Water
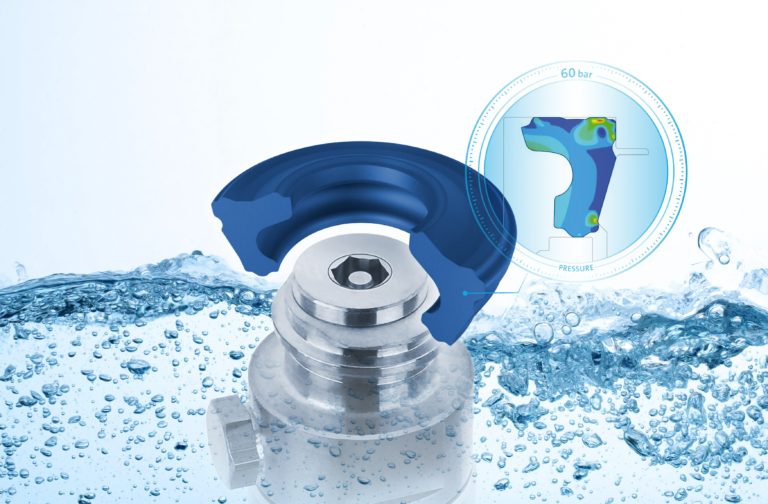
High-performance polyurethane seal from Freudenberg Sealing Technologies combines positive characteristics. (Image source: Freudenberg FST GmbH)
Drinking water is heavily contaminated in many countries around the world: Pollutants such as microplastics, bacteria, viruses and pesticides can negatively impact the quality of the water. Freudenberg Sealing Technologies developed an innovative sealing solution for a water treatment device that not only filters tap water but also enriches it with minerals, trace elements and, if desired, carbonic acid.
When the device was first developed, the customer faced a technical challenge: The valves of conventional carbon dioxide cartridges are not fully standardized and have many different dimensions that connect at varying heights. Ensuring that all valve variants fit together flawlessly with the appliance requires a seal with a sophisticated design that provides reliable sealing regardless of this high tolerance range.
“After the customer contacted us, we began an analysis of the special conditions that such a seal has to meet,” said Ulrich Wüstenhagen, Pneumatics Product Development at Freudenberg Sealing Technologies. “It quickly became clear that this project required our materials expertise as well as our development know-how and our experience in manufacturing such products.”
Amazing sealing performance
The valves of carbon dioxide cartridges are screwed into water purifiers with a standardized trapezoidal thread. Then the cartridge and appliance are firmly connected to each other. Next, a pressure reducer on the appliance lowers the cartridge pressure from 60 bar to a permanent working pressure of around three bar. The seal in the gap between the pressure reducer on the appliance and the valve of the gas cartridge must now accomplish something extraordinary: Since it is exposed to the pressure of 60 bar for a long time, carbon dioxide penetrates the material until the saturation point. When the water purifier is used, the pressure quickly decreases, and the gas abruptly expands. During this rapid decompression, the gas in the material escapes back out of the material. This is no problem when the seal is produced from the right kind of material. But if the material has imperfections in which the CO2 can accumulate, or if it is categorically unsuitable, the expansion will create bubbles that damage the seal.
In addition to the right material, the seal must also have the right geometry to handle these tough conditions. It must both compensate for the various connection dimensions of the valves on the gas cartridges and make it easy for users to change the cartridges. Here a clever combination of material and geometry ensures the lowest possible frictional torque as the cartridge is twisted in or out.
Optimal in design and material
The customer was working on a tight deadline that did not offer much time for extensive testing. By relying on its existing material expertise and manufacturing know-how, Freudenberg Sealing Technologies began working in close cooperation with the appliance manufacturer, and the optimal sealing solution and perfect material were identified. The company’s high-performance polyurethane ,93 AU V167, is resilient and has excellent tensile strength in addition to high elongation at break. It is very elastic, wear-resistant and approved for food contact pursuant to European Union Regulation 10/2011. It also complies with FDA requirements and 3-A sanitary standards.
The company’s rapid seal service, Freudenberg Xpress supplied the first CNC-machined prototypes and then took over the production of two preliminary series, each with about 1,000 CNC-machined seals. The next step called for the expertise of specialists at Freudenberg Sealing Technologies for the production and sampling of an injection molding tool, which is now being used to supply the series parts – economically and ready for use.
“Thanks to a very pragmatic approach, we arrived at a tailor-made solution with our customer in a short time – a solution we have now patented,” Wüstenhagen concludes. “This seal ensures that, in the future, tap water can be enjoyed confidently anywhere in the world.”
Source: Freudenberg FST GmbH