Freudenberg Sealing Technologies bestimmt CO2-Fußabdruck von Dichtungen
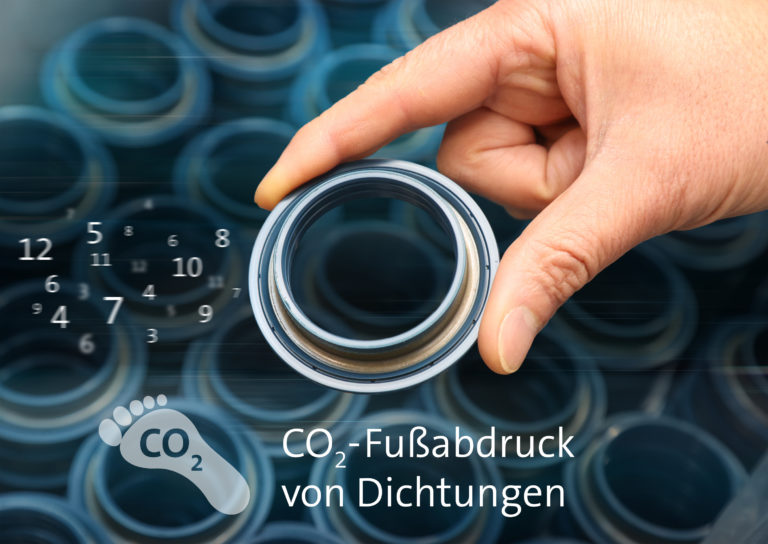
(Bildquelle: Freudenberg Sealing Technologies GmbH & Co KG)
Wieviel Gramm CO2 stecken in einem Dichtungsring? Und wie kann die Treibhausgasbilanz aus der Produktion eines Bauteils bereits in der Konstruktionsphase minimiert werden? Diese Fragen seriös beantworten wollen Dr. Meike Rinnbauer und Volker Schroiff bei Freudenberg Sealing Technologies. Seit zwei Jahren arbeiten sie mit einem Team an einem Projekt, das es erlauben soll, den CO2-Fußabdruck der Freudenberg-Produkte genau zu bestimmen. Eine grundsätzliche Erkenntnis entstand bereits am Anfang des Projekts: „Es sind zwei Faktoren, die die Emissionsbilanz eines Bauteils wesentlich beeinflussen“, erläutert Rinnbauer. Der erste Faktor besteht in der Auswahl des Materials, aus dem die Dichtung gefertigt wird, der zweite im Herstellprozess der Dichtung. Der Einfluss des Transports hingegen ist, das zeigten Analysen zu Beginn des Projekts, um Größenordnungen geringer und daher in der aktuellen Bewertung zu vernachlässigen.
Um die Treibhausgas-Bilanz von Werkstoffen zu erstellen, hat Freudenberg Sealing Technologies einen eigenen „Green Index“ entwickelt. Der Hintergrund: Neben den klimarelevanten Emissionen sollen auch andere Umwelteigenschaften chemischer Stoffe berücksichtigt werden, um intern Materialien und Prozesse vergleichen und bewerten zu können. „So versuchen wir, giftige Vorprodukte so weit als möglich zu vermeiden, um die Arbeitssicherheit unserer Mitarbeitenden zu gewährleisten und auch andere Umwelteinflüsse zu berücksichtigen“, sagt Rinnbauer. Da moderne Dichtungen oft aus Materialmischungen bestehen, werden alle Einzelkomponenten berücksichtigt, um keine Fehlanreize für die Auswahl bestimmter Materialien zu setzen.
Um das Treibhausgaspotenzial (Global warming potential, GWP) einzelner Materialkomponenten zu bestimmen, nutzt Freudenberg Sealing Technologies eine Expertendatenbank, die der ISO-Norm 14044 für Ökobilanzen gerecht wird. Dabei werden mittlere, standort-unabhängige GWP-Werte für jeden einzelnen Stoff genutzt, also unabhängig von der konkreten Herkunft. Perspektivisch ist aber zu erwarten, dass hersteller- und standortspezifische Kennwerte entlang der gesamten Lieferkette zur Verfügung stehen. „Das würde uns auch erlauben, Materiallieferanten zukünftig nicht nur anhand von Kosten, Qualität und Verfügbarkeit, sondern auch unter Nachhaltigkeitskriterien auszuwählen“, sagt Rinnbauer. Die Summe der nach Materialanteilen gewichteten GWPs ergibt dann den gesamten GWP eines Dichtungsmaterials. Parallel erfolgt die Überprüfung der Schädlichkeit einzelnen Materialkomponenten anhand Freudenberg-eigener Arbeitsschutzrichtlinien sowie der europäischen REACH-Chemikalienverordnung. Je nach Schädlichkeitsklasse wird ein Malusfaktor vergeben, der aktuell von 1 (unschädlich) bis 2 (persistent) reicht. Der schlechteste Einzelwert bestimmt den Faktor, der mit dem gesamten GWP multipliziert wird. Letztendlich ergibt sich ein dimensionsloser Wert, mit dem der Dichtungswerkstoff einer bestimmten Nachhaltigkeitsklasse des Green Index zugeordnet werden kann. Alle einmal bestimmten Index-Werte werden in einer unternehmensweit genutzten Werkstoffdatenbank hinterlegt und stehen damit den Entwicklungsingenieuren zur Verfügung.
Der Effekt, der sich aus dem Gewichtungsverfahren ergibt, lässt sich anhand zweier Fluorkautschukmaterialien (FKM) darstellen, die beide für Dichtungen im Industriebereich eingesetzt werden. So kommt die erste Mischung völlig ohne schädliche Materialkomponenten aus und weist ein Treibhausgaspotential von 9,4 Kilo CO2 pro Kilo Material aus. Bei der zweiten Mischung ergibt sich hingegen ein Wert von 8,0 Kilo CO2 pro Kilo Material, dafür enthält die Mischung jedoch einen Gefahrstoff, was im Green Index zu einer Einstufung als „nicht nachhaltig“ führt. Da die geringere Nachhaltigkeit mit einem Malus von 1,66 berücksichtigt wird, schneidet die erste Mischung in der Gesamtbilanz besser ab. Ein Beispiel einer Polyolefin-basierten Abdichtung für Brennstoffzellen zeigt aber auch, dass ein Material auch dann sehr nachhaltig sein kann, wenn es mit einem geringen Anteil von 0,08 Prozent einen persistenten Katalysator enthält. Wie und in welchem Umfang über das GWP hinaus Nachhaltigkeitsfaktoren berücksichtigt werden sollen, ist auch bei Freudenberg Sealing Technologies nicht endgültig entschieden. „Wichtig ist“, so Rinnbauer, „dass wir nicht eindimensional optimieren. So berücksichtigen wir bei der Materialauswahl auch Lebensdauer und Verschleißbeständigkeit, die die Ökobilanz unserer Kunden beeinflussen.“
Gemessen statt geschätzt
Klar ist auch: Die Energie, die für die Herstellung von Dichtungen aufgebracht wird, führt zu CO2-Emissionen, sofern die Energieversorgung der Produktionswerke nicht bereits vollständig auf Treibhausgas-neutrale Quellen umgestellt wurde. „Die große Herausforderung besteht darin, die CO2-Emissionen, die durch den Energiebezug oder auch Eigenerzeugung an einem Produktionsstandort anfallen, korrekt auf einzelne Materialchargen oder Produkte umzulegen“, erklärt Schroiff. Eine Voraussetzung dafür ist durch Messungen abgesichertes Wissen darüber, wieviel Energie in einzelnen Prozessschritten spezifisch, also auf das Gewicht, das Volumen oder die Oberfläche bezogen, tatsächlich verbraucht wird. Anhand von Kernprozessen des Unternehmens untersuchte ein Team am Stammsitz in Weinheim den spezifischen Energieverbrauch sowie weitere umweltrelevante Parameter wie die Menge an technischen Abfällen, auch „Engineered Waste“ genannt, die aus teilweise oder ganz verarbeitetem Material bestehen. Solche Abfälle entstehen beispielsweise, weil Produkte durch Feinbearbeitung erst im Lauf des Produktionsprozesses ihre endgültige Form erhalten. Die vier untersuchten Kernprozesse umfassen das Mischen des Materials, die Formgebung einschließlich der Vulkanisation, die Beschichtung sowie das Nachheizen. Auf das Materialgewicht bezogen erwies sich das Mischen in etwa so energieintensiv wie Formgebung und Vulkanisation. „Besonders überrascht hat uns aber, dass das Nachheizen fast so viel Energie verbraucht wie Formgebung und Vulkanisation“, sagt Schroiff.
Musterprodukte
Abschließend übertrug das Freudenberg-Team die Ergebnisse auf zwei Musterprodukte, einen Simmerring aus Fluorkautschuk (FKM), wie er in Automobilindustrie und im allgemeinen Maschinenbau verwendet wird, sowie ein Gehäuseteil aus Polyamid 6.6, das mit einer Funktionsbeschichtung für elektromagnetische Abschirmung versehen ist. Dabei zeigten sich deutliche Unterschiede: Bei dem Simmerring verursachen Formgebung und Vulkanisation rund die Hälfte des gesamten fertigungsbedingten Energieaufwands. Die CO2-Emissionen können insgesamt um ein Drittel verringert werden, wenn ein optimiertes Formgebungsverfahren verwendet wird, das ohne Nachbearbeitung auskommt. Bei dem Gehäuseteil hat die Herstellung des Kunststoff-Materials einen deutlich höheren Anteil von rund 40 Prozent am Energieaufwand, rund ein Zehntel entfällt auf die Beschichtung. Auch in der Herstellung von Polyamid-Bauteilen entfällt ein wesentlicher Anteil der Gesamtemission auf das Material und eventuell die technischen Abfälle.
Auch wenn für eine Übertragung der Methodik noch viele Materialien und Prozesse detaillierter untersucht werden müssen, zeigt sich eine klare Tendenz: „In der Abfallvermeidung während der Produktion liegt der größte Hebel, um Bauteile klimafreundlicher herzustellen, solange wir zumindest noch fossile Energie nutzen“, erläutert Schroiff. Bereits heute setzt Freudenberg Sealing Technologies daher konsequent auf abfallvermeidende Produktionstechnik. Allein durch den Einsatz des Kaltkanal-Spritzgusses mit Nadelverschluss spart das Unternehmen bereits jährlich rund 70 Tonnen Abfall und emittiert 600 Tonnen weniger CO2.
Quelle: Freudenberg FST GmbH