Filling of Semi-Solids in Disposable Syringes
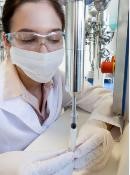
For semi-automatic processes such as this benchtop solution, the simple handling is a positive aspect for the operator.
Nevertheless, absolute precision filling of the syringe is a must. Conventional filling technologies in the pharmaceutical industry often reach their limits when it comes to semi-solid products.
ViscoTec has set itself the task of being able to fill a wide variety of products with just one dosing system. From watery to highly viscous, shear sensitive, abrasive, aggressive or toxic. This includes all viscous pharmaceutical or medical technology products and so-called semi-solids with or without highly effective substances: i.e. dermal fillers such as hyaluronic acid or depot medication drugs made of liposomes, filled with abrasive solids such as hydroxyapatite or shear-sensitive active ingredient crystals.
Flexible but high-precision filling of syringes
The ViscoTec endless piston principle enables a precise, gentle, and pulsation-free product flow. The dispensers have a flow rate of 0.2 to 700 ml / min and are flexible to fill Luer Lock or Luer Slip syringes, for example, from 0.2 ml to 50 ml with a filling accuracy of +/- 1 %. The net dosing time can be less than one second per syringe. A possible overfilling, but also underfilling, especially with self-medication of standard syringes, is therefore eliminated.
Even filling of small and very small batches with frequent product changes are possible thanks to the easy cleanability of the GMP-compliant Hygienic Dispensers. Cleaning is performed either by COP (Cleaning out of Place) or CIP (Cleaning in Place). Components in contact with the product can be autoclaved.
The special design of the filling pumps enables a programmable suck-back, which in turn ensures a defined thread break and therefore prevents unwanted dripping or thread pulling. This is done by the change of rotation direction in the dispenser, whereby the material is sucked-back into the dosing needle in a defined manner. The suck-back function can also be used for materials with difficult thread breakage. Dosing quantity, speed and acceleration can be individually adjusted according to the requirements of the product. The viscosity does not affect the dosing performance.
Another advantage of the volumetric filling pump is the absolute gentle handling of shear-sensitive or abrasive materials. There is no compression of the conveyed product during the filling process.
Changes to the fill quantity, due to a change in the container size, can be made without mechanical modification. This is ensured by the linear relationship between the quantity dosed and the servo revolution. Thanks to the compact design of the Hygienic Dispensers, they can be easily integrated into existing or newly designed fully automatic packaging systems. There are no limits as to the alignment of the dispensers. And in semi-automatic processes, the simple handling for the operator is a positive aspect - ideal for small batches or clinical trials.
Different filling processes depending on the application
The filling process can be performed either via the stopper or via the syringe cone. When filling via the stopper, this is done by means of a Z-movement of the container or the filling needle in order to ensure a mirror filling. To avoid air pockets, the syringe can be placed under vacuum during filling. In this way, additional so-called "head spaces" can be avoided, which are known from conventional filling.
If the filling process is implemented via the syringe cone, a special needle or Luer connection is used for connection. This is possible thanks to the high-pressure stability of ViscoTec dosing systems. An advantage of this type of filling is that the "piston" can already be mounted in the syringe. During filling, this is then pushed backwards by the inflowing fluid. Subsequent placing of the piston under vacuum is no longer necessary.