ATEX Certification for Energy-efficient NeoMag Pump
There are many different areas of application for the NeoMag pump from DST Dauermagnet-SystemTechnik GmbH. As a result of ATEX certification, the centrifugal pump with the Borohardcan silicon glass separating can has now also become the standard energy-efficient chemical pump, and can therefore be employed in potentially explosive areas. In addition, with an energy-saving of up to 30 percent, the NeoMag is very impressive.
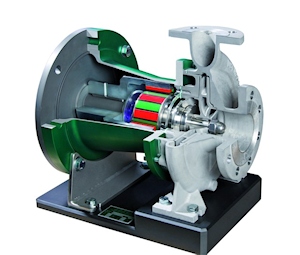
NeoMag Pump (Image: DST)
The NeoMag is a single-stage, non-self-priming, stainless steel centrifugal pump in block design. Its centre-piece is the Borohardcan, a canister made from borosilicate glass - a patented innovation from DST. This brings the NeoMag into a new economical, energy-saving dimension. There is no heat development due to eddy currents. The Borohardcan is thereby, in itself, a particularly economical solution for magnetically coupled standard centrifugal pumps. The pump impeller and the housing components of the NeoMag have been developed and designed according to the latest expertise with regard to flow technology and hydraulics.
Through the employment of the new patented permanent magnetic coupling with Borohardcan canister and a compact plain bearing mounting made from silicon carbide (SSIC), one can assume a maintenance-free running time of circa five years and more for the NeoMag.
Comparing a normal magnetic centrifugal pump with conventional magnetic drive and the new NeoMag pump, with a delivery rate of 60 m³/h and a delivery height of 60m, and using the DST patented Borohardcan separating can, a power saving of up to 3.5 kW can be achieved. With a power requirement of 18.5 kW, on a pump which is in operation 24 hours a day for the whole year, as a result of the improved magnetic coupling the energy saved is 30,660 kWh, which is a saving of €3,066 at a price of 0.10€/kWh. If an energy-efficient IE2 motor is employed, for the NeoMag pump unit there is a further energy saving of up to 11 percent compared with conventional drive solutions. In the example calculation this means a saving of a further 14,454 kWh and thus €1,445.40.
A centrifugal pump with double-acting mechanical seals and the NeoMag is at more or less the same price point. With a running time of five years - depending on the media being pumped - the customer saves five to ten maintenance intervals for the mechanical seals.
The NeoMag can be obtained in the pressure ranges PN10 and PN16 for a delivery rate up to 60m³/h and for delivery height of up to 60m. The series will be extended further to smaller design sizes on the first bearing bracket. A permanent magnetic coupling with a new magnet configuration specially developed for employment in the NeoMag is suitable for media temperatures up to 150°C. A magnet assembly for employment up to 350°C is possible on request.
Areas of Application
- Chemical industry (aggressive, in part toxic media)
- General process engineering (services, tempering)
- General industrial applications (delivery of water, watery media and oils)
- Pharmaceutical industry (service media)
- Biotechnology (service media)
- Foodstuffs industry (service media)
- Petrochemistry (ancillary processes)
IPV Varisco Dresden, a specialist in self-priming centrifugal pumps, has worked successfully with the NeoMag s mounting and permanent magnetic coupling for several years. Measurements have shown that the company, through the employment of the new technology, has used up to 50% less electricity.The NeoMag consists essentially of three components, the housing, the mounting and the permanent magnetic coupling. After just 15 minutes test run, the housing shows a characteristic curve with an optimum efficiency due to the hydraulic and flow technology design. With the NeoMag 50-200 this is at 73 percent. Permanent magnetic couplings have been designed and manufactured by DST for over 20 years for new applications and customer-specific solutions. The company is market leader in this technology. As far as the SSIC mounting is concerned, DST has more than a decade s experience to fall back on.