Understanding the Multiple Functions of Pulsation Dampeners/Surge Suppressors
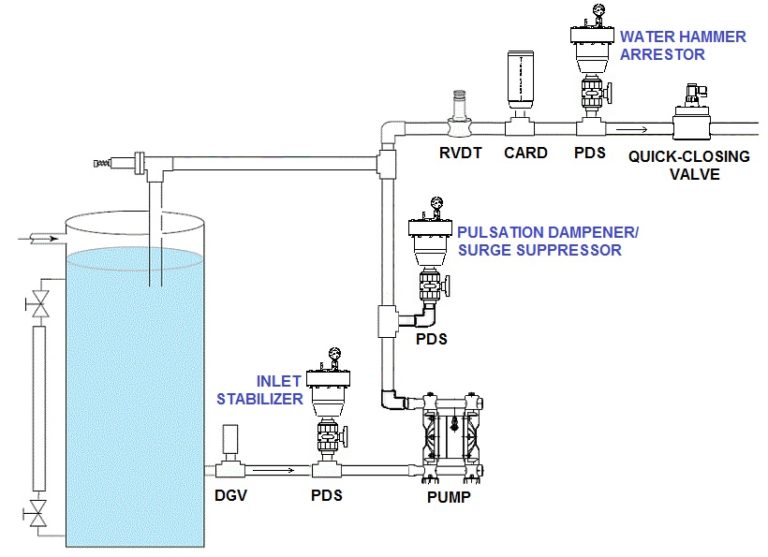
One Pressure Vessel Wears Many Hats. (Image source: Plast-O-Matic Valves, Inc.)
When used properly, quick pulsating flows will be greatly reduced preventing the following flow control problems:
- Prevents Fatigue of all Pipes and Inline Equipment.
- Ruptured Piping, Gaskets and Seals
- Leaking and Weakened Connections
- Pipe Vibration and Noise
- Damaged Valves and Filters
- Damaged Pressure Regulators and Gages
- Loosened Pipe Hangers and Supports
- Premature Failure of other Equipment and Devices
- Prevents Splashing and Foaming of Fluids
Pulsation dampening provides the added benefit of smoothing the output supplied by many types of pumps, especially double diaphragm pumps and metering pumps. This provides a steady, uninterrupted supply to points of use, which will greatly enhance system productivity, prolong pump life, and prevent splashing and foaming.
Water Hammer Arrestor When used properly, water hammer will be greatly reduced to just a few percentage points of the spike that the system would have without using the PDS. This helps prevent the following flow control problems, as per the Plumbing and Drainage Institute Standard PDI-WH 201:
- Ruptured Piping
- Leaking Connections
- Weakened Connections
- Pipe Vibration and Noise
- Damaged Valves
- Damaged Check Valves
- Damaged Water Meters
- Damaged Pressure Regulators and Gages
- Damaged Recording Apparatus
- Loosened Pipe Hangers and Supports
- Ruptured Tanks and Water Heaters
- Damaged filters
- Premature Failure of other Equipment and Devices
Inlet Stabilizer AKA “Suction” Stabilizer — Installed as close as possible to the pump inlet, the PDS will take in liquid when the system is pressurized. If the dome is properly charged with compressed air, the PDS will expel the liquid back into the pipeline when the pump draws liquid and pressure drops. This repeated action ensures a continuous supply of liquid to the pump, reducing strain on the pump and greatly improving pump efficiency.
Used in combination with a PDS on the discharge, in most cases the pump will supply a smooth, steady flow at a constant pressure and prevent the following pump related problems:
- Cavitation and “starvation”
- High frequency pressure waves
- Incomplete filling of pump chambers
- Uneven flow and pressure
- Pump friction and overheating
- Pump damage and premature failure
Accumulator As with the inlet stabilizer function above, the PDS will take in liquid when the system is pressurized. If the dome is properly charged with compressed air, the PDS will expel the liquid back into the pipeline when pressure drops. This cycle is automatic, or the liquid and line pressure can be retained and released as needed simply by using a blocking valve between the PDS and the piping tee. The accumulated liquid and pressure could be held for unexpected power outtages or other system failures, and then used to complete a cycle, retained for backflush during scheduled maintenance, or any other requirements when the regular process is off or interrupted. When the intended use of the PDS is solely as an accumulator, the blocking valve need not be a full port design.
Thermal Expansion Tank Liquid temperature generally increases in a flowing condition. It can also increase due to processes or external factors that transfer heat to the media. When temperature increases and liquid — which is non-compressible — expands in a closed system, the results can be catastrophic. The PDS can be used as a simple expansion tank in many applications where anticipated expansion would be less than the stated capacity of the unit.
Important Safety Note: Please be aware that a Pulsation Dampener is designed to operate as a pressurized vessel. Proper precaution should be taken to ensure safe installation and operation; read the installation instructions carefully prior to use. The unit should be charged with regulated compressed air or nitrogen only. Oxygen must not be used. The gauge isolation valve should be closed prior to opening the system connection valve.
Source: Plast-O-Matic Valves, Inc.