Technical Paper Shows How to Cut Energy Use in Papermaking Industry
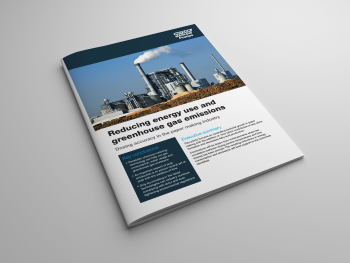
WMFTG technical paper shows how to cut energy use in papermaking industry (Image source: Watson-Marlow Fluid Technology Group)
The paper drying section consumes most of the energy in the manufacturing process, and contributes 68 percent of the total greenhouse gas emissions for the sector. However, better performance at the dewatering stage delivers the potential for less water to be heated and evaporated in the drying section.
To enhance dewatering, additives are used to increase drainage of the paper fibres, while the calcium carbonate content of the raw material also has a significant influence on dewatering.
As set out in the technical paper, comprehensive trials to corroborate this thinking took place at the Netherlands research facility of Huhtamaki OY, a Finnish multi-national and global leader in moulded-fibre technology for food and drink packaging.
Full details of the trial can be found in the technical paper, suffice to say that adding lime at the wet end of the process was shown to provide a number of significant benefits.
The trade-off for any paper mill looking to adopt this strategy, however, is that lime is challenging to work with, as it tends to settle, forming lumps in suspension. Diaphragm pumps are often used to add lime, although difficulties are frequently encountered as ancillary foot valves tend to get blocked by lime dispersion.
For the trials at Huhtamaki, a Qdos 120 peristaltic chemical metering pump from Watson-Marlow Fluid Technology Group was used to deliver the lime prior to dewatering the paper pulp. Qdos pumps deliver accurate flow, despite changing process conditions, and do not require additional ancillaries like inlet and pressure-holding valves.
By accurately metering lime to the pulp, Huhtamaki succeeded in lowering the average oven temperature over the course of the trial. A lowering in oven temperature of 15C correlates to a 3 percent reduction in energy consumption and, consequently, a 3 percent reduction in greenhouse gas emissions. At Huhtamaki, such was the size of the gains achieved that payback on the Qdos pump was achieved in just four weeks.