Sulzer Secures Flexible Thermal Power Generation with Pump Retrofits
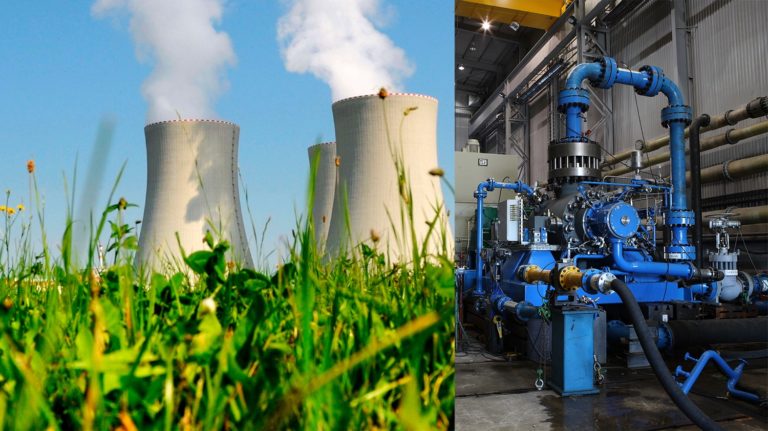
Sulzer’s dynamic, bespoke pump retrofit service means that the operational needs of any thermal power plant can be met optimally and cost-effectively. (Image source: Sulzer Ltd.)
This change in operational strategy can adversely affect the efficiency and reliability of equipment such as boiler in-feed pumps. Operators of these power plants should analyze the changes and assess how their equipment needs to be adjusted to respond to the increase in renewable energy.
Changing requirements of a sustainable future
Electricity demand in Asia is growing by around 6% annually. Renewable energy is at the forefront of this, with the Association of Southeast Asian Nations stating that it wants to source 23% of its power from renewables by 2025, up from 9% in 2019. With this transition, Asia’s energy grid is diversifying. However, the fluctuating electricity output from renewable energy sources means that thermal power plants are still having to cover any shortfalls in the grid.
Smoothing out these fluctuations in renewable energy supply means pushing equipment at thermal power stations beyond their initial design remit: baseload operations. Working at variable loads can damage equipment and cause energy losses.
With renewable energy not entirely dependable for the power requirements of billions across Asia currently, thermal power plants will be part of the energy ecosystem for a long time to come. If these facilities cannot adapt, the road to a sustainable future looks anything but smooth. Luckily for operators, there are proven solutions available.
The risks of overlooking pumps
Boiler in-feed pumps are a critical element of a thermal power plant, supplying the water that eventually drives the steam turbines. Flexible operation poses risks to existing boiler feed pumps, increasing the probability of wear and energy losses. This equipment can be neglected when adapting facilities for new operations, with plant managers usually prioritizing turbine improvements instead. However, this can be a false economy.
For example, at a thermal power plant meeting fluctuating load, repeated stops and starts can cause damage to a boiler feed pump’s shaft, thrust disk, impellers, and diffusers. Low flow cavitation at the suction impeller and corrosion in high flow velocity areas of the casing are additional risks. If this causes pump downtime, power generation can be adversely affected - a situation operators cannot afford.
As a global pump original equipment manufacturer (OEM) and worldwide independent service provider (ISP) with nearly two centuries of engineering heritage and experience in the power industry – Sulzer is well placed to support power plant in overcoming the challenges of meeting fluctuating loads.
Tailored services for individual power plants
The first step recommended by Sulzer is a thorough pump energy audit. By assessing pump reliability, maintenance, temperature and vibration data – operators are able to identify the root cause of issues well ahead of any potential failure.
Next, Sulzer can deliver the retrofit services to enhance any pump from any brand, as part of its recently launched OEM-X line service. Even if pumps are nearing 30 years old, solutions are ready to give this equipment a new lease of life, improving efficiency and output power capacity.
Pump re-rates, including de-staging and new hydraulics, help to meet new duty points. Material and design upgrades can enhance durability and reliability in fluctuating load operations. Variable speed systems can deliver quantifiable energy savings. All work is backed by in-house reverse engineering, parts production, precision machining, 3D scanning and additive manufacturing.
A global network of more than 100 service centers provides responsive local engineering support, along with teams of dedicated, highly experienced field engineers. This ensures that power plants benefit from expert pump knowledge and services on-site too.
Smoothing the energy transition
Sulzer’s dynamic, bespoke pump retrofit service means that the operational needs of any thermal power plant can be met optimally and cost-effectively. By carrying out such a project along with turbine improvements, not only can plant managers efficiently support energy supply fluctuations to safeguard output and profits, but they can also lower CO2 emissions and reduce carbon taxes too.
Continuous investment in Sulzer’s pump engineering research and development facilities helps power plants across the globe to become leaders in pump reliability and efficiency. To date, Sulzer has retrofitted hundreds of boiler feed pumps worldwide.
As more renewable energy integrates into the grid systems in Asia, load fluctuations for thermal power plants will continue to become more frequent. By partnering with Sulzer, operators can ensure that their pumps operate efficiently, reliably and profitably, while adapting to grid changes and contributing to energy security and a more sustainable energy future.
Source: Sulzer Ltd.