Sulzer Pump Retrofit Secures Flare Knockout Pump Reliability
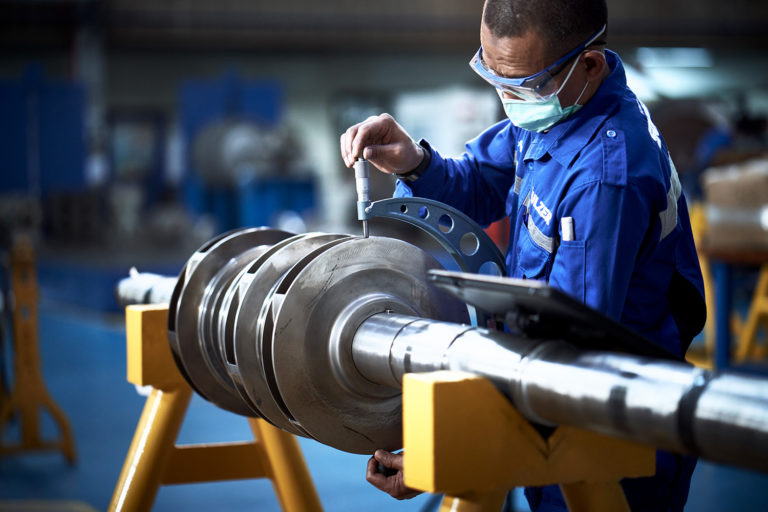
Pump downtime was minimized, with Sulzer completing each pump retrofit individually to keep operations running (Image source: Sulzer Ltd.)
Reliability issues flaring up
Flare knockout pumps are an essential component of offshore platforms. Gas or liquid from the process stream that cannot be recovered or recycled requires a release to avoid pressure build-up, so the flare system safely vents these. The excess is transported via a pump to a flare knockout vessel before combustion. A critical safety element, any pump failure in the flare system results in a total platform shutdown, stopping extraction and halting productivity.
It was exactly these pump failures the operator was experiencing at its platform operating offshore in east Malaysia. The two double casing diffuser vertically suspended pumps had operated reliably for several years, until a change in process caused abrasive sand to be drawn into them. Operating with a flow rate of 32 m3/hr at a head of 163.9 m, the pumps had a short MTBF, with failures typically occurring every 12-18 months. Excessive vibrations during running were causing the pumps to trip, with the resulting low performance not meeting the platform’s demand. In the worst-case scenario, a double pump failure would result in a complete shutdown of operations, costing the operator millions of dollars.
Shrewd project delivery
The operator approached Sulzer for a solution due to its reputation as a global pump original equipment manufacturer (OEM) and leading service provider to the oil and gas industry. After a tour of Sulzer’s Singapore Service Center and a presentation on its extensive pump retrofit capabilities, the IOC selected the company to complete the work. Sulzer in Belgium was also ready to assist, ensuring that the two international teams collaborate and complete the project efficiently.
A retrofit was selected over supplying new units due to the time advantages, as Sulzer could guarantee a retrofit lead time of 26 weeks. This included manufacturing retrofit parts, carrying out modifications and conducting a performance assurance test at the Singapore Service Center. Pump downtime was minimized, with Sulzer completing each pump retrofit individually to keep operations running. Sulzer could also carry out all modifications within the existing pump footprint, ensuring easy reinstallation into the surrounding infrastructure and preserving available space on the platform.
Toughening up
Upon receiving the pump at the service center, Sulzer dismantled it and carried out a thorough inspection. It was quite clear that the pumps had experienced excessive wear. First, there were signs of erosion on the impellers and diffuser bowls, as well as running marks and wear on bushings, shaft sleeves and wear rings. Moving further along, blistering and running marks were found on the mechanical seals and O-ring locations, with marks on the seal’s drive collar too. During previous maintenance work, the bearings had been installed incorrectly. With access to the OEM drawings, Sulzer could ensure the correct orientation. Finally, skidding marks were also discovered on the bearing seating area.
To combat the wear on the impellers, diffusor bowls, sleeves and wear rings, Sulzer applied an exceptionally durable tungsten carbide coating to these components using a high velocity oxygen fuel (HVOF) thermal spray process so they could resist the debilitating effects of the abrasive process liquid. Each impeller was individually balanced, then added to the shaft until the whole assembly was correctly assembled. To solve the worn bushings, Sulzer upgraded the PEEK design to ceramic to further reduce wear. Seals were reconditioned to OEM standard and the bearing seating area repaired. Each pump motor was refurbished in-house too as part of the turnkey project. The pumps were all tested, delivered, installed and commissioned in-line with the proposed maintenance plan.
Right on time
The high-performance coatings greatly extended MTBF for the pumps, helping to secure platform uptime, productivity and profitability. Long-term, this increased durability will reduce maintenance requirements and provide operational cost savings - adding value to operations. Furthermore, the upgraded pumps were reinstalled into the platform quickly with no modifications to the equipment footprint. The retrofit project offered reduced lead times compared to new units and is ensuring continued reliable performance and efficiency.
Manish Talwar, Head of Retrofits Asia Pacific for Sulzer, concludes: “With almost 200 years of experience designing and manufacturing high-performance pumps, we have a unique advantage for these retrofits. Our unmatched track record in a wide range of applications proves we can deliver high-quality repairs that will withstand arduous environments in any industry.”
Source: Sulzer Ltd.