Sulzer Inaugurates Pump Production Line and Logistics Center in Kotka, Finland
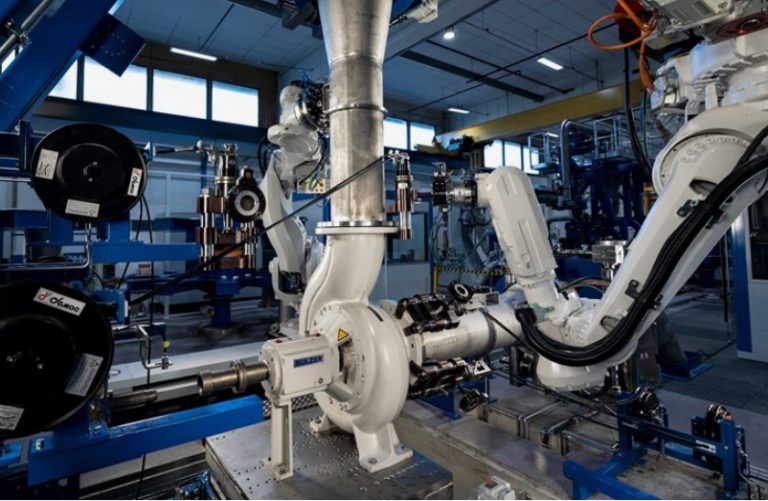
Sulzer inaugurates highly automated and digitized pump production line and logistics center in Kotka, Finland. (Image source: Sulzer Ltd.)
Sulzer has been manufacturing pumps in Kotka for 130 years. Now the company is entering a new era with the new, state-of-the-art pump production line that meets the highest industry standards, alongside excellent ergonomics and safety. The production throughput time of the cutting-edge and energy-efficient equipment will be reduced by 93%. This will translate into far more favorable delivery times for our customers and world-class measurement accuracy and digitized quality inspection will guarantee the highest product quality.
Strengthening Sulzer's entire global supply chain
The automated facilities have been designed to deliver fast and efficient workflows, incorporating digital and lean principles to ensure effective production. A brand-new logistics center provides materials and component handling, streamlining material operations, and contributing to shorter lead times. The increased output from the Kotka factory will strengthen Sulzer’s entire global supply chain.
Sulzer’s factory in Kotka is one of the key providers of configured process pumps, agitators and high-speed turbocompressors for the global market. The facility also comprises industry-scale test beds and research facilities. The factory serves process industry customers in markets such as pulp, paper and board, new wood-based processes, biofuels, sugar and starch, metals and mining, fertilizers, chemical processing, and water treatment.
A significant step in building a sustainable future
“The new production line represents the most advanced technology in the field, and we are excited about the possibilities it offers our customers when it comes to quality and delivery times. Moreover, given that the materials used in our high-efficiency pumps are 99% recyclable, the new facility reflects not only our dedication to quality, but is also a significant step in building a sustainable future that our customers value and our employees can take pride in,” says Veli-Pekka Tiittanen, Head of the Industry Business Unit at Sulzer.
Source: Sulzer Ltd.