Sulzer Delivers Targeted Pump Refurbishment that Achieves 50% Cost Saving
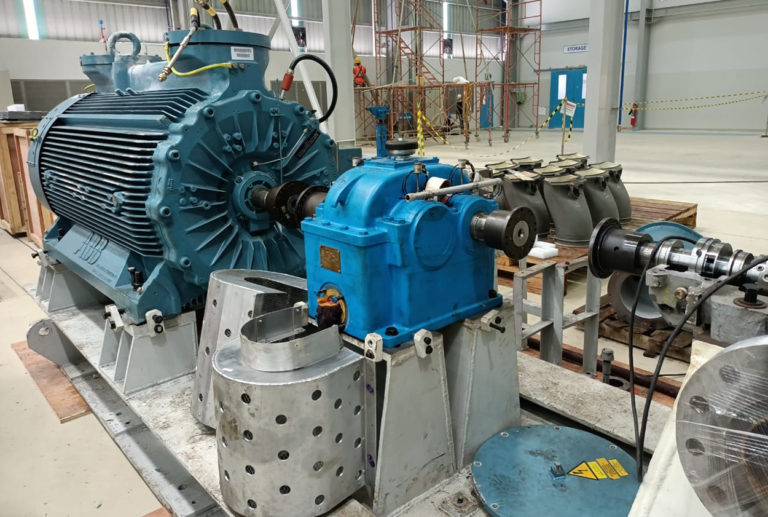
The old diesel drives and steam turbines were replaced with new electric motors and gearboxes to deliver the desired speed increase. (Image source: Sulzer Ltd.)
The targeted overhaul program helped the equipment attain a new operating point, providing a 50% cost saving compared to purchasing new units and 5-month overall lead time reduction.
Recently, the refinery has undergone a long-term, facility-wide upgrade project designed to maximize production capacity and meet the future energy demands of Indonesia.
The right expertise for legacy equipment
As part of this initiative, the equipment promptly identified for modernization included eight diesel pumps used to transfer fuel from the refinery. The pumps were using six diesel drives and two steam turbines for power. One of the assets dated from 1975, and there was no existing documentation available on site for any of the units.
As a result, operators were unsure how to improve the performance of the pumps to meet the increased fuel demand while safeguarding reliability. Consequently, the engineering contractor approached a number of pump specialists to see how a new duty point could be effectively achieved.
Finding a service provider who can work effectively with older equipment is often a challenge. However, after a rigorous tender process, the contractor selected Sulzer as its unrivalled engineering capabilities meant that it rose above the competition. Utilizing its knowledge as a global pump original equipment manufacturer (OEM), Sulzer is an expert in carrying out retrofits and refurbishments for equipment used in a wide range of applications. This ensures that higher reliability and efficiency standards can be achieved with optimized overhaul projects. Consequently, Sulzer engineers have unrivalled experience in working with legacy pumps.
Local expertise with global support
Sulzer’s local service center in Indonesia provided seamless access to engineering services and the company’s wider global network. This worldwide support proved crucial in collating all the necessary information and expertise to deliver this project effectively.
To overcome the lack of documentation, the Indonesian team contacted Sulzer Pumps UK. The UK team was able to source all the documentation and data for the diesel pumps installed at the refinery.
With this information, the team in Indonesia closely collaborated with the Sulzer Pumps engineering team in the U.S.A. Building upon this, the U.S.A team also delivered additional training to the customer’s team.
Throughout the project, the Singapore Service Center acted as a central hub for all the teams to organize their findings and recommendations. After close international collaboration, it was clear that the new duty point could be met without any modifications to the pumps themselves.
Gearing up
Rather than modifying the pumps, new gearboxes would be used to increase the speed of the pumps to reach the new process requirements, which could be achieved well within the performance envelope of the units.
Armed with this information and a plan of action, Sulzer Indonesia carried out detailed inspections of the units. The team then conducted a full refurbishment of the eight pumps, bringing them back to as-new standard. New skid frames were fitted with efficient electric motors connected to gearboxes to deliver the desired speed increase, replacing the old diesel drives and steam turbines. To ensure a complete drivetrain package, Sulzer also installed new couplings and lube oil systems. The rebuilt skids were a plug and play solution, allowing simple reconnection with existing refinery pipework, unlocking a quick installation and minimizing time on site.
This approach not only ensured a reduced lead time on the project, but also meant the retrofit could be carried out at 50% of the cost of sourcing new pumps. Furthermore, the retrofit offered a time saving of five months compared to delivering replacement units. No modifications to the pumps themselves also allowed easy plug and play reintegration into the surrounding process equipment back at the refinery once work was complete. What had initially been a complex problem was solved with a straightforward solution that saved time and costs.
Meeting demand reliably
Updating the drive technology for the pumps ensured that the new duty point was also met with increased efficiency. By using the operational data for the pumps, the complex new performance requirements could be met with speed increasing gearboxes, with future system reliability assured. The exceptional engineering capabilities at Sulzer ensured that a complex application challenge was met with a faster solution that offered increased value compared to ordering all new pumps.
The think global – act local philosophy at Sulzer enabled seamless information sharing and collaboration during the project. The great depth of Sulzer engineering knowledge and talent available through its global network meant that the customer had access to the very best technical support, which helped to solve their complex problem in the most straightforward manner. As a result, a cost-effective and efficient solution was provided to the refinery, ensuring that it could deliver increased fuel supply while also safeguarding availability.
Source: Sulzer Ltd.