Side Channel Pump for the Safe Transport of Ammonia
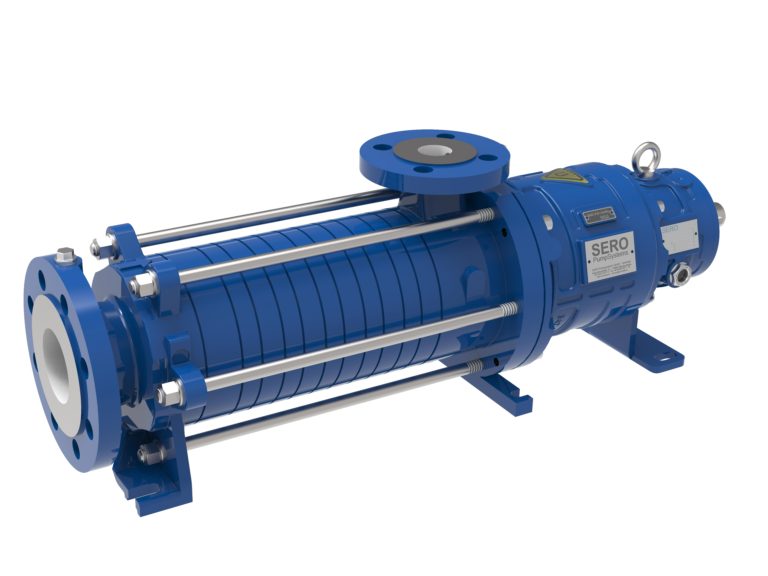
SERO PumpSystem’s self-priming side channel pump SEMA is the ideal solution for the reliable and efficient transport of ammoniak NH3. (Image source: SERO PumpSystems GmbH)
The leak-proof “mag-drive” sealing arrangement guarantees a high level of reliability and safety. The SEMA-S has extremely low NPSH requirements as well as high entrained gas capabilities to ensure maximum operational functionality. Pump users and operators will also benefit from SERO‘s modular design principle allowing for optimal adaptation of flow and head conditions.
For pumping services involving ammonia, a strong-smelling, toxic, colorless, water-soluble liquid, the SEMA-S sealless design provides a safe, environmentally sound solution. Depending upon the type of ammonia, aqueous or anhydrous, the materials of construction can be either ductile iron or all stainless steel.
The sealless magnetic coupling design eliminates the use of mechanical seals in the pump and the inherent problem of seal leaks and the release of fugitive emissions. Safety is greatly enhanced along with increased reliability.
The mag coupling creates contactless torque transmission from the motor to the pump via permanent magnets attached to the motor shaft and the pump shaft. A containment can separates the magnets and enables the pump to be completely sealed off from the surrounding environment. The corrosion resistant sealless mag drive system ensures zero-leakage! Consequently, operating or service personnel are protected from exposure to ammonia and HSE concerns are thus eliminated.
A service where the SEMA-S can be utilized is pumping ammonia where the ammonia acts as a transport medium for hydrogen. Given the rapid development of fuel cell technology, this application will gain new significance. The SEMA-S hydraulic flow range of 0.3 m3/hr to 42 m3/hr with pressures up to 40 bar fits nicely into the fuel cell design criteria.
Low NPSH values simplify suction inlet design requirements
The Model SEMA-S has many unique capabilities and one of the most significant is its low NPSH requirements. The low NPSH first stage impeller in conjunction with the liquid ring vacuum effects of the succeeding side channel stages, all work together to produce very low NPSH values and prevent cavitation. Values as low as 0.35 m depending upon operational speed. This allows for more flexibility in suction piping design and vessel or tank placement. It can be exceedingly important when pumping volatile process fluids such as ammonia.
Source: SERO PumpSystems GmbH