Editorial: Canned Motor Pumps for Ammonia Applications
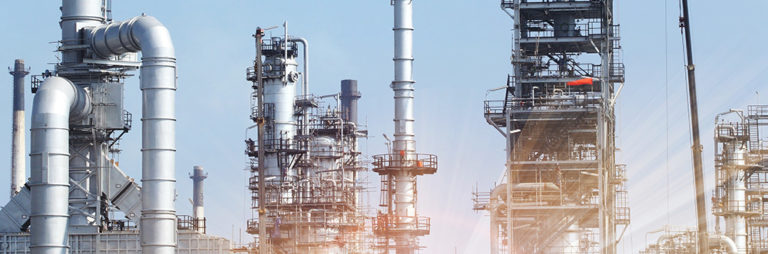
Spaltrohrmotorpumpen für Ammoniak-Anwendungen. (Bildquelle: Hermetic
With its CAMT and CNF series, the canned motor pump specialist provides safe and durable units that offer system operators a number of advantages for the production process of ammonia when compared to conventional centrifugal pumps. While the CNF series with an integrated auxiliary impeller and internal fluid return system is specifically designed for pumping liquefied gases as well as boiling media and condensates, the tandem configuration of the CAMT series offers an effective solution for pumping small quantities at high delivery heads, as is typically the case when pumping liquid ammonia into a storage tank.
Application areas
Ammonia, the chemical compound of nitrogen and hydrogen, with the formula NH3, is, with an estimated 180 million tons a year, one of the most frequently produced chemicals world-wide (figure from 2021). Roughly 75 percent are being used for the production of fertilisers. Various substances derived from ammonia serve as starting materials for polymers. As a fire-resistant, nonhazardous refrigerant with regard to the greenhouse effect, ammonia is being used in refrigeration technology. In the quest for alternative fuels, ammonia is also increasingly brought up as a topic for discussion as a potential hydrogen carrier as well as an alternative to hydrogen.
Production of ammonia
Ammonia is produced from hydrogen and nitrogen. A synthesis process according to the Haber-Bosch method is applied most commonly. In recent years, however, research has increasingly focused on alternative processes since high carbon dioxide emissions and a high energy consumption are associated with the Haber- Bosch method. The starting materials for ammonia synthesis are gained by way of a process known as steam reformation. The resulting synthesis gas mainly consists of hydrogen and nitrogen.
Ammonia synthesis
In order to synthesise ammonia, a turbo compressor is used to compress the synthesis mixture to 250 bar to 300 bar, so that the actual ammonia synthesis can take place in the reactor at 400 °C to 500 °C. The reactor catalyst is made of specially prepared iron, which contains traces of potassium, aluminium, calcium, magnesium and oxygen. This is where the diatomic oxygen molecules and hydrogen molecules split and chemically bond with an atom of the other element to form ammonia. Ammonia can then be continuously removed from the process, and continually cooled in a heat exchanger with water, supplied gases and / or other process flows. Due to being cooled down, the ammonia condenses and can be removed from the cycle by means of a high-pressure separator. The non-reactive oxygen components and hydrogen components are brought back to operating pressure and added to the synthesis gas. Sometimes the produced ammonia is distilled to increase its purity. The ammonia is then cooled so that it becomes a liquid that can be stored in large tanks.
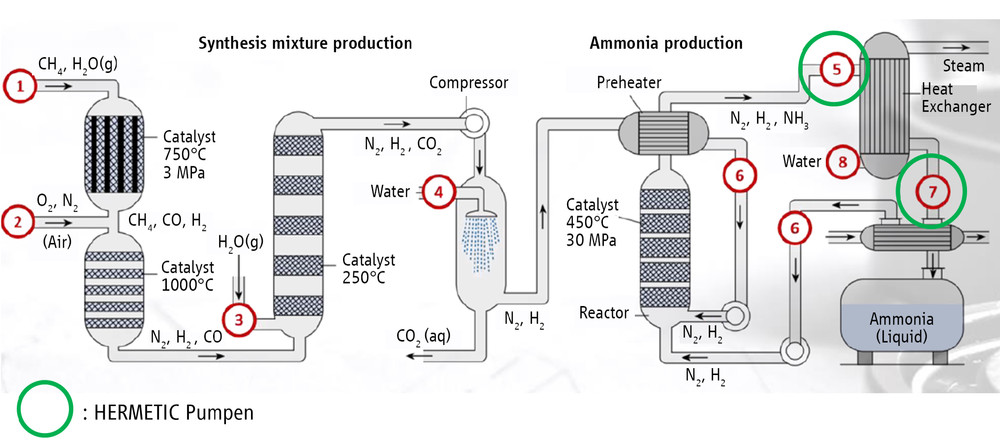
Placing high demands on the equipment used
The physical properties of ammonia (low viscosity and density, low temperature) are a challenge for pumps. High corrosivity and the harmful or toxic property of ammonia require high material resistance and leak proofness of the equipment used. Since canned motor pumps are hermetically sealed and offer a high level of safety, they are particularly well suited to this purpose. This holds true especially when discharging the condensed ammonia (5) and pumping the liquid ammonia into the storage tank (7).
Completely leak-free, low-wear and low-maintenance pumping technology
In contrast to conventional centrifugal pumps with mechanical seals, canned motor pumps do not have any vulnerable dynamic seals. Instead, canned motor pumps have a second hermetic safety containment that prevents any leakage of pumped media and emissions. The design-based omission of wear-prone components such as shaft seals, couplings and roller bearings ensure a high degree of operational safety, almost negligible wear and the best MTBF (Mean Time Between Failure) values compared to other pump technologies.
Compact pumping solution for discharging condensed ammonia
A HERMETIC CNF-type canned motor pump is used to discharge the condensed ammonia. The CNF series is the version that is suitable for liquefied gases, boiling media and condensates with a vapour pressure of up to 10 bar. With an integrated auxiliary impeller and internal fluid return, it is suitable for conveying liquids close to vapour phase. The range of applications for CNF variants includes delivery heads of up to 220 m, flow rates of up to 1800 m³/h, fluid temperatures from –120 °C to +360 °C, power ratings of up to 220 kW and pressure ratings of up to 25 bar.
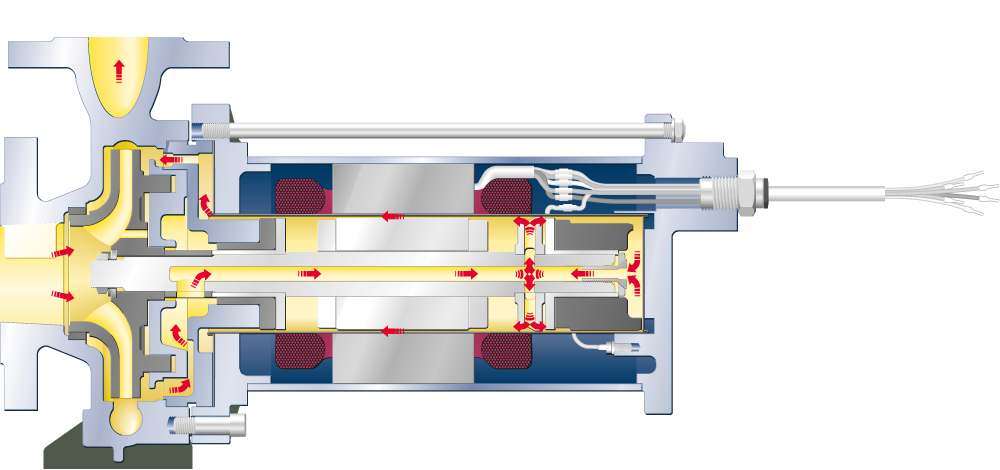
The present system uses a single-stage canned motor pump of type CNF 65-40-200 with a flow rate of 15 m³/h and a delivery head of 45 m. The N34L-2 motor provides a shaft power of 10.5 kW. The operating temperature is 40 °C and the vapour pressure is 1.2 bar. Thanks to the internally recirculation, a partial flow for cooling the motor and lubricating the plain bearings is branched off at the periphery of the impeller and, after flowing through the motor, it is conveyed back to the pressure side. An auxiliary impeller is used to increase the pressure to prevent the fluid from changing to the gaseous state due to the pressure loss downstream of the impeller.
Conventional pumps require external recirculation ducts for this purpose. A higher risk of leakage exists in this case since more seals, flanges and pipes are required. Plus, the cost of installation is also higher. With a recirculation within the pump, HERMETIC offers a slim pump solution that requires little installation space and effort. The canned motor filled with liquid is wear-free and maintenance-free during continuous operation thanks to hydrodynamic sleeve bearings.
Partial flow return to the pressure side
![]() |
|
Pressure-temperature diagram
![]() |
|
Attractively priced and quickly available in the V-line modular system
The CNF series is available with the most popular pump/motor combinations in the HERMETIC V-line pump concept. With standardised assemblies, the V-Line pump concept follows the modular approach of plant engineering. There is a choice of canned motor pump variants with different hydraulics, motor ratings and material versions including matching monitoring technology. The range of applications for CNF variants includes delivery heads from 12 m to 145 m, flow rates from 1.5 m³/h to 130 m³/h, fluid temperatures from –50 °C to +180 °C, power ratings from 6.0 kW to 33 kW and pressure ratings of up to 16 bar.
Within these parameters, many pump-motor combinations can be configured with just a few clicks using the online “HERMETIC Expert Tool”. Thus, optimized delivery times from 8 to 12 weeks are possible.
Multi-stage, tandem design ensures reliable delivery into the storage tank
Frequently, high delivery heads have to be negotiated to pump liquid ammonia into large storage tanks. Good efficiency for pumping tasks that involve small quantities to be pumped from great pumping heads can only be achieved with multi-stage centrifugal pumps. In the present system, a six-stage canned motor pump of type CAMT 44/6 in a tandem configuration ensures that the liquid ammonia is reliably and safely pumped into the storage tank. At a flow rate of 40 m³/h, a delivery head of 300 m has to be managed. The N80rm-2 motor has a shaft power of 57 kW. The operating temperature is 15 °C and the vapour pressure is 1 bar.
Multiple stages with a single-side bearing arrangement pose problems with regard to vibrations and shaft deflections. The perfect solution for this type of application was found with the aid of a tandem configuration. One three-stage centrifugal pump each, with the same direction of rotation, placed upstream and downstream of the canned motor results in the shaft not being loaded on one side only. The entire pump delivery flow is conveyed by the priming pump via the rotor chamber to the pump on the pressure side, whereby the main share of the pump delivery flow is guided through the hollow shaft while a small share is routed through the rotor-stator gap. The advantages of this type of design are a short set of rotors (bending arms) and an ideal bearing arrangement for the entire shaft.
HERMETIC technologies offer a high level of process reliability and low life cycle costs
Whether configured as a modular pump from the V-line concept or individually engineered, every canned motor pump from HERMETIC features sophisticated technologies. These include, for example, the unique ZART principle by HERMETIC. If the pump is running at the duty point, there is no contact between rotating parts. The complete compensation of axial forces in conjunction with hydrodynamic plain bearings guarantees an extremely high level of reliability in the processes implemented by the operators. Life cycle and operating costs for the pump can thus be significantly reduced for the production of ammonia.
Source: Hermetic-Pumpen GmbH