Safe Pump Technology from HERMETIC Contributes to Carbon Capture and Storage (CCS) Value Chain
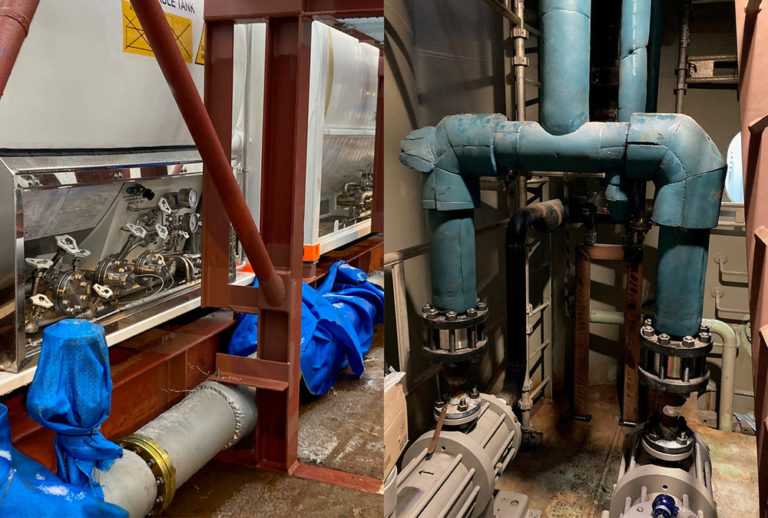
HERMETIC canned motor pumps in use in project “Greensand” (Image source: Hermetic-Pumpen GmbH)
Canned motor pumps from HERMETIC-Pumpen GmbH are used within the scope of the CCS value chain, which involves the separation of carbon dioxide, its transportation and the geological storage of CO₂ below the seabed. Canned motor pumps are used to ensure the operational reliability of the CO₂ pumping process from the ships to the injection platform. In addition to the leakage-free, compact design of this pumping technology, the pump specialist’s many years of experience in managing the challenging properties of CO₂ as a medium were the decisive factor in favour of HERMETIC. The modular pump concept of HERMETIC’s “V-Line” enabled fast delivery times.
The consortium behind “Project Greensand”1 led by INEOS and Wintershall Dea demonstrates for the first time the feasibility of geological CO₂ storage, including CO₂ separation at the location of INEOS Oxide in Belgium, transnational transportation of the CO₂, and final safe and permanent geological storage of the CO₂ in the offshore Nini field, operated by INEOS in the Danish North Sea.
Project Greensand – the value chain
When removing carbon dioxide from an incineration plant, the CO₂ is separated from the flue gas and liquefied. To this end, the carbon dioxide is first heated, then compressed, and finally chilled. The CO₂ is carried by tanker lorries to a transport ship, which transports the liquefied CO₂ to the Nini field. From the ship, it is pumped to the injection platform, from where it is sent underground about 1,800 metres deep below the seabed into a sandstone reservoir. A canned motor pump from HERMETIC-Pumpen GmbH is used to pump the liquid CO₂ to the injection platform.
The challenge of CO₂ as a medium
The primary difficulties are the pressures and temperatures involved in pumping CO₂. The CO₂ liquefication process takes place at a compression pressure from 14 to 20 bar and at low temperatures ranging from –40 to –25°C. The liquid CO₂ in the tanks must be chilled and kept at a low pressure below 20 bar to maintain its liquid phase. Then the liquid CO₂ is pumped to the injection platform at temperatures from –30°C to –40°C. A high risk of gas formation in the pump and dry running are associated with the low temperature in combination with the relatively high vapour pressure of CO₂. For the selection of technology and design, these are the points that require close attention.
Special requirements of the CCS project
The goal of Carbon Capture and Storage initiatives is the reduction of CO₂ emissions into the atmosphere. The required separation of CO₂, its liquefication and transport are energy-intensive processes, however. For this reason it is imperative to ensure that any leakage along the CCS value chain is prevented. Otherwise, in addition to failing to reach the original goal, a high expenditure of energy without any relevant benefits would be the result. The requirements to be met by the equipment used are correspondingly high, which is why hermetically sealed pumps should be given preference over conventional pumps.
CO₂ is a health hazard and high levels of it are lethal. These are good reasons for ensuring absolute leak-tightness of the equipment to counteract any dangers for the personnel responsible in the pump chamber. Other process safety requirements within the scope of the CCS value chain involve a low MTBF of the pump and hence the meeting of exacting reliability standards.
Proven pump technology for pumping CO₂
Since canned motor pumps are hermetically sealed and offer a high level of safety, they are particularly well suited to this purpose. Unlike conventional centrifugal pumps with mechanical seals, canned motor pumps do not require any dynamic seals. Instead, canned motor pumps have a second hermetic safety containment that prevents any leakage of pumped media and emissions.
A canned motor pump of the type CAM 32/3 from HERMETIC-Pumpen GmbH is used in project Greensand. This pump series has been optimised for pumping liquefied gases and it has been used in the refrigeration industry a thousand and one times whenever the reliable circulation of natural refrigerants such as CO₂ and NH₃ was at stake. A three-stage design was selected to overcome the pumping head.
Long service life, compact, wear-free unit
This pump-motor combination in a compact unit eliminates the risk of incorrect shaft alignment. There is no need for a mechanical coupling and coupling guard as well as the often complex base plate design. Moreover, when compared to a pump with an external motor, the space requirements are cut in half. This is an important criterion for deployment on a transport ship.
The hermetically sealed design requires the arrangement of bearings in the pumped liquid.
The bearing pairings were specifically designed for this application and made from materials based on tungsten carbide (W5) and silicon carbide (SiC30). Mixed friction conditions, which occur, for example, when starting and stopping pumps, are very easy to control. Furthermore, SiC30 is also resistant to thermal shock, chemically largely inert and blister-stable (no blistering on the material surface) as well as abrasion-resistant.
The HERMETIC technology “ZART” (Zero Axial and Radial Thrust) ensures that the rotor unit runs without contact and wear. It is based on comprehensive axial thrust balancing in conjunction with hydrodynamic sleeve bearings.
All components correspond to the required pressure rating. The pump design offers a long service life and absolute reliability with low-viscosity media. This HERMETIC pump thus provides an alternative pump for the CCS value chain that is hermetically sealed, more reliable and safer compared to magnetic drive pumps or centrifugal pumps with mechanical seals.
HERMETIC V-Line: Fast delivery times thanks to pre-fabricated components
In addition to the technical pump properties, the fast delivery time was also a decision-making criterion for the consortium to select the pump supplier.
HERMETIC has many years of experience in handling CO₂ and it offers the largest pump portfolio for refrigeration-relevant applications, regardless which medium is used. HERMETIC pursues a modular approach in equipment engineering with its “V-Line” pump concept. Thanks to standardised assemblies for the most common pump-motor combination, a V-Line pump can be delivered in a matter of a few weeks. The modular concept enables short-notice adaptation for major or minor change requests. For project Greensand, HERMETIC was able to draw upon its “CAM” type pump-motor combination. The wide performance range of the V-Line in conjunction with an automated design process and modern lean manufacturing made it possible to deliver an optimally configured standardised canned motor pump in a matter of a few weeks. Without exception, all pumps meet the high HERMETIC quality standards, including the unique ZART® (Zero Axial and Radial Thrust) principle for contact-free and wear-free operation.
¹ About project Greensand:
The consortium behind Project Greensand involves 23 organisations experienced in carbon separation and carbon storage from the fields of business and science, government agencies as well as startups. The project is supported by the Danish state through the Energy Technology Development and Demonstration Program (EUDP). CCS is considered a key technology to reaching the objective of net zero emissions in Denmark by 2045.
Source: Hermetic-Pumpen GmbH