Raízen Selects Sulzer for Next Generation Biofuel Production
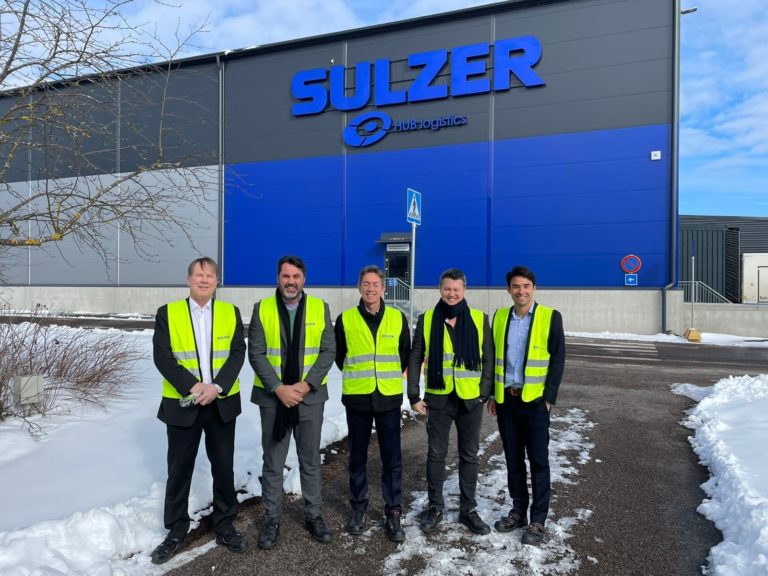
Henrique Nakamura and Marcelo Mancini from Raizen visiting Sulzer factory in Finland with Veli-Pekka Tiittanen, Stefano Sampaolo and Michael Yang (Image source: Sulzer Ltd.)
In many markets worldwide, it has become standard practice to mix a fraction of ethanol into gasoline, helping to reduce the carbon footprint of road transport. Energy companies have plans to go further too, creating fully renewable biofuels that can be used as drop-in replacements for their fossil-based predecessors. Since 2022, for example, Shell has been using bioethanol as a key ingredient in the 100% renewable race fuel that it supplies to the NTT IndyCar series.
Much of that ethanol is made by Raízen, a joint venture between Shell and Brazilian sugar and energy conglomerate Cosan, which produces around 2.5 billion liters of the material from sugarcane in a network of plants across the country. Now, with global demand for bioethanol expected to grow at over 14% per year, the company is expanding its production capacity with the introduction of new second-generation ethanol technology.
Energy from waste
While Raízen’s conventional bioethanol plants use raw sugar cane as their primary input, E2G facilities are designed to process bagasse, the waste material left over after the manufacture of sugar or ethanol from cane. Putting bagasse to work in the production of ethanol has the potential to increase overall yield by 50%, and this ethanol has an even lower carbon footprint than conventional product, creating 97% lower greenhouse emissions than gasoline.
Sulzer has been working on pumping requirements for the E2G technology with Raízen for more than twenty years now. The company has supplied a range of pumps for pilot plants, and the two companies’ engineering teams have worked closely together to resolve the complex technical challenges involved in transforming bagasse into useful fuel.
Large-scale processing of sugar cane wastes is very demanding. The bagasse material is extremely fibrous, and the hot slurries used in bioethanol production are also very acidic. They also contain significant quantities of abrasive sand. Together, those conditions make for very difficult handling: Pumps, pipes and valves in E2G plants are susceptible to blockage, corrosion and early failure.
Demanding environment
To produce pump designs that could meet the needs of the new E2G facilities, Sulzer drew heavily on its experience in other demanding industry sectors. The fibrous nature of the bagasse slurry has much in common with materials used in the pulp and paper industry, for example. Sulzer has also developed a range of specialist materials and coatings to improve pump durability in corrosive and abrasive environments seen in the mining and metals sector. Energy efficiency was another key priority for Raízen, which required careful attention to the hydraulic design of the entire system.
As the E2G project moved from development to commercialization, all this experience was critical in helping Sulzer win a competitive tender to supply pumps to Raízen’s production sites. The final scope of supply includes Sulzer’s MCE/WPP pumps in special metallurgy and AHLSTAR A pumps for general process and utility applications across the sites.
Along with the strategic partnership, Sulzer has been recognized for achievements in areas that correspond with Raizen’s corporate values. Out of six thousand companies in Raizen’s vast supplier network, Sulzer was awarded for setting an outstanding example in embracing environmental and social governance values. The award is a significant accolade for Sulzer’s corporate responsibility efforts.
Ongoing support
For Raízen, sourcing all the major pumps for the E2G project from Sulzer offers several advantages beyond the proven technical capabilities of the pumps. The contract has simplified procurement for the new project and allows the facilities to keep spare parts inventories to a minimum. The AHLSTAR is a multi-role pump with a modular construction that enables it to be customized to different applications, for example. Sulzer Industry team in Brazil will provide maintenance and spare parts support for each facility, to ensure availability when required. Those capabilities will be critical to the successful operation of the E2G plants.
Source: Sulzer Ltd.